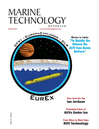
Designing for Ice with Ian Jordaan
By Andrew Safer
Dr. Ian Jordaan, Professor Emeritus and University Research Professor in the Faculty of Engineering and Applied Science at Memorial University, and President of Ian Jordaan Associates, Inc.
How did a South African engineering student end up in Newfoundland?
I immigrated during the time that Mandela was imprisoned on Robben Island. I was strongly pro-Mandela. I went to England first, where I did doctoral studies, and then I immigrated to Canada and obtained a position at the University of Calgary. Then I entered consulting work with Det Norske Veritas in Calgary. They had formed a Cold Climate Technology Center.
I became head of research and development for them and later became vice president in Canada for R&D. In the early 1980s when I was at DNV, Calgary was the chief place for the Arctic because access was generally from Calgary north. Quite a few oil companies were there. It was a logical place for DNV to do cold climate technology. The idea was to tap into Canadian expertise. In 1986, I was fortunate to obtain a position at Memorial University (in St. John’s, Newfoundland) as a research chair, sponsored by Mobil. The focus was to investigate ice-structure interaction, which I had been very interested in when I was working for DNV. This gave me a chance to do research in more depth.
The position here at Memorial was the NSERC Mobil Industrial Research Chair in Ocean Engineering. It was the first Collaborative Industrial Research Chair established at Memorial, and among the first in Canada. Fairly soon after coming here in 1986 I started working on several projects with C-CORE. I’ve worked on and off with them ever since, usually on a project basis. I have worked on various aspects of Hibernia, Terra Nova, White Rose, Hebron and other projects offshore Newfoundland and Labrador. I’ve also worked on projects in the Beaufort Sea, Barents Sea and Caspian Sea.
What are the biggest challenges in providing engineering solutions for industries that are operating in ice-prone waters?
The biggest challenges are to get a handle on (1) how to set design criteria, and (2) how to understand ice loads. (1) For design criteria, the focus is very strongly on using risk-based methods, probabilistic methods. One could very easily over- or underestimate what a safe design is. There is a reasonable point where the structure is safe enough; it’s not unsafe, and it’s not overdesigned. If you design for the biggest feature ever seen, like the 13-kilometer ice island seen off St. John’s in the 1880s, you’d be designing for something that is quite unrealistic. So, the idea is not to overdesign. We decided to use a risk-based method: to minimize risk to human life and the environment without necessarily having to design for the worst feature ever seen. We set risk criteria that follow civilized norms, and worked out what the corresponding ice feature would be.
(2) Regarding loads, I’ve spent a lot of time on the mechanics of ice interacting with structures. For example, with a circular structure, many features may hit on the side in glancing blows. You consider the shape of the ice feature, say, an iceberg, and the speed it’s travelling. To arrive at the number of ice features per unit area, looking at data from the International Ice Patrol is a good start for the Grand Banks. All of the data figures into the calculation. Now you’ve got the risk down to a very acceptable level. You didn’t go for excessive overdesign. I believe that this approach helped a lot with making things happen here. Having this industry here, from my point of view, has been a healthy development for Newfoundland and Labrador.
The other part (of ice-structure interaction) is how ice fails. It’s very tricky and quite complicated. When I held the Chair here, we had some field programs using a medium-scale indentor. Mobil had used this device to measure forces in a tunnel inside an iceberg. We installed it inside a trench to push against the ice feature from either side and measure the forces and pressures. Mobil Oil Canada Properties donated the indentor and associated equipment to Memorial. With the help of Sandwell (now Ausenco), one of our experiments was to fill up compressors with compressed air, release it all in just a few seconds, and measure the impact forces and pressure distribution. This was done on an ice island in the Arctic that had been used for a variety of experiments including seismic readings. We dug a trench in the ice and used the indentor to measure the forces and pressures. When the indentor pushed against the ice, we saw finely pulverized crushed ice coming out. Pushing into it, applying pressure and shear was producing microstructural changes resulting in tiny grains of ice. Parenthetically, when continents push together, the same thing happens in mylonites (rocks), which have broken down into finer grains.
Ice is one of the few materials that exhibits pressure melting. When there is enough pressure on it, it starts to melt, and the melting point decreases under pressure. That’s unusual. Pressure softens the ice, and when it’s ejected, it comes out as a finely grained powder. Pressure melting is related to the fact that ice expands on freezing.
