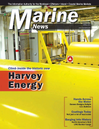
Page 48: of Marine News Magazine (April 2015)
Shipyard Report: Construction & Repair
Read this page in Pdf, Flash or Html5 edition of April 2015 Marine News Magazine
ech file
T
Access the Advantage:
Remote Control
Welding Technology
Safe, ef? cient and pro? table welding involves many variables, all of which can be had by embracing remote controlled welding techniques and equipment.
By Jim Rappl, Product Manager, Miller Electric Mfg. Co. f? ciency, safety and pro? tability are important to set of welding parameters enables the welding operator to any company, but especially to a welding operation. stay where the welding is done, reducing the need to access
EIn addition to general best practices and welding op- controls in inconvenient locations. In reality, a company erator training, there are equipment advancements that can may be sacri? cing quality and productivity by settling for help meet quality and production goals, while also help- less-than-optimal settings. ing keep welding operators safer on the job. Remote con- For example, it’s possible that the welding operator may trol welding technology is one of those advances. Remote have selected a lower output setting for out-of-position control welding technology allows welding operators to set welds and is using that same setting for welding in the ? at/ welding parameters at the joint without the need to carry, horizontal position. Because it is actually possible to oper- route, troubleshoot and maintain expensive control cables ate at higher output settings and travel speeds for ? at/hori- — all while delivering consistent welding performance. zontal applications, the net result is the welding operator is losing time by welding with less productive weld settings.
O W P That can lead to costly rework, too, since too cold of a weld
PTIMAL ELDING ARAMETERS
For any application, following proper welding param- setting, for instance, can lead to poor fusion and/or poros- eters is critical to achieving high weld quality and produc- ity, especially when welding over pre-construction primer. tivity, as is employing proper and consistent techniques. Remote control technology enables the welding operator
On some jobsites, however, that goal can sometimes be to set welding parameters at the arc without a control cord compromised by the expanse of the location. Welds in and without using wireless controls that require batteries or some fabrication, construction and shipbuilding environ- line-of-sight for operation. This technology uses the exist- ments are often made at extended distances from the weld- ing weld cables themselves to communicate with the power ing power supply. Because of this distance, portable wire supply, which helps the operator obtain the best welding feeders that do not require a control cable are often used parameters for the desired joint orientation — right at the but up until recently these feeders did not provide voltage weld joint. These optimized settings, when coupled with control. As a result, welding operators often select a single good techniques such as proper travel speed, help produce set of welding parameters that are a “best ? t” to accom- high-quality, properly sized welds at a faster rate. plish all of the joint orientations to be welded. This best Having the proper weld settings can also reduce the cost ? t eliminates the need to travel back to the power source per foot for the welds. In some cases, reducing these costs repeatedly to change weld settings. can add up to thousands of dollars annually per welding
At ? rst glance this approach seems viable. The single operator, delivered back to the bottom line.
Image above: Remote control welding technology allows welding operators to set welding parameters at the joint without the need to carry, route, troubleshoot and maintain expensive control cables — all while delivering consistent welding performance.
April 2015 48 MN