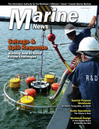
Page 44: of Marine News Magazine (October 2016)
Salvage & Spill Response
Read this page in Pdf, Flash or Html5 edition of October 2016 Marine News Magazine
PROPULSION
Electric Motors for Marine Applications:
Empire Magnetics President Richard Halstead discusses the critical considerations necessary for engines operating in Arctic waters.
By Richard Halstead
A large number of vessels sail in more C G M AONSIDERATIONS FOR ENERAL ARINE PPLICATIONS than one ocean, from warmer seas to The torque, speed and power requirements to accom- arctic waters, so motors for marine plish a task are exponentially higher for motors that operate applications must be versatile enough under water. Undersea movement is much slower than in to operate in a variety of conditions. air due to the power required to push through the water
While the greater majority of my ex- (viscous drag). Often, the power limits are not on the mo- perience involves building motors for tor itself, but instead on the power supplies because bat- use in ? n controls on mini submarines, teries have limited capacity, especially at low temperatures. robot arms on deep sea remotely oper- Battery life is a critical concern for ROVs, so it’s common
Halstead ated vehicles (ROVs), deep ocean oil to see performance speci? cations change as the math gets well tools, under ice scanners and scienti? c research sup- done to calculate the power needed to make a speci? c move.
port equipment, the same principles nevertheless apply to Cables can supply power to undersea motors, but power motors for use on any kind of workboat. For Arctic op- loss between the drive electronics and the motor can be erators, there are myriad variables to consider, address and an issue. For example, a 2,500 foot cable is really a 5,000 ultimately monitor. foot cable on a roundtrip. A typical AWG 14 copper wire would present about 12.5 ohms of resistance. At 5 amps, and using ohm’s law, a 63-volt loss in the cable would be realized before it gets to the motor.
Control of the system is another issue. While it’s desir- able to have control topside, feedback delay and noise on the line are reasons to put the drive in proximity to the motor. A reasonable compromise is to place the drive elec- tronics in a dry tank located near the motor; this way only power and high-level communications come down the cable. Fiber optics can be used to solve the noise and speed issue for more reliable communications.
Every marine application must address the effects of cor- rosion. For long-term submersion, the material of choice is 316 stainless steel. It is best if the steel is ‘passivated’ after machine work is done. Passivation maximizes the corro- sion resistance of stainless steel by removing surface iron with an acid solution. While a number of boats use anod- ized aluminum to resist the effects of corrosion, when it comes to mechanical assemblies that are bolted together there are problems with the anodize coatings. To be spe-
A waterproof motor with stainless steel exterior
Credit: Empire Magnetics
October 2016 44
MN
MN Oct16 Layout 32-49.indd 44 9/21/2016 3:27:28 PM