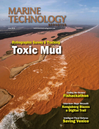
Page 28: of Marine Technology Magazine (June 2016)
Hydrographic Survey
Read this page in Pdf, Flash or Html5 edition of June 2016 Marine Technology Magazine
GPS, Gyro Compasses & MEMS detected by the survey vessel used by CADS Survey were in the total station traverse.” post-processed and the results were reported back before the Caissons were placed 260 feet apart. At approximately every screed frame’s positioning was signed off. 1,600 feet survey pillars were installed on a caisson. Further
The survey vessel also helped verify that gravel bed extents static GNSS baselines were observed to each one.
and elevations were satisfactory after the survey.
For accurate caisson placement, the upper beam of each cais- How to Meet in the Middle?
son was mounted with three or four GNSS receivers, which To ensure both ends of the jetty met in the middle, CADS wirelessly transmitted position data to the hydrographic sur- Survey employed long-range reciprocal trigonometric height- veying software. In the control room on the caisson ? oating ening using geospatial total stations and interference-averse barge, an operator viewed the position and tilt of the caisson measuring technology. These instruments can detect targets in relation to the design location. A team that included engi- without interference from surrounding prisms to 8,200 feet, neers to determine how much water to pump into the caisson achieving one-centimeter level accuracy.
to keep it level, a hydrographic surveyor and a winch operator The team set up the total stations to face each other from watched the visualization on three large screens. The hydro- neighboring caissons and observed from both ends of the line. graphic software displayed winch lines to help the operator They measured at exactly the same time to derive mean el- determine which one to use to move the caisson, plus informa- evation differences while minimizing the effects of refractive tion such as vertical-distance-to-touchdown and caisson cen- turbulence. CADS Survey was able to do this due to the re- ter location. The latter screen was used when the caisson was liability of the total stations and will be able to repeat their close to design location. results even for the longest observations.
Static GNSS Enhances Total Station Traverse Solving Access Problems with 3D Scanning
To solve the problem of poor network geometry for total sta- When pipe modules were installed, they came with straight tion observations, CADS Survey observed primary control lengths of pipes already installed. CADS Survey’s next task points with static GNSS—these tied back to the high-order was to deliver accurate pipe end measurements. After careful network on Barrow Island. The baselines were observed for testing, CADS Survey deployed 3D scanners to aid in data col- 12 hours or more to negate any subtle movements caused by lection. Rope access climbers, with the sea beneath them, bolt- environmental factors. ed the scanners in place close to pipe racks. The survey team “Caissons sway, so you can wander off with your traverses,” positioned themselves nearby with the scanning PC – used to
Bush said. “The static GNSS tied everything back to the Bar- operate 3D software – and were able to provide a clean rep- row island network. It was an insurance against angular drift resentation of pipe ends that they could model with certainty.
June 2016 28 MTR
MTR #5 (18-33).indd 28 6/1/2016 5:21:34 PM