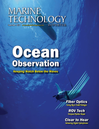
Wave Glider – Ocean Monitoring in Motion
The Wave Glider is a remote control ocean robot, which uses wave motion as propulsion. As an autonomous marine vehicle, the Wave Glider is capable of conducting detailed meteorological and oceanographic surveys across large distances and under the most extreme wind and sea conditions. Since its inception, the Wave Glider has seen the roles it is capable of undertaking greatly expanded, with the Wave Glider becoming a key Metocean measurement asset for research institutes, academia, shipping companies, government agencies and oil companies. Marine Technology Reporter’s Contributing Editor Claudio Paschoa spoke with Sudhir Pai, Vice President, Technology and Operations of Liquid Robotics Oil and Gas (LROG), a joint venture with Schlumberger, about the qualities and capabilities of the Wave Glider.
The Wave Gliders are in a distinctly different class of AUVs from previous gliders in that they are wave-propelled with continuous diurnal solar panel support of electrical systems. A sensor platform like the Wave Glider is capable of detecting solid data at depths where satellites data is unreliable. Sudhir explains the vision behind the design of the Wave Glider and how its development process occurred, “The Wave Glider development began out of a man’s passion for whale songs. Joe Rizzi, Chairman, Jupiter Research Foundation, had a love for the sounds of whales as they migrated along the coasts of Hawai’i to Alaska. In order to capture their songs live, he enlisted Roger Hine, a mechanical engineer and robotics expert, to help develop an unmoored, station-keeping data buoy. A joint venture then began between Joe and Roger Hine. The initial prototyping and early testing was from approximately 2003 - 2008. Development of the first commercially available system followed in 2009 with extensive sea trials and broad market sales in 2010,” said Sudhir Pai.
This surfboard-shaped vehicle, contains photovoltaic panels that continually replenish the lithium-ion batteries used to power its navigation, communication systems, computing and sensor payloads. Wave Gliders may also carry submerged sensor payloads underneath their wave-powered wings and rudder assembly, which are connected to the glider body by an umbilical. The low-profile surface float, high-strength umbilical and sturdy sub allow the vehicle to carry on through high winds and waves of the open ocean. The sub is sheltered from surface weather conditions and acts as a drift anchor to counter the effects of wind and wave on the surface float. During storms, it cuts through a wave and in stern seas it can surf waves too. This unique mode of propulsion allows tremendous range and duration of sampling at the air-surface-underwater interface as it uses wave energy for thrust and solar energy to power its rudder motor, navigation system and payload electronics.
The System
The Wave Glider system consists of a surface float and a submerged glider, connected by an electromechanical umbilical. The float weighs about 68 kg (150 lb.) with a standard payload and measures 208 X 60 cm (82 X 24 in). Its deck supports antennae for GPS, satellite communications and collision avoidance systems, as well as a mast to support a position marker light and flag for increased visibility. Seven smart battery packs housed within the float are each electrically isolated with separate discharging and monitoring circuitry that permits only two batteries to be in use at a time. Two payload bays support a total of 18 kg (40 lb.) of sensors and equipment. The umbilical, about 5.8 m (19 ft.) long, provides a robust, yet flexible connection between the surface float and submerged glider and transmits power and steering commands to the glider. The submerged glider, or sub, is 2 m (6.5 ft.) long. The sub glides on six pairs of underwater wings that propel the entire Wave Glider system forward. The sub frame supports a rudder and its control package. The sub frame weighs about 68kg. The combination of a very low-profile surface float, high-strength command umbilical and the weight of the sub allow the vehicle to carry on through huge waves and fierce wind.
