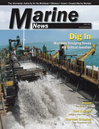
Page 36: of Marine News Magazine (June 2013)
Dredging & Marine Construction
Read this page in Pdf, Flash or Html5 edition of June 2013 Marine News Magazine
W&O has also been named as PG Marine?s Representative for their full range of equipment in this territory.? PROVEN , APPROVED EQUIPMENT With 24 retro t installations of BWT systems on Offshore Supply Vessels already under its belt, Hyde Marine is one of the more familiar names in the domestic BWT game. And, for good reason. In the ballast water treatment business since the very beginning, the chemical free Hyde GUARDIAN BWTS uses ef- cient ltration and ultraviolet disin- fection to prevent the spread of inva- sive species from port to port. In April 2013, the Hyde GUARDIAN BWTS earned the Alternate Management System (AMS) approval from the United States Coast Guard (USCG). It also received International Mari- time Organization (IMO) Type Ap- proval in April 2009 and has Type Ap- provals from several Class Societies. It was also an early player in the Coast Guard?s Shipboard Technology Evalu- ation Program (STEP) program. LOOMING DEADLINES: NO TIME TO WASTE A December 2013 BWT installa- tion deadline for newbuild tonnage is just around the corner and in January 2014, vessels entering the shipyard for a major drydocking will have to com- ply by the time of departure. And, although some exemptions apply, it clear that the time for hesitation is over. Jim Mackay told MarineNews in May, ?In a few months, this will be triage.? Mackay expects Hyde Marine to be quite busy in the immediate fu-ture and then, steady in terms of busi- ness in the newbuild markets. And, while that may sound good for Hyde Marine and its distribution partners, it spells trouble for those operators who are not already making prepara- tions for installation and compliance. Mackay cautions potential customers: ?Do not make an uninformed deci- sion at the last moment.? He adds that the key to success includes getting framed agreements early on. This allows the BWT manu- facturer ? no matter who you choose ? to plan production. Mackay adds, ?Committing as early as possible ben-e ts both parties.? Todd Nestel, W&O?s Integrated Solutions Manager echoed those senti- ments, saying, ?Fleets with 15-20 ves- sels of one class would do well to get a couple of boats commissioned early, and then proceed with the eet in succession, using lessons learned. You want a consistent approach; the same, standardized equipment for each class of boat.? But that?s only possible if the manufacturers, shipyards and design rms have early notice of the plan. For newbuilding, keeping up with demands of a series-build client will be important. Nobody wants to put three different types of systems into one class of vessel. Beyond this, a bet- ter rate will probably be negotiated for a series BWT deal than one-off deals. But, unless the systems are readily available for shipbuilders when they need them, planned for in advance, the one-off purchase may become the practice of the day. And, with every- one trying to achieve compliance at once, that will inevitably mean delays.SHIPYARDS ? THE THIRD LEG OF THE BWT STOOL Bill Young with International Ship Repair & Marine Service (ISR) also weighed in. ISR operates shipyards in Galveston and in Tampa. Young says, ?We?ve been looking at this for more than two years. Most operators will want to do it in drydock, but that will require an upfront approach ? you must prepare in advance for that visit.? But, he adds, ?The recent down econ- omy affected the impetus to get pre- pared early, because that costs money up front.? On the other hand, for those operators who continue to sit on their hands, trying to get it done at the last minute may even be more expensive. And, he says, shipyards today are still not elding a lot of BWT inquiries. For his part, Young and ISR have a good relationship with W&O and Hyde, but he?ll work with owners to put in the right equipment for the speci c vessel; no matter which BWT solution they choose. Owners can g-ure on at least 9 months advance no- tice to allow for planning and design work and about 4 to 5 months to de- liver equipment. Aiming to speed up that process, Hyde itself employs 3D design technology which allows pre- made piping which can be assembled on board, instead of having the ves- sel endure a lengthy and sometimes messy manufacturing process. mmÜÜWW==EEPPPPTTFFOOPPTTJJRRMMNNNN ccññWW==EEPPPPTTFF==UUPPTTJJTTTTUURRbbWW==ÜÜÉÉ~~ÇÇÑÑääììëëÜÜÉÉêê]]~~ÜÜÉÉ~~ÇÇíí~~ååââKKÅÅççããttÉÉÄÄWW==ïïïïïïKK~~ÜÜÉÉ~~ÇÇíí~~ååââKKÅÅççãã + +==``ÜÜÉÉããááÅÅ~~ää==ooÉÉëëááëëíí~~ååíí== + +==ooììëëíí==CC==``ççêêêêççëëááççåå==mmêêççççÑÑ==== + +==llÇÇççêê==ccêêÉÉÉÉ== + +==aaììêê~~ÄÄääÉÉ== + +==``ççããéé~~ÅÅíí==== + +==iiááÖÖÜÜíí==ttÉÉááÖÖÜÜííqqóóééÉÉ==ffff==ppÉÉïï~~ÖÖÉÉ==qqêêÉÉ~~ííããÉÉååíí==mmää~~ååíí==EEppqqmmFFrp=`ç~ëí=dì~êÇ=`ÉêíáÑáÉÇ ~åÇ=fjl=OMNM=^ééêçîÉÇ qqÜÜÉÉááëë==ÅÅççååëëííêêììÅÅííÉÉÇÇ==ççÑÑ==eeÉÉ~~îîóódd~~ììÖÖÉÉ==iiii==mmççääóóÉÉííÜÜÉÉääóóååÉÉ==ììëëááååÖÖ==ííÜÜÉÉ==ããççëëíí~~ÇÇîî~~ååÅÅÉÉÇÇ==ëëíí~~ííÉÉJJççÑÑJJííÜÜÉÉJJ~~êêíí==êêççíí~~ííááççåå~~ääããççääÇÇááååÖÖ==ééêêççÅÅÉÉëëëë==ÅÅêêÉÉ~~ííááååÖÖ==~~==ììååááíí==ííÜÜ~~íí==ááëëWW + +==iiççïï==jj~~ááååííÉÉåå~~ååÅÅÉÉJune 201336 MNMN June2013 Layout 32-42.indd 36MN June2013 Layout 32-42.indd 365/30/2013 11:13:15 AM5/30/2013 11:13:15 AM