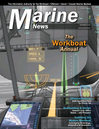
Page 34: of Marine News Magazine (November 2016)
Workboat Annual
Read this page in Pdf, Flash or Html5 edition of November 2016 Marine News Magazine
SAFETY
What to Know When Welding Primer-Coated Steel
Solving one problem can create another. Safety always comes ? rst.
By Kevin Trick, Applications specialist at CWI, Hobart mid competitive bidding, contract deadlines and R TECOMMENDED ECHNIQUES the general drive to gain the best productivity and Porosity is one of the biggest pitfalls when welding primer-
A quality, welding operations in the shipbuilding in- coated steels due to the primer’s zinc content and its inabil- dustry face their own set of challenges. That’s especially ity to burn out of the weld pool when the welding operator true when it comes to welding primer-coated steel, a mate- establishes an arc. Using travel speeds that are too fast can rial prevalent for its ability to withstand atmospheric cor- increase the opportunity for porosity and it can also result rosion from sources such as saltwater. in poor tie-in at the weld of the toes. So what can be done?
Most primer coatings are zinc-based and used on steel One option is to remove the primer coating, but that is that is between 70 to 120 ksi in strength (and sometimes rarely a viable approach from a productivity standpoint; it higher). As a cost- and time-saving measure, shipbuilding causes additional downtime not only for the removal, but operations employ this material to expedite the welding also for painting again after the weld is completed. Still, process — it eliminates the need for painting large por- some companies may prefer this method. tions of steel after the welds are completed. And while the Another option is to tandem weld on a dual-sided joint, coating serves a distinct protective function, it also makes employing two operators welding on opposite sides at the it prone to issues like spatter and porosity during welding. same time or using an automated process with two weld-
From selecting the right type and diameter of ? ller metal ing heads or two individual robots. In both cases, welding to employing proper techniques, it is possible to minimize both sides can help to push the zinc impurities from the the potential for these problems during welding — and to weld. In the case of a semi-automatic operation, it is com- reduce downtime and cost for their associated rework. mon for end users to weld 3 or 4 inches ahead of the other
Ahead of any such business matters, however, comes welding operator to prevent zinc oxide gases from becom- safety. The paint used for this material contains com- ing entrapped in the puddle and solidifying as porosity. pounds that may release hazardous materials into the air Adjusting travel speed and voltage is another means to when heated, including chromium, lead and tin, in ad- minimize issues when welding primer-coated steel. Because dition to the zinc. As a result, the heat from the arc may the primer often makes the weld pool sluggish, traveling too cause paints to give off unsafe amounts of gases like carbon fast when welding can result in poor tie-in at the toes of the monoxide and carbon dioxide. They also give off zinc ox- weld. Welding operators typically need to change their volt- ides, which are formed when zinc vaporizes from the weld age and wire feed speed to accommodate for the coating. A pool. These gases are especially risky in con? ned work ar- lower voltage — about 5 to 7 percent less than when weld- eas or those with poor air movement. Welding operators ing non-coated carbon steel — forms a tighter and/or more should always take proper safety precautions according the biting arc that is capable of burning the zinc out of the weld
SDS (Safety Data Sheets) and Occupational Safety and pool more readily. A slower wire feed speed is often neces-
Health Administration (OSHA) guidelines. sary to compensate for the slower travel speed that accompa- nies this lower voltage. It is also important to note that the slower an operator goes, the more convex the weld bead may be, which may or may not be a factor in a given application.
Finally, the gun angle a welding operator uses in a man- ual operation can also help when welding primer-coated steel. Depending on the travel speed, using a slight angle, between 0 to 15 degrees, can help dig into the weld joint and create a tighter arc to weld through the primer.
S F M
ELECTING A ILLER ETAL
When selecting a ? ller metal for welding primer-coated steel, it is important, ? rst and foremost, to choose one
Credit: Hobart speci? cally formulated to be tolerant of welding through 34
MN
November 2016
MN Nov16 Layout 32-49.indd 34 10/21/2016 2:29:06 PM