“Initial funding for the Wave Glider development was created by Joe Rizzi and private investors. Subsequently, funding was provided by lead investors; Vantage Point Capital Partners (VPCP), Riverwood Capital and Schlumberger. The Wave Glider SV Series is comprised of the Wave Glider SV2 and Wave Glider SV3. They are positioned akin to the BMW Series of cars – different performance characteristics and features at different price points. The Wave Glider SV3 is a larger platform with modular power and payload capacity; it has an auxiliary thruster to navigate through extreme ocean conditions (doldrums to high currents). In addition, the Wave Glider SV3 has an advanced operating environment with autonomy, automatic ship identification, avoidance features and enhancements for data delivery and communications,” said Sudhir. To date, Liquid Robotics Oil and Gas, a JV between Schlumberger and Liquid Robotics Inc, has 44 of the Wave Glider SV2 platform and 25 of the Wave Glider SV3 platform. Later this year they plan to acquire an additional 25 Wave Glider SV3 platform to have a total fleet of 94 Wave Gliders conducting various missions around the globe. “The Wave Gliders are used around the world for climate change, ocean acidification, environmental monitoring, fish tracking, tsunami prediction and severe weather observation and monitoring. Oceanographic institutions such as Woods Hole Oceanographic Institute, Scripps Institution of Oceanology, Monterey Bay Aquarium Research Institution, along with international environmental research organizations such as the National Oceanographic Institute in the UK are all using Wave Gliders for long duration ocean observation,” said Sudhir Pai. Wave Gliders are manufactured and assembled in California. The float is made from advanced composite materials and the glider (submarine) section is made from stainless steel with some parts made from titanium. All sensors are acquired from industry recognized, top of the range companies. The Acoustic Doppler Current Profiler (ADCP) is made by Teledyne-RDI; the weather station is made by Airmar; wave height sensor form Data Well; Acoustic Modems from Sonardyne; MAG sensors from Marine Magnetics. Hydrocarbon fluorometers are made by Turner Inc. and Chelsea Instruments.
To Boldly Go …
In December 2012, a Wave Glider completed a 10,357 mile (16,668 km) scientific expedition across the Pacific Ocean, not only did it set a new world record for the longest distance traveled by an autonomous vehicle, the wave-powered glider reached Australia’s Hervey Bay with wealth of data, including observations of rogue waves that satellites failed to detect. “The Wave Glider is a true game changing technology, key aspects of this technology is that there are no humans and no fuel on board, so it is able to execute operations in an environmentally friendly and safe manner while minimizing damage to assets and people. No other autonomous ocean robot provides the ability to stay out at sea for 1+ years, collect data, compute in-situ and transmit valuable real-time data back to shore. By removing the risk and cost barriers to long duration ocean observation, scientists can now study ocean basin scale phenomena from the surface of the ocean gathering high-resolution temporal and spatial data in densities never before possible. An example of this is in severe weather forecasting. Today we can accurately measure the path of a cyclone/hurricane/typhoon but not the intensity (tropical storm or Cat 5). Collecting valuable data from the surface of the ocean during the live event has not been possible until the invention of the Wave Glider. Just last week, a Wave Glider in the South China Sea navigated through Typhoon Rammasun, one of Asia’s biggest typhoons in the last 40 years. It continuously collected and transmitted data to satellite directly through the eye of the typhoon (150 mph winds, 45 ft. waves). This has the potential to provide meteorologists the data needed to improve forecast models to save human lives as well as billions in property damage,” explained Sudhir Pai. The Wave Glider was remotely piloted through Super Typhoon Rammasun (Category 5) collecting and transmitting vital and rare, real time wave, temperature, conductivity and current data all from the surface of the ocean, while simultaneously collecting current data to 100 meters and full directional wave spectrum data, this collection of data gave scientists a unique picture of the extreme surface and underwater conditions encountered. For the first time ever a marine vehicle transited and survived a major typhoon class storm to collect surface and underwater data without severe risk to human life and property, at a fraction of the cost to boot.
“To date no LROG Wave Gliders have been lost at sea and we have had two incidents involving other ships and one may have been bitten by a shark. A key parameter recorded is days at sea. The 17 Liquid Robotics Oil & Gas missions have clocked 1250 days at sea. Overall, the fleets of Wave Gliders have collectively traveled over 450,000 nautical miles (almost a round trip to the moon),” says Sudhir Pai. Liquid Robotics Oil and Gas owned Wave Gliders have been active in working with operators around the world. “They have been used all over the world. Specifically, Western Australia, North Sea, Nigeria, Equatorial Guinea, Uruguay, Gulf of Mexico, Alaska and arctic regions are a few areas of operations for Liquid Robotics Oil & Gas. We are just getting ready to deploy systems in Brazil for the first time.”
Schlumberger was quick to see the potential behind the Wave Glider system as a data acquisition system for offshore operations support. “Schlumberger is the world’s largest oilfield services company with its key strength being secure data acquisition and management. The Wave Glider is an excellent platform in a marine environment, with integrated sensors to harvest this data as the vehicle traverses the oceans,” said Sudhir Pai. Fleets of Wave Gliders can be used for environmental monitoring of large offshore areas, such as the long Brazilian coast or in Australia, which also has a large coast and this could be interesting from a financial and logistical standpoint. “The first mission done by LROG was for Chevron (CVX) off the coast of Onslow (Western Australia) to monitor particle suspension in water (Turbidity) during the Wheatstone Pipeline dredging operation. Wave Gliders will be deployed later this year around the Brazilian currents off the Campos Basin. Four more missions are currently going on concurrently in four different parts of the world. One important application for the Wave Glider is environmental monitoring from both a security and protection aspect and for early alert and notification of environmental disasters. Fleets of systems can be deployed in advance to monitor MPAs, EEZs and critical coastal areas,” said Sudhir Pai.
