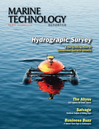
Fugro Upgrades DeepWorks
Fugro Subsea Services enhanced tooling capabilities on its DeepWorks simulators. Improvements have been made to ROV manipulator deployed tools to provide easier access verification as well as more realistic deployment behaviors.
In addition to the traditional approach using a Schilling T4 master arm, a new method has been introduced in DeepWorks Engineer to enable engineers who do not have specific ROV piloting skills or access to a master arm controller to precisely control manipulator tools. The tool tip is driven manually from a suitable input device such as a space navigator/3D mouse or automatically from a predefined set of instructions in a file. Manipulator joint positions follow the tool and are adjusted automatically. This engineering solution supports full collision detection and with user-configurable receptacle tolerances can be used for position feedback and to verify successful tool deployment.
Similar improvements have also been made on the DeepWorks ROV pilot simulator using powered tooling components. Using the master arm controller, pilots can lift tools out of a holster and deploy them into receptacles with realistic collision and dynamic response. Tolerances of receptacles can be changed to cater for the skill level and experience of trainees. Torque tool can turn a valve to its open or closed position and this can activate linear actuators or hydraulic rams.
These enhanced tooling capabilities are available with new orders for DeepWorks and as an upgrade to existing installations.
www.fugro.com
(As published in the May 2013 edition of Marine Technologies - www.seadiscovery.com)
Read Fugro Upgrades DeepWorks in Pdf, Flash or Html5 edition of May 2013 Marine Technology
Other stories from May 2013 issue
Content
- What Goes Down ... page: 14
- MHI to Build for PGS page: 18
- Exploring the Abyss page: 20
- Unmanned Surface Vessels page: 24
- Unmanned Surface Vessels: Wave Glider SV3 page: 32
- Unmanned Surface Vessels: C-Stat Mobile Buoy USV System page: 34
- Ocean Business Sold page: 36
- Partrac, Rockland Scientific Announce Partnership page: 36
- Ashtead Increases Sonardyne 6G Rental Pool page: 36
- Seatronics Invests in Teledyne TSS Products page: 37
- Geomatrix Buys Applied Acoustics’ Energy Source page: 37
- New Gyro Changeover System page: 38
- Sonardyne Aids NOC page: 38
- EvoLogics Showcase Latest Developments page: 39
- Forum Subsea Rentals Adds iXBlue Systems page: 40
- DP-PHINS Adds to Acoustics page: 40
- Kongsberg to Offer AUV Rentals page: 41
- Fugro Upgrades DeepWorks page: 41
- Teledyne Moves Portfolio to Odom page: 42
- Ashtead Technology Launches Electric Dredge page: 42
- Navigation, Tide and Weather Information via Twitter page: 43