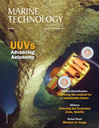
Page 37: of Marine Technology Magazine (April 2020)
Read this page in Pdf, Flash or Html5 edition of April 2020 Marine Technology Magazine
subsea system and high-speed fber-optic project development followed the recom- remote analytics can be performed, these communications enables responsive re- mendations and technology readiness lev- digital solutions delivering ABB’s deep mote operations. el (TRL) defned in DNV RP-A203, which domain expertise from device to edge to provides a systematic approach to ensure cloud, thus benefting oil and gas industry that the technology functions reliably and customers. Jeremy Cutler, Head of Total’s
Realistic testing
As the resulting power distribution and within the specifed limits. Energy Research & Development Center in Stavanger, Norway, commented: control system is made up from several hun- “This disruptive, transformative technol-
Benefts for the oil and gas industry dred unique critical components operating
The successful testing of the ABB system ogy opens up unexplored areas, and the under various stress conditions, a clear and power of the collaboration, which started has a number of implications for the oil and pragmatic testing structure was put in place gas sectors. The use of the system means with a clear defnition of the scope of the in order to learn the behaviors and limits of different designs, thus helping to mitigate that the operating lifespan of an existing work and combined the best talents in a the risk of failure before prequalifying for facility can be extended through more fresh design from the bottom up, resulted full-scale prototypes. Therefore, starting cost-effcient tie-ins, requiring minimal in a ‘subsea factory’ concept employing topside modifcations. In addition, future green power from shore to subsea maxi- with simulation and laboratory tests, mate- developments can be phased in and easily mizing the exploitation of potential subsea rials, components, sub-assemblies and as- resources. Partnerships are not new in the semblies were subjected to realistic stress adapted through an inherently more fex- levels in accordance with lifecycle profles ible system topology. With full production oil and gas sector – we compete in many before the fnal full-system 3000-hour systems installed subsea, long tie-backs no areas but we also collaborate – and in a big project like this the different parties can longer need multiple power cables or com- shallow water test was carried out. share the risk and share the rewards An
All tests were carried out in accordance plex umbilicals and in addition, electrically unmanned subsea factory facility provides powered solutions enable around-the-clock with API 17F Standard for Subsea Pro- duction Control Systems and included visibility of system performance. By using many benefts, with clean offshore power, more effcient use of energy and reduced
ABB Ability, the company’s digital plat- temperature, vibration, pressure and ac- celerated lifetime. The development f the form, more precise control and advanced carbon emissions.”
ABB’s sheltered-harbor test facility at Vaasa,
Finland, where the JIP 3000-hour shallow-water test validating the new subsea technology and proving its viability was performed.