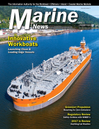
Page 51: of Marine News Magazine (December 2017)
Innovative Products & Boats- 2017
Read this page in Pdf, Flash or Html5 edition of December 2017 Marine News Magazine
Superior Industries who facilitated communication between they attached the head of the conveyor portion along with
Watkins and Superior engineers to address this unique situa- the cylinder system. tion. Watkins described the needs of his application to Supe- Notably, the Telestacker Conveyor’s ? xed radial axle al- rior engineers who started working on new designs. lows operators to move the conveyor over 90 degrees radi-
Superior engineers faced the design obstacle of con? gur- ally, which, combined with the telescopic capability, pro- ing a heavy-duty, telescopic conveyor on a Pontchartrain vides immense ? exibility during operation. barge, which would be between 35 and 45 feet wide. The axle length on a standard 130-foot Superior Telestacker Flexible Operation
Conveyor is over 50 feet. The size constraint required a During the design process, Pontchartrain requested custom approach from Superior engineers. For example, to their Telestacker Conveyor to be ? tted with a custom hop- mount a Telestacker Conveyor onto a 35-foot barge, the per on the tail end to meter material onto the conveyor. length of the axle would need to be about 28 feet. The stan- The hopper has a hydraulically controlled gate that opera- dard stacker design incorporated a steel support structure tors can open or close to change the material ? ow. Before underneath the conveyor called the undercarriage, which owning a barge-mounted conveyor, Pontchartrain used a raised and lowered the conveyor, providing stability for crane mounted clam bucket to unload material from its the axle. The shortened length of Pontchartrain’s custom barges directly to a truck or hopper. Thooft describes the conveyor required sharper angles in the support system de- dif? culty involved with such a maneuver saying, “If you’ve sign, a constraint that demanded a steeper undercarriage. ever looked at a big clam bucket, the control of those is
However, a steeper undercarriage couldn’t work because it pretty dif? cult, especially for the operator that is sitting in wouldn’t allow for any clearance underneath the unit. the crane multiple feet away from where the discharge is.
In order to rectify this problem, Travis Thooft, Superior’s You have this huge load of material that is fairly dif? cult to chief engineer of portables systems, explains that Superior control.” The custom hopper on the barge-mounted con- engineers switched the support system, “from being an un- veyor gives crane operators an easier target to hit. “The dercarriage to what we’ve been calling an ‘overcarriage’ – a distance that the crane operator moves for each load is sig- support system that rides above the conveyor.” Thooft con- ni? cantly less,” says Thooft. In addition to speeding up tinued, “By going to an overcarriage we’re able take advantage the process, Superior’s design provides operators with more of increasing those angles which provides a lower force going ? exibility in positioning the ? ow of material and ensures a through the support system.” Part of the challenge with the consistent ? ow rate. new design was ? guring out how to distribute the weight “It’s a very versatile machine, allowing us to unload to within the unit. Pontchartrain’s conveyor weighed the same stockpiles and hoppers or onto trucks,” says Watkins. He as a standard unit, but the axle weight was increased consid- mentions that one of the best features of the Telestacker erably in order to compensate for the adjustments made to Conveyor is the wireless remote control operation, which the angles and distances of the support carriage. allows the controller to run the operation from a safe posi- “It was a ? t for Superior where engineering through tion while always maintaining a clear visual of the opera- problems seemed to be their mission in life,” says Watkins. tion. “It’s a very safe machine, very steady,” he says. “Reducing the footprint of a Telestacker Conveyor to ? t Watkins vision for a fully engineered, quality barge- onto a barge deck while maintaining the conveyor reach is mounted stacker provided the catalyst for Superior engi- not easy,” he adds. neers to pursue greater innovation and a better product for
After the new design proved viable operating in-appli- material transfer companies. Custom conveying solutions cation, Pontchartrain Materials felt that the custom ma- provide an alternative to slow, stationary operations and chine was worth the investment. They purchased the unit equip river businesses with ? exibility, ef? ciency, and speed. in August of 2015. To mount the conveyor onto one of the unloader barges, Pontchartrain’s crew set the conveyor axle on the barge platform and assembled it onto the bearing along with the conveyor tail. They then put up side sup-
Daniel Tiernan is a Communications ports and pinned the actual conveyor portion, including
Specialist at Superior Industries.
the main and stinger, onto the tail. Simultaneously, the in- stallation crew pinned the overcarriage to the tail. Finally, 51 www.marinelink.com MN