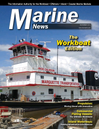
Page 78: of Marine News Magazine (November 2015)
Workboat Annual
Read this page in Pdf, Flash or Html5 edition of November 2015 Marine News Magazine
WORKBOAT EQUIPMENT for its installation. ? ttings, sometimes as much as 25 uct, owner/operators will see reduced
The number one reason that an years. While the initial material costs maintenance costs and additional sav- offshore or workboat operator might may be more than traditional ? ttings, ings from the lower material weight of opt for SeaCor products as opposed to especially with the downturn in the the installed product. traditional, standard ? ttings involves price of copper, the overall lifecycle Another reason to turn to thermo- lower cost of ownership. This thermo- costs are dramatically reduced, begin- plastic couplings for grey, potable, and plastic piping system has a longer life ning with the installation of the mate- sewage lines is the remarkable savings span compared to traditional standard rial. Throughout the life of the prod- in weight that it creates. Steve Hartsaw,
Senior Project Manager of Engineered
Viega features and bene? ts at a Glance …
Solutions at W&O Supply reports, “Based on an actual bill for materials
Copper-nickel alloy (CuNi 90/10) Compatible with existing Viega press tools on a typical OSV system for the grey, (seawater systems) potable and sewage lines, with a change
The only copper-nickel ? tting with Helps reduce installation time up to 90% from steel to SeaCor we found there to double press connection be a 75 percent reduction in material
Makes secure connections in less Easily transition to imperial and metric sizes weight. A complete steel system would than seven seconds weigh in around 10,000 lbs., whereas the complete SeaCor system weighs
Provides safety - no ? re watches or SeaPress product in stock and ready to ship hot work permits just more than 2,500 lbs.”
In this case, time also equals money.
Viega Smart connect identi? es un- Metric/standard ? ttings to match any system
A vessel operator who opts go to Sea- pressed connections
Cor piping and ? ttings (for all appli-
Secure connections made with bat- Innovative tooling allows pressing in tight cations that would allow for such use) tery powered tool areas would be looking at substantial sav- ings in terms of both eliminating hot- work and gas freeing, not to mention down time while the work is accom- plished. In the yard, depending on the type and size of vessel, of course, the time savings alone substantial. For example, a typical OSV employing this product on grey, potable and sew- age lines could expect to expend 298 man-hours that project. According to the Mechanical Contractors Associa- tion, the same job using steel or cop- per materials, might take 1,018 man- hours. Those savings might translate into a win for the vessel owner, the boatbuilder, or both.
W&O’s Hartsaw admits that the apple-to-apples cost comparison is a little harder. He told MarineNews, “The base material costs for SeaCor technology is higher than traditional metal components, especially with the recent drop in Copper. Using the typical OSV system as a baseline for comparison, the SeaCor products are
November 2015
MN 78
MN Nov15 Layout 66-81.indd 78 10/23/2015 2:31:56 PM