There are also significant challenges because we’re working with ice mechanics. This table here has nice, defined geometry. It’s level; you can put a load on it and work out the stresses, and compare it to failing stress. You don’t necessarily have to worry about the details of how it cracks up. If you have an ice feature, there’s irregular geometry, and the feature is not going to stop when our mechanics assumption suits us. There’s crushing, recrystallization, and other things that are very much at the leading edge of what we can do. We’re going into an area where there are great difficulties in treating the mechanics.
The fracture problem is the worst part. It’s very random. Floes can split; features can break in half, bits can peel off; there can be local fractures associated with high-pressure zones; there can be large fractures. Fracture happens where there is a flaw in the ice. Grain boundaries are a significant source of crack propagation. Large features can break off in ice; icebergs calve. It’s very hard to estimate what is going to happen.
The mechanics are complicated partly because ice has a high homologous temperature (close to the melting point), so it’s prone to change its structure. The recrystallization is quite dramatic. Locally, it can be 1 million times softer than the ice next door. Classical mechanics does not work except in some domains. When you have break up, you get crushed ice and high-pressure zones; you can’t use plasticity or elasticity. Also, ice changes with time. If stressed, it will change its structure and its response. You can’t treat it as a time-constant substance.
Why is it important for designers to know about the mechanics of high-pressure zones in ice-structure interactions?
When it comes to high-pressure zones, the Titanic is a case in point. One view, mistaken in my opinion, was that the riveters were at fault. If we have a vessel that is not ice-class, we don’t go into areas where there are icebergs and expect the berg to get out of the way. I think the riveters did a fantastic job, heating the rivet, throwing it up, and popping it in. That ship was designed for the North Atlantic in terms of waves, but certainly not for impacts with icebergs. I think high-pressure zones factored into the disaster. We did some calculations on the plates, and then worked out the force on a rivet. It seemed to be more than enough to pop a rivet. It’s like a can opening. You pop one and the fracture extends, and it gets easier from there. You can’t say she’s “invincible” to loads for which she was not designed.
High-pressure zones and pressure melting are also the seat of ice-induced vibration.
In the Molikpaq structure in the Beaufort Sea (right) in 1986 there were severe ice-induced vibrations. Ice was pushing in, the structure started vibrating, and crushed ice was ejected, forming piles that were meters high. There is very high pressure associated with the crushing process. When the ice recrystallizes, it softens under pressure, and behaves like quite a different material.
We believe that vibrations occur because of pressure melting: a change in pressure within the high-pressure zone. When the zone fails, the load drops and the melting reverses, and then the load increases again, resulting in an alternating load. There can be synchronization between different high-pressure zones interacting with the structure.
It’s important to design the structure for both global loads and local loads. When ice is confined and is not subject to cracking, high-pressure zones form, up to 70 megapascals locally on very small areas. They cause problems for local design. There is very high local punch, like there was with the Titanic. You can get a zone that is relatively fracture free, resulting in a significant high-pressure zone. It can tear the plate apart, like with the Titanic. If you have a vessel carrying oil, there might be a significant environmental consequence if the plate tears.
Floaters have double hulls, which adds to safety. Even though we use welded joints, it could still tear the plates and the welds, if not designed for the appropriate local pressure. Access to full-scale data helps a lot. There have been a lot of expeditions up north with instrumented ships. There was one this last summer. In the past, in planned experiments, strain gauges were placed inside the hull. They might ram that vessel into the ice, during which they measure the pressure distribution. Based on this data, we can develop criteria for various ice scenarios. If I’m working on a design, there is nothing better than full-scale data.
At the Arctic Technology Conference here in St. John’s in October, I am presenting a paper, “Estimation of Ice Loads Using Mechanics of Ice Failure in Compression”, which focuses on high-pressure zones and the use of mechanics for design. It highlights the necessity of using full-scale data, and also how mechanics can supplement that considerably.
How has the melting of the Greenland ice sheet been impacting oil and gas operations?
It has resulted, I believe, in possibly increased release of icebergs and ice islands. I understand that the people who have been working on this have deduced that the ice islands have come from Petermann Glacier. I worked intensely on the problem of designing for icebergs and we built software here, using the Monte Carlo method, doing repeated simulations of icebergs and structures, which allows for solving complex problems without trying to solve by using a single equation.
