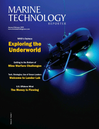
Lander Lab: Technologies, Strategies and Use of Ocean Landers
Moon landers held my attention in the 1960’s as a teenager. Unmanned robotic vehicles like Surveyor, descend out of a dark sky onto an alien world, and took the first look around.
The deep and dark ocean seemed as distant and alien. SEALAB II, bathyscaphe Trieste, and the Scripps Institution of Oceanography in my hometown of San Diego had immense gravitational pull on my curiosity.
Ocean Landers, unmanned robotic vehicles, like Scripps Professor John Issacs’ Monster Camera, descend out of a dark sea onto an alien world, and took the first look around. Our first glimpse of The Other Earth.
Why Landers?
There are multiple classes of unmanned undersea vehicles (UUVs): Remotely Operated Vehicles (ROVs), Autonomous Undersea Vehicles (AUVS), Gliders, midwater SOLO drifter floats, towed platforms, and Ocean Landers, also called “free vehicles”. Each unmanned vehicle has a unique set of strengths and weaknesses, often complementary to another class. Ocean Landers are the oldest, but an overlooked platform for many seagoing projects.
Ocean Lander construction is straightforward: Buoyancy high, weight low for stability. The vehicle is self-buoyant, weighed down by an expendable anchor, usually iron. Proper design minimizes cross-section perpendicular to the direction of vertical travel, known as the vehicle’s frontal projected area. Water drag provides a terminal velocity. A positively buoyant lander floats above its anchor, making it independent of the seafloor rocks, mud and slope. No legs required for many missions. A dual or triple redundant release system gives multiple chances for return. Designers can choose from a suite of release mechanisms to suit the mission profile. On return to the surface, the vehicle becomes a spar buoy. It’s top most structure is raised out of the water, providing a line-of-sight to the ship for a radio and strobe light, or to the sky for a satellite tracking system. A flag is always a good thing, and reflective tape can help with a searchlight at night. We always add a tag for someone to contact the lander’s owner should it go AWOL. Davy Jones can be such a prankster.Figure 3. Then-and-Now. Munk/Snodgrass Deepsea Tide capsule (1968). Twin 24” diameter, 1” wall, spun 7075-T6 aluminum spheres provide buoyancy and house electronics. A 15m EM cable tethers the spheres to the sensor frame. Modified automotive wet cell batteries provide system power and negative ballast. The battery ballast remains on the seafloor when the capsule is recovered. (Photo Credit: Deep Sea Instrument Capsule, Frank E. Snodgrass, Science, Vol. 162, No. 3849 (Oct. 4, 1968), pp. 78-87.)
Ocean Landers can carry every imaginable sensor and sampler. They can even recover sediment cores by using a clever sword-in-a-sheath design by a chap named David Moore of the USN NEL-San Diego. He had to solve the “core extraction problem” caused by gloppy mud. Sam Raymond and Benthos turned this idea into a product it sold for years called the Pogo Corer.
Materials have to handle the pressure. A lunar lander travels 400,000 km to the moon and the ambient pressure changes 1 bar. Ocean vehicles experience that every 10m of depth. Some buoyancy materials overcome the pressure by specific gravity and bulk modulus, other buoyancy materials do it by displacement and the compressive strength of the material.
We’ll discuss all of these elements in the course of this column. Like Edison’s ratio of inspiration-to-perspiration, our profession calls it R&D, with emphasis on the D.
The concept of ocean landers/free vehicles for geophysical research was first proposed in 1938 in a brilliant paper by Maurice Ewing (Lamont) and Allyn Vine (WHOI), titled “Deep-Sea Measurements Without Wires or Cables,” published in Transactions of the American Geophysical Union. Many of its insights are still valid today. The authors cited operational benefits of ocean landers/free vehicles including:
- Much less specialized and expensive equipment required on the ship;
- Long, undisturbed placement of recording instruments on the bottom;
- Recall by time-clock or signal from the surface;
- Once a free vehicle is released, the ship is free to move to another position to deploy another free vehicle, meaning large survey areas are possible;
- Stations at specified distances or heights off the bottom;
- Unlimited depth;
- Ballast release by contact with the bottom is possible if no bottom dwell time is required;
- Operators can follow progress down and up by sound-ranging;
- Initial lifting force when leaving the seafloor may be multiplied by a pulley-system;
- The ballast is on the bottom and left behind, minimizing the danger of being stuck in the mud.