The more powerful Wave Glider SV3 has an auxiliary vectored thruster, the function of which is to provide additional thrust capability in extreme ocean conditions (doldrums to high currents). It also provides thrust for quick mobility if needed for obstacle avoidance. The thruster is solar powered and runs off of the lithium batteries and when needed, a remote command is given to initiate the thruster. All sensors on the Wave Glider are acquired from industry leading sensor manufacturers.
Wave Glider is a very robust and reliable vehicle and its maintenance is conducted as Service Levels (SL). SL-1 is done after every recovery; SL-2 every six months and SL-3 every year. SL-2 involves a re-paint of the surface with anti-fouling paint and SL-3 involves a full quality check and extensive system upgrades. In future we may see Wave Gliders continuously monitoring Metocean data in petroleum basins, both for support of seismic operations and for E&P support. Sudhir Pai pointed out that, “LROG has conducted 17 missions so far, over half of those missions were to support seismic operations particularly during close pass of obstructions like rigs, platforms and FPSO. The Wave Glider equipped with METOC services provides real time intelligence to the navigation team on board to safely image as much of the area as possible. The Wave Glider is also useful in detecting oil seeps and the current generation of SEEP sensors (called GEN-2) can detect (Yes/No) presence or absence of hydrocarbon. Four Gen-2 Wave Gliders were used on a project to identify and sample seven separate natural hydrocarbon seepage areas in the Gulf of Mexico. The next generation SEEP technology (Gen-3) will be able to characterize the hydrocarbon.” The future of the Wave Glider and its many possible uses by different industries and institutions are exciting to think about and future Wave Glider upgrades will be geared towards expanding and enhancing these capabilities. “The future is exciting and full of promise. Seismic service has undergone early tests and trials, which look very encouraging. The results were presented at the recently concluded EAGE-2014 in Amsterdam. This will help complement the streamer technology and help image areas that traditionally the vessels either cannot go due to depth or terrain or the service is cost prohibitive like the Permanent Reservoir Monitoring. Our overall objective is to provide our clients with technology, data and service of a very high quality so they can overcome their challenges in a safe and cost-effective manner” concluded Sudhir Pai.
The Wave Glider has
7 main business lines
METOC: Meteorology and oceanography, ability to monitor the physical properties of the ocean.
SEEP: Hydrocarbon detection; background or oil spill
GATEWAY: Ability to communicate with subsea and sea bottom sensors via acoustic communications.
MAG: Computing Total magnetic Intensity (TMI) in a marine environment where EMO (Earth magnetic Observatories) are not available.
PAM: Passive Acoustic Monitoring
Seismic: Acquisition complementing streamer technology
Others: Long distance communication, security and turbidity measurements. This opens the door to many others marine data acquisition services.
(As published in the September 2014 edition of Marine Technology Reporter - http://www.marinetechnologynews.com/Magazine)
Read Wave Glider – Ocean Monitoring in Motion in Pdf, Flash or Html5 edition of September 2014 Marine Technology
Other stories from September 2014 issue
Content
- ULSTEIN PX121 for Otto Offshore page: 10
- Triton Submarines’ New Submersible page: 12
- OceanScience Adds Autonomy page: 14
- Island Performer for Deep-Sea Subsea Work page: 16
- Rogue Waves page: 18
- The Blue Economy page: 20
- Innovative Solutions Mark SWE’s Heritage page: 24
- Multi-channel Fiber Optic System Design: Going Big in Small Packages page: 28
- Wave Glider – Ocean Monitoring in Motion page: 36
- Underwater Noise Understood: Clear to Hear page: 46
- Wachs Subsea Answers the Call for Chevron page: 52
- Biofouling Foiled: UV Light Harnessed for Biofouling Control page: 58
- New Subsea Hi-Traq Trencher page: 74
- Kongsberg Upgrades Digital Stills Camera page: 75
- Thien Nam Buys Sonardyne’s Ranger 2 page: 75
- MTR 100: ASV page: 91