How is climate change taken into consideration when designing an offshore structure in an area that is currently ice- and iceberg-prone?
I am certainly not a climate denier. Glaciers might calve more often for a while, if the warming trend continues. There might be increased aerial density. For shipping, first-year ice is a big hazard in the Beaufort Sea. It might in some years be clear of ice. But the presence of ice has always been very variable. There is tremendous variability.
If you go into areas where multi-year ice is present, there are places where the thickness is hardly diminished. If you want to go through the Northwest Passage, in some areas you can do so much more easily, but you still have to go through the channels between the islands to get all the way through, and it can still be very demanding. Multi-year ice in some cases hasn’t diminished. We believe the thicker ice is still a big hazard. There is no sign it’s totally disappearing. First-year ice may be diminishing, but multi-year, with the brine drained out of it, is harder. A multi-year ridge occurs when first-year sea ice compresses against itself, fractures, and breaks into smaller pieces, or blocks, that stick together. If this jumble of ice remains, it becomes a multi-year ridge. There is a zone in the Beaufort Gyre near the Canadian Archipelago where you get ridges forming. It gets thicker and thicker until it’s thick enough to survive next summer. A lot of it gets pushed in between the islands in the Canadian Archipelago. It’s quite hard to deal with. Multi-year ice poses the main hazard for shipping in the Arctic.
Aside from the anthropogenic reasons for climate change, there are natural reasons why there is a warming trend. There are cycles related to other factors. Some people are implying that the Arctic is becoming like the Mediterranean, which is totally ridiculous. Ken Croasdale, Bob Frederking, and Peter Noble, co-authors with me of the CAE study “Engineering in Canada’s Northern Oceans: Research and Strategies for Development”, are vastly knowledgeable about ships in ice. We need to put more money into Arctic research and increase efforts to deal with these problems to inform what we can do in the Canadian Arctic.
In general we design for present conditions and then extrapolate them out over time, and then look at some sensitivities and possible future changes. Often there is more variability than trend. It is difficult, for example, to detect an increase or decrease in aerial density of ice features.
Since the Titanic, the International Ice Patrol has produced data every year. We’ve been mapping the months and years for this area based on their data. Some years there are no icebergs at all in a given area, some years there are many. The other hazard is calving. You get small icebergs and bergy bits, accelerated by waves. (A bergy bit is glacier ice, 1 to 5 meters above sea level and 5 to 15 meters long.)
Wave-induced motions increase the kinetic energy in impacts against a floating structure. It’s harder to detect icebergs in a high sea state, which is an issue for floating structures. High sea states are associated with wind and rain. Waves can accelerate an ice piece, and there’s a decreased chance of detecting it. The joint probability of having a very extreme wave and having an iceberg in there at the same time is very low. Lesser sea states are more common, particularly for floaters. The larger icebergs are generally towed and the floating systems can disconnect and move off location. With fixed structures, you have to worry about bigger bergs. While they are not affected by sea states as much as small ones, they might be the biggest hazard in this case.
Who would you say is the leader internationally in designing for ice?
I’d say C-CORE is the leader. They have a very good understanding of risk-based design and probabilistic methods, put together in very elegant computer programs that can help us design. And they have an appreciation of full-scale data. The group here has analyzed all kinds of full-scale datasets including both ships and structures in ice. Memorial University is certainly amongst the top few for ice research, particularly in medium-scale testing. There is vast experience from work on ships in ice, such as experiments conducted by people like Claude Daley. We have a lot of experimental work going on, and collaborations with the National Research Council of Canada. Put all those facilities together, and it makes a very strong effort—certainly in the top few.
(As published in the October 2016 edition of Marine Technology Reporter)
Read Designing for Ice with Ian Jordaan in Pdf, Flash or Html5 edition of October 2016 Marine Technology
Other stories from October 2016 issue
Content
- Silence Your Ships page: 12
- FRV for Bangladesh page: 14
- Delving Deeper with AUVs page: 18
- Exploring Alien Oceans with AUVs page: 22
- AUVs Under Ice: Past Milestones, Promising Future page: 32
- Designing for Ice with Ian Jordaan page: 38