Other benefits not mentioned in the Ewing-Vine article include:
1. Flexible Configuration: A lander can be configured to whatever ship-of-opportunity presents itself. Small vessel, small lander; Large vessel with an A-frame, larger lander. Lander frames can be bolted together like building blocks. Side pods provide additional buoyancy or instrument bays;
2. Interchangeable payloads: Like a pick-up truck to the deep sea, if a payload fits within physical, weight, electrical, and control parameters, it can be delivered to any place in the ocean, and recovered on command;
3. Profiler: The zone of interest maybe the water column between the surface and seafloor;
4. Ships-of-opportunity: A less specialized but appropriately sized seaworthy vessel may be found in a smaller harbor closer to a point of interest, during a more advantageous time, at a more modest cost;
5. Test bed: Ocean landers make excellent test beds for systems destined for more advanced vehicle types or more advanced Lander missions. Materials, sensors, cameras, lights, batteries, thrusters (without props), solenoid releases, recovery beacons, acoustic comms, and a lot more can be tested using small landers, from small vessels, with smaller budgets, and less worry. It doesn’t bet the farm to test a hunch;
6. Training: An ocean lander provides operational training on launch-and-recovery techniques for larger systems, giving engineers and scientists the field experience and confidence that comes from a successful deployment and recovery;
7. Collaboration: Researchers can combine a variety of instruments to measure and sample the ocean from distinctly separate, but interacting points of view. With similar landers at dispersed universities, researchers need only plan on bringing their instrument as their colleagues have a similar lander, so they know their instrument fits;
8. Persistence: Expanding on Ewing & Vine, a lander can remain on the seafloor for an entire year or longer if needed. Using glass, plastic and titanium, landers are capable of long duration deployments of even multiple years. One application may be to surround the base of an offshore oil platform where they can continuously monitor for a hydrocarbon leak, communicating with each other and back to the platform;
9. Baited lure: The lander can be used to lure animals towards its position by the use of bait. Low-light cameras using red LEDs can image animal behavior without disturbance, or await the arrival of an ROV or manned submersible;
10. Scout: Landers can precede a manned submersible or ROV operation to determine a specific area of interest. They can also stand-by as a rescue vehicle, using their full buoyancy to help bring another vehicle back to the surface;
11. Pack horse: Working with manned or unmanned vehicles with mobility but limited VB to carry samples, a lander can act like a chest-of-drawers to hold the samples collected by the mobile craft. The mobile craft is recovered first, and the lander is recalled with its payload to the surface afterwards;
12. Cheap anchors: Only scrap iron is needed for anchors, so the ballast weight may be purchased in the port of operation, saving the cost of shipment of a heavy drop weight;
During COVID, when barbell weights became very expensive and hard to find, the idea came to make ferrocement anchors, replacing the gravel with readily available scrap steel stampings. The scrap stamped steel was valued at 4 cents/pound. The anchor worked great, and would later corrode and dissolve into ocean friendly materials. Non-magnetic SS stampings are likewise available, if magnetic signature is an issue.Figure 5. Ferrocement expendable anchors, where steel stampings replace coarse gravel in the mix. Cheap, heavy, and biodegradable. Photo by Kevin Hardy.
13. Shipping: A lander and its surface support gear can be shipped by overnight air freight from point-of-origin to point-of-operation, allowing rapid deployment to an active site of interest. One research group brought a small lander as check-on luggage to Fiji, where they used it to gather samples at a maximum depth of 2km.
14. Disruptive technology: Landers are simple enough to be used by any size institution anywhere in the world. I’ve mentored high school through graduate students in lander design and construction, and had them build and deploy their own. Their use in the ocean at any depth for any length of time provides unique observational and sampling capability. Ocean Landers are a UUV technology that empowers and enables all nations during the UN Decade of Ocean Science for Sustainable Development (2021-2030).Figure 6. Without winch and wire, or the big boat. The author, Kevin Hardy, then with Scripps, deploys Ocean Lander DOV Patty into the 10,700m Sirena Deep off Guam in 2011. The Munk/Snodgrass design influence is easily seen. Our ship-of-opportunity is the 62-ft Super Emerald out of Saipan. (Photo by Elizabeth Strickland, IEEE)
It was noted by Ewing and Vine that locating the free vehicle after it had returned to the surface was a serious problem. Today, Ocean Landers have the advantage of RDF and satellite trackers. They sink and rise pretty fast. Currents are relatively thin layers, and the vehicle passes through them fairly quickly, minimizing offset. The surface location problem has become more manageable.
Landers have been my muse to develop new undersea vehicle component technologies. Looking to send landers to the deepest trenches on a limited budget, I was looking for both buoyancy and housings. In 2001, I approached Gerald Albich, then General Manager of the German company Nautilus Marine Service (NMS), manufacturers of the impressive Vitrovex line of hollow glass spheres for ocean science. My suggestion was to leave the 17” OD the same, but make the ID smaller, creating a thicker wall. We discussed modifications to the tooling. The thick-wall glass spheres, serving as both flotation and as a housing, would be capable of reaching the floor of the deepest ocean trench. With funding from Japan, whose researchers wanted to study the deeper waters of the western Pacific, NMS completed the development. Exploration of the ultra-deep sea changed dramatically after that.
Ocean Landers inspire such invention. Come along on the journey.
References: Copies of the Ewing & Vine (1938), Snodgrass (1968), and other papers are available for download at <https://www.globaloceandesign.com/other-lander-reference-papers.html>.
Post-script: I am very grateful to MTR Editor Greg Trauthwein for his invitation to write this column. I am, in perhaps my favorite self-image, an educator. There is enough material to continue the column for some time, and perhaps, in the end, bind the articles into a Handbook of Ocean Lander Design. We imagine supplementing the articles with video “How to’s”, and share some drawings of useful lander lab gear. We’ll share experiences and designs from other Landerians from around the world, and suggest Yet-To-Be-Done ideas waiting their turn.
I look forward to receiving your comments, suggestions, and most importantly, your contributions to future articles. Please send your thoughts and photos to me at: Kevin Hardy <[email protected]>
Listen to Kevin Hardy discuss the rationale behind the new "Lander Lab" article series for Marine Technology Reporter.
Read Lander Lab: Technologies, Strategies and Use of Ocean Landers in Pdf, Flash or Html5 edition of January 2022 Marine Technology