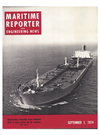
Page 12: of Maritime Reporter Magazine (September 1974)
Read this page in Pdf, Flash or Html5 edition of September 1974 Maritime Reporter Magazine
Numerical Control's Impact
On Shipyard Management
Thomas Lamb*
The searching for better ways to accomplish specific items of work should be a never-ending task of engineers and manage- ment. Although it is applied in shipbuilding, the determination and implementation of new ways is generally slow compared to other industries. This is usually stated to be because shipbuilding is a custom-building heavy in- dustry, building one of a kind products in a fiercely competitive world where any significant change usually involves large cap- ital expenditure.
One of the important changes in shipbuilding methods and one which allows others to be possible is the use of numerical-control (N/C) production machines. The
N/C production machines for ship- yards are limited presently to marking and burning machines and frame-bending machines, al- though commitments have been made for other shipyard N/C ma- chines and N/C controlled process- ing lines and plate-forming ma- chines have been proposed.
The use of N/C in the shipyard has had a significant effect on most methods and departmental organization.
Although it takes a relatively short period of time to learn the basic coding of a specific com- puter-assisted programming sys- tem for the preparation of N/C data, it requires considerable ex- perience in the full use and man- agement and control of such N/C software systems to be able to set up an effective and efficient
N/C programming group and to integrate it within the existing shipyard organization. Even when the programming instructions are fully understood, the success of the system is not guaranteed.
This part is less than 25 percent of the total effort required to ensure an effective N/C data- processing group. It appears that it is more difficut to set up the organization and its operating procedures than it is to obtain working knowledge of the pro- gramming methods.
N/C or Not N/C?
The application of N/C to ship- yard processes has been discussed and the benefits of the use of the system covered in previous papers and articles. However, is it the panacea for all shipyards, or are there certain conditions that must *Mr. Lamb, manager of the Marine
Division, Value Engineering Company, presented the paper condensed here before a meeting of the Hampton
Roads Section of The Society of Naval
Architects and Marine Engineers. exist before it becomes beneficial ?
Does it depend on ship type and size, or shipyard size, and are there other alternatives today which provide meaningful com- petition to N/C production ma- chines ?
As may be obvious, there are no easy and clear-cut answers to these questions, as they involve many factors which are not even constant from one shipyard to another. However, from the ex- perience of shipyards using at least some aspect of N/C, it can generally be stated that N/C ap- plications always have improved the process and resulted in eco- nomic savings, regardless of these factors.
Guidelines for the use of N/C in other industries can be studied as a decision aid for a shipyard.
It is claimed that a company is ready for N/C when: 1. The number of identical job runs is relatively small. 2. The average part has a fair degree of complexity. 3. The parts are subject to fre- quent design change. 4. Inspection procedures are lengthy, difficult and, therefore, costly.
In order to determine the size of the N/C data-processing sec- tion, an estimate of the total manhours per year is necessary.
A rough estimate of the total manhours required, utilizing a second generation computer-aided lofting (CAL) system, can be obtained from Figure 1. Table 1 can be used to analyze the man- power requirements for the N/C data-processing section. The ex- ample given in the table is the basis for the manning shown in
Figure 2. It can be seen from the example that two ships, each of a o o 30 14 3
O £ a 10 /ci / n av r-P- /4
A* < s
G u/* 10 11
LBP 100
Figure 1—Total computer-aided lofting section manhours, in- cluding all necessary manual lofting for four classes of ships. new and different design, are forecasted for each year and that the work for one will be com- pleted before the other is com- menced. This is obviously an idealized case and difficult to ob- tain in real life.
Methods and Organization
The introduction of N/C pro- duction machines along with com- puter-aided lofting systems have had noticeable effect on both shipyard methods and organiza- tion. While it is true that the use of a computer-aided lofting sys- tem could be set up so that it simply replaced a manual system with no changes to the existing organization, it soon becomes ob- vious to the users that changes should be made in order to gain the full benefit of the system. In fact, some shipyards using com- puter-aided lofting systems have
STRUCTURAL WORK PREPARATION
DEPARTMENT HEAD
STRUCTURