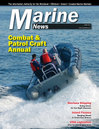
Page 48: of Marine News Magazine (June 2015)
Combat & Patrol Craft Annual
Read this page in Pdf, Flash or Html5 edition of June 2015 Marine News Magazine
PROPULSION annular airfoil which develops thrust from the circulation addressed during testing and it was determined that ef- created by the propeller. The nozzle airfoil has negative (in- ? ciency suffered if the gap was greater than 0.4% of the ward) camber to develop ahead thrust. The shape of the propeller diameter. There are also cavitation effects due to nozzle airfoil can be tailored to the expected ? ow condi- the size and shape of the gap. Another very practical issue tion to achieve maximum performance at the design point for brown water use is the ability for the propeller to shed of the particular vessel. debris. This is largely affected by the tip clearance and the shape of the leading edge of the propeller. Both can be
Inland River Towboats optimized for use in the inland rivers systems.
A key consideration for inland river towboats is the need Integration of a nozzle into the hull is another critical fac- for backing thrust. The Type 19A nozzle was developed to tor for towboats. The outside diameter of a typical nozzle is provide good ahead performance, but backing performance about 20-25% larger than the propeller diameter. In all cases, is sacri? ced. Typically, astern thrust is about 55% of ‘ahead’ the nozzle will be tucked up close to the hull and may be in thrust. There are several factors that cause this loss of astern a tunnel in order to provide suf? cient diameter. And in most thrust, including the small trailing edge radius of the nozzle, cases, the bottom of the nozzle should be at or above the the small diffusion angle of the conical section aft of the baseline of the hull. This likely makes the top of the nozzle propeller and the form of the stern of the vessel itself. The inside the nominal hull line and in some cases, the base of
Type 37 nozzle addresses some those factors and generally the nozzle will have to be ? attened. The upper section of the does provide better backing performance. However, some nozzle must be faired into the hull as reasonably as possible of the ahead thrust potential is lost. But with the ever-in- to avoid cavitation while moving ahead and to minimize creasing use of CFD, it is possible to customize the nozzle ? ow disturbances into the propeller while moving astern. geometry for any operating condition, including the neces- The lower portion must be thick enough to provide ad- sity to have greater backing ability. Off-design conditions equate strength and be well-rounded to minimize ? ow losses.
can also be investigated to determine the effectiveness of the These compromises will reduce the amount of the thrust nozzle in scenarios other than the primary use of the system. produced by the nozzle, but when properly designed, the
When the 19A nozzle was being developed at MARIN, overall outcome should be a more ef? cient operation. a range of nozzle length-to-diameter ratios were tested and Cavitation is as always a key consideration for towboat it was determined that a 0.5 length to diameter ratio was propellers. Nozzle propellers are less sensitive to in? ow optimal. This gave engineers and architects a rule of thumb velocity than open propellers, but blade pressures should for considering nozzles on both new vessel designs as well as be kept slightly lower for best performance. The ability retro? ts. In recent years, other CFD analysis of airfoil noz- of the nozzle to produce some of the thrust does allow for zles indicated that it may be possible to increase overall ef? - smaller diameters to be used for a given power.
ciency with slightly shorter nozzle lengths, with a length to For most ? eets, fuel costs make up a large portion of diameter ratio of about 0.3. The shorter nozzle would make the overhead. The ef? ciency of a properly applied ducted ? tting into an existing arrangement easier and it would re- propulsion system can be a reliable way to keep fuel costs duce clearance problems with rudders in all applications. It lower over the life of the vessel. For the design of new ves- was also found that there may be some bene? t in increased sels with ducted systems, analysis of underwater features, backing performance with a reduced nozzle length. optimizing for any parameters such as ef? ciency or vibra-
The MARIN tests also looked into the effects of propel- tion mitigation, makes a lot of sense. For existing vessels, ler placement within the nozzle. It was determined that evaluation of the current con? guration can determine placing the propeller in the center of the nozzle, relative whether a conversion to a ducted system is feasible. And to the nozzle’s length, provided the best ef? ciency. Other in every case, the propellers can be engineered and built to studies have shown that moving the propeller away from ? t a speci? c system operating in any given condition.
the center of the nozzle, especially forward of the center line, tends to reduce thrust.
John Eckart is the Principle Engineer at HS
In addition to the placement of the propeller in the noz-
Marine Propulsion, LLC. He is a graduate of zle, the clearance between the tip of the propeller blades
Kings Point and the University of Michigan and the inner diameter of the nozzle was also found to be with a degree in Naval Architecture and a critical dimension that has quite an effect on the over-
Marine Engineering.
all performance. Increased tip clearance was speci? cally
June 2015 48 MN