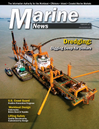
Page 43: of Marine News Magazine (February 2015)
Dredging & Marine Construction
Read this page in Pdf, Flash or Html5 edition of February 2015 Marine News Magazine
SAFETY “We like to have control over the production of critical components wherever possible. We ? nd it is easier to control processes and ensure quality when the product is made under our roof so that is what we do whenever possible.” – Ben Jordan, Rapp Marine Senior Engineer mally documenting all of the checks and balances of the de- Standardized Features Customized sign and manufacturing process, to ensure that all of quality In addition, Rapp Marine has leveraged its QMS pro- standards are being met. These checks and balances include cesses to better capture the speci? c requirements of each documenting employee competency, ensuring that vendors customer. With long standing customers in the ? shing, off- of critical parts meet quality standards, and heading off po- shore, and LNG markets, Rapp Marine is often depended tential issues through robust preventative maintenance. upon to provide affordable, robust solutions to meet its
Cranes built by Rapp Marine may be certi? ed to API customers’ requirements. One example is a new crane de- spec 2C, a unique certi? cation known as “monogram- sign developed for Foss Maritime, which is building a new ming” that may be applied by crane manufacturers that Fireboat 20 and its sister ship for the Port of Long Beach. meet these rigorous quality standards. The API 2C certi? - The crane features a personnel basket that is self-leveling cation provides the end user with an easy way of knowing via a master-slave cylinder system. The basket can also be that the crane that they are purchasing has met the set of manually tilted and slewed, its underside is out? tted with requirements that are outlined by API, and that API has LED ? ood lights and a camera.
made sure that the manufacturer has gone through inten- In order to ? t the crane into the tight space allotted on sive audits to maintain the certi? cation. the vessel, but also be capable of achieving the required
Since initially implementing the quality system over reach, Rapp engineers came up with a double-telescopic 6 years ago, Rapp Marine has realized a payoff for both boom. The crane can be controlled via wireless remote, themselves and the end user. Creation of cranes meeting basket controls, or from the platform. A telescopic ladder such high quality standards has resulted in units that pro- is mounted to the booms of the crane.
vide reliable service for an extended lifetime. Beyond this, Rapp Marine features standard model cranes including internal warranty related costs have almost disappeared. ? xed boom, telescopic, knuckle, double-telescopic, and
And a further bene? t of the quality program implementa- knuckle extension type cranes from two to 100 tons in ca- tion is that should an issue occur with a particular crane, pacity. Typically, the standard crane models are customized the documentation allows review of similar cranes that according to each customer’s speci? c application. Crane are currently in use which potentially may suffer a similar projects with lift capacities up to 100 tons are fabricated problem. Proactive repair and maintenance of any identi- in-house in the Seattle, WA, production facility in order to ? ed issue can result in big savings in both costs as well as protect the quality of the product. The fabrication of any the safety for the crew and the vessel. crane with lift capacity above 100 tons is outsourced to a 43 www.marinelink.com MN