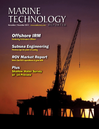
Brazil Offshore: Petrobras & Subsea Engineering
Brazil’s Petrobras has been one of the leading players in deepwater, subsea development projects since the turn of the century. These projects include pre-salt and post-salt plays, which require extensive and complex subsea engineering and construction efforts. It would be impossible for Petrobras to develop all of its projects alone, therefore much is done by specialized companies, mostly of foreign origin. “We could not have advanced in this project (pre-salt) conventionally, developing the production individually. We needed a global vision of the projects, starting from a high level plan,” said José Formigli, Petrobras’ Executive Director of E&P, speaking of the primary plan for the development of the pre-salt at the Santos Basin, the Plansal, which was created in 2008. According to Formigli, “The Plansal led to a ‘virtuous cycle,’ which has guaranteed better results each year.”
In the last 10 years Petrobras investment in R&D grew 22.7% per year, reaching $1.1 billion in 2012. Petrobras rarely operates alone when it comes to subsea engineering and construction. Partnerships are part of Petrobras’ DNA and by working in cooperation with institutions such as the ANP (National Petroleum Regulator), universities such as the Federal University of Rio de Janeiro (UFRJ) and service companies like FMC Technologies, Subsea 7 and DeepOcean, Petrobras has found solutions to many problems and challenges in subsea development that might have taken much longer to realize if the company were to go at it alone.
Some of the problems and challenges are directly related to the harsh environment where the constructions are undertaken, specific challenges are strong deepwater currents, irregular and unstable seafloor, along with equipment corrosion and equipment failure during and after installation, to name just a few. “It is important to have access to reserves, technology and the adequate mechanisms to manage production to be competitive,” said José Miranda Formigli, Petrobras’ E&P Director during the recent Offshore Technology Conference (OTC Brazil 2013) in Rio de Janeiro.
“In terms of wells and subsea, we have problems associated with hydrate formation and, in some cases, we have also to make work-over on the wells for sand control, and I would say traditional workover for replacing gas lift valves. So this is a very traditional work-over that we have to do in all fields with the mature areas that we have in Campos Basin. Beside that, in some areas we have also some electrical submersible pump replacement work to be done. For example, this affected P-57 production,” said Formigli.
Teaming with FMC Technologies
In terms of subsea engineering FMC Technologies is at the forefront with important projects in Brazil, such as the subsea separation system at the deepwater Marlim field at the Campos Basin, which is one of the major global subsea separation projects in existence. “Subsea oil/water separation, as-delivered in Marlim is the first step in removing enough water to prevent flow assurance issues,” said Rob Perry, Director of global subsea processing systems for FMC Technologies.
Marlim is Petrobras’ largest field in the Campos Basin, located 110 km (70 miles) offshore Rio de Janeiro. It was once considered the world’s largest subsea development, with 129 wells and 8 floating production units (FPU), devoted to the extraction of oil and gas. The Marlim field is spread out between depths of 640 to 2,590m (2,100 to 8,500 ft.), with the separation system itself located at the 900m mark (2,950 ft). This is the first system worldwide to include deepwater subsea separation of heavy oil and water, with sand removal systems and reinjection of water to boost production in this mature field. The separation system also includes cyclone modules that will perform water treatment before re-injecting the water back into the reservoir. The separated gas is added back to the oil stream to aid its lifting to the FPU, while the separated water is pumped back into the reservoir to further increase production. FMC supplied the subsea separation and pumping system, utilizing a novel pipe separator design, licensed and developed in cooperation with Statoil. The system is being engineered by FMC’s operations in Brazil, Norway and the Netherlands with final manufacturing and integration activities performed at the company’s Rio de Janeiro facility. For this project FMC is responsible for the offshore commissioning and for technically assisting in the installation. “Marlim is the fifth field in the world that will utilize FMC’s subsea separation technologies,” said Tore Halvorsen,. “The project will enable a broader application of our separation technologies for future subsea processing opportunities.”
Subsea 7
Subsea 7 is another major Petrobras partner in subsea engineering and construction projects. Only this years Subsea 7 has been awarded a $350m, five-year contract for a pipe-laying vessel. The contract covers the operation of Kommandor 3000, a 118 m PLSV with a top tension capacity of 15 tons, two work class ROVs, two 30 ton cranes and three carousels for flexible pipes. The PLSV is capable of installing flexible lines, umbilicals and equipment to a depth of 2,000m and will start work under the contract this year. Victor Bomfim, Subsea 7’s Senior Vice President for Brazil, said “Subsea 7 has one of the most advanced vessel fleets in the world for subsea engineering and construction, and we look forward to supporting Petrobras in future developments.” Another important Subsea 7 project is the seabed-to-surface Guará-Lula NE project. Guará and Lula are part of the large pre-salt discoveries made by Petrobras in the Santos Basin, Brazil in ultradeep water depths of beyond 2,100m, 300km from shore. The Guará-Lula NE project is a US$ 1billion contract awarded to Subsea 7 in 2011 by Petrobras and to date is the largest EPIC-SURF contract awarded in Brazil. The project scope includes the subsea engineering and the subsea installation of four decoupled riser systems featuring large submerged buoys supporting 27 steel catenary risers. The engineering and project management work is ongoing at Subsea 7’s offices in Rio de Janeiro. The SCRs are being reel-laid by the Seven Oceans vessel and hooked-up to the subsea buoys. The production and water injection lines are constructed predominantly from Mechanical Lined Pipe (BUTTING BuBi). This is a result of a joint development programme by Subsea 7 and BUTTING, with Petrobras participation. Offshore installation commenced during the second half of 2012, using Seven Oceans, Acergy Polaris and Skandi Seven.
The system includes:
• 4 submerged buoys each weighing about 2,000 tonnes to be installed approximately 250 meters deep, buoy foundations and associated tethers
• 27 steel catenary risers of 3.9km
• 21 x associated pipeline end terminations (PLETs) of which 18
• 7.5-inch production lines, three 9.5-inch water injection lines and six 8-inch gas injection lines
• 27 x anchor suction piles
• 4 x monitoring systems for buoys and SCRs
On October 21 Subsea 7 was awarded two new contracts with a combined value in excess of $600 million from Petrobras, for operation of the PLSVs Seven Mar and Seven Condor on a day rate basis for approximately three years, with operations starting toward the end of 2013 for Seven Mar and in the third quarter of 2014 for Seven Condor. Both vessels have operated for Petrobras for several years and are currently under contract with the national operator. The work scope of the contract is similar to that of other PLSVs which Subsea 7 currently operates offshore Brazil, comprising project management, engineering and installation of flowlines, umbilicals and equipment supplied by Petrobras. “Following on from the renewal of contracts for the K3000, Seven Phoenix and Normand Seven, the renewal of contracts for Seven Mar and Seven Condor further strengthens our presence in the day-rate PLSV business segment in Brazil,” said Victor Bomfim, Senior Vice President for Brazil.
Over the years Petrobras has installed an expressive amount of subsea equipment and underwater pipelines up to 3000m deep. In many cases it is impossible to inspect them with intrusive techniques, and the need of advanced underwater in-service inspection tools and self-monitored equipment has become imperative. The CENPES, Petrobras’ Research Center is focused on advancing inspection and monitoring technologies to face these challenges, leading a project which main goal is provide reliable and practical solutions applied to SURF components inspection (subsea structures, Xmas trees, umbilicals, control systems and subsea piping). Many tools are being developed locally and show how much subsea engineering has developed in Brazil in the last 10 years. CENPES is also working on developing new and more efficient systems, methods and procedures for deepwater subsea construction, with a eye at increasing subsea construction efficiency for the many deepwater pre-salt development set to take off in the coming years, including the recently auctioned Libra pre-salt field, which is expected to require something to the tune of 60 to 90 support vessel, many of which will be exclusively used for subsea construction efforts. “Development of subsea systems and equipment, new or optimized, are vital to produce in deep and ultra-deep waters, pursuant to concepts of compact subsea oil, water and gas separation, re-injection of produced water into the seabed, gas-lift technology enhancement, subsea gas compression, oil boosting from the seabed, and a new generation of submersible electric pumps,” said Marcos Isaac Assayag, Director of the CENPES Research Center.
Petrobras is looking to improve its the pre-salt production systems and reserve recovery factor by intensive use of compact subsea solutions, injection systems, and by improving the capacity of new pre-salt FPSO units. In order to do this Petrobras and partners are constantly working on the development of subsea systems and equipment, new or optimized, to produce in deep and ultra-deep waters, experimenting concepts of compact subsea oil, water and gas separation, reinjection of produced water into the seabed, gas-lift technology enhancement, subsea gas compression, oil boosting from the seabed and a new generation of submersible electric pumps. “One of the new technologies related to subsea engineering comprises the new flexible riser top connector for use in deep and ultra-deep waters features an innovative design that allows the pipe to be anchored onto the connector without traction reinforcement bending. This improves traction reinforcement structural performance, enabling greater fatigue resistance of the risers’ system. The connector concept was developed and patented by Petrobras and engineered by the Federal University of Rio Grande do Sul(UFRGS). A prototype was assembled on a flexible line sample and passed the initial tests. Fatigue performance tests are currently in progress at UFRGS. Once the technology has been confirmed by the qualification tests, Petrobras may license the connector to the traditional suppliers in the area,” said Assayag.
The Steel Lazy Wave Riser
Another interesting Petrobras development in subsea engineering is the Steel Lazy Wave Riser (SLWR) setup, which has optimized the cost of the Sapinhoá Norte riser collection system. The technology enables the use of steel risers connected directly to an FPSO. This riser system includes the use of floats in mid-water so as to afford a geometry that will provide the steel tube resistance to fatigue during the life of the project. Petrobras undertook extensive optimization studies on the system’s structural configuration for the Santos Basin scenario, which enabled the choice of the SLWR for Sapinhoá Norte. The study allowed for the minimization of pipes with metallurgical clad in the production risers; that could be substituted in 70% of the length of the risers, for mechanical clad ones, which are less expensive and more readily available on the market. This will be the first SLWR connected to an FPSO anchored by spread mooring system, and the first in the Santos Basin pre-salt region. This will be the fourth system in the world to use the SLWR, after the Bonga Field, in Nigeria, the Parque das Conchas (BC-10), in the Espírito Santo Basin, and the Stones Field, in the Gulf of Mexico (still under development). However, Petrobras is reportedly having a frustrating time installing these riser-buoys, which are considered to be key equipment to increase production at the Sapinhoá and Lula Northeast plays. The project includes four submerged riser buoys, each weighing around 2,000 tons, hooked up in pairs to two FPSOs. “We have faced serious problems in the installation of the first of these two systems and this has caused long delays. The reason for this includes susceptibility that the installation vessel (Seven Polaris) has shown to maritime conditions,” said Formigli.
He also explained that the first buoy is still held by temporary tethers but installation is expected to move forward in November, as maritime conditions in the South Atlantic become more agreeable with the onset of summer. The first pair of riser buoys are expected to start producing by the end of January, several months after the original deadline.
(As published in the November/December 2013 edition of Marine Technology Reporter - www.seadiscovery.com)
Read Brazil Offshore: Petrobras & Subsea Engineering in Pdf, Flash or Html5 edition of November 2013 Marine Technology
Other stories from November 2013 issue
Content
- Help Build the "Space Station of the Sea" page: 10
- Makai Continues Energy Research in Hawaii page: 12
- Fugro’s Offshore Wind Farm Drill Ready page: 14
- Dr. Jennifer Brower, Prometheus page: 18
- Bourbon: Offshore Seismic Survey Vessel Success page: 22
- The Rise of the Work-class ROV Market page: 30
- Brazil Offshore: Petrobras & Subsea Engineering page: 34
- Offshore Energy: Monitoring Performance page: 42
- Sea Owl ROV Revamped page: 56
- New SediMeter Features Integral Cleaner page: 56
- MacArtney Updates MERMAC ROV Winches page: 56
- Project Launched to Better Detect Ocean Ice Hazards page: 56
- New AQUAlogger Aids Ocean Data Recording page: 57
- Triton Subs in Fort Lauderdale page: 57
- LVDT Linear Position Sensors Survive Operation Underwater page: 57
- Vectron Measures Tide Speeds page: 58
- Kraken Debuts AquaPix MINSAS page: 58
- Updated SeaLite Sphere LED Light page: 58
- OSIL Launches Fracking Water Monitor page: 59
- Stand-Alone Mosaicking Module Introduced page: 59
- OSIL Giant Snow Catchers Used for NERC Research page: 59
- Immersion Suit Drying System Ordered page: 59