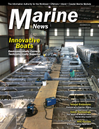
Page 51: of Marine News Magazine (December 2016)
Innovative Boats of 2016
Read this page in Pdf, Flash or Html5 edition of December 2016 Marine News Magazine
Because corrosion by seawater – aqueous corrosion – is an electrochemical process, most metals and alloys are subject to various degrees of destructive corrosion, pitting, erosion or cavitation – except for 316 stainless steel. Automated, state-of-the-art lubrication systems provide grease or oil to many bearing points on board a ship. These systems eliminate the cost and hazards of manually dispensing lubricants, and also ensure longer bearing wear life.
nected lube point at precise intervals. making stainless steel metering valves for many different
Many of today’s most common marine automatic lubri- applications, and keeps a large supply of 316 stainless on cation applications require large series progressive metering hand for fast delivery.
valves. These valves are assembled from inlet, piston, and end sections. Each piston section dispenses an engineered amount of lubricant to the bearing point(s), to which it is connected. These large series progressive metering valves
Richard Hanley is President and founder are generally only available in plated carbon steel, which of Lubrication Scienti? cs, LLC, which will not offer optimum life in high corrosion applications.
produces a full product offering of American
To protect these large carbon steel series progressive made lubrication pumps, metering devices, metering valves from aqueous corrosion, a prominent electronic controls, switches, monitors, and manufacturer of lubrication system components instructs automatic lubrication system accessories, its distributors to encapsulate the valve body in epoxy which are available in both plated steel and material, which is impervious to the corrosive effects of stainless steel construction. www.lubricationscienti? cs.com seawater and salt air.
Unfortunately, these epoxy-encapsulated valves are vir- tually impervious to maintenance as well. When a piston section of the valve ultimately fails, the complete unit is rendered unusable because it is so impossible for shipboard maintenance personnel to disassemble the epoxy encapsu- lated valve assembly, replace the one piston section.
The inability to service sections of epoxy-encapsulated metering valve assemblies is a costly predicament. If it is an eight-section valve, the cost to the customer is ap- proximately $30,000. So, if a section goes bad, the user has to discard one $30,000 valve and replace it with an- other $30,000 valve. If the metering valve assembly were not encapsulated in epoxy, it would be a simple procedure to replace a faulty valve section for a cost of approximately $2,500.00. To avoid the high costs of replacing epoxy-en- capsulated metering valves, Lubrication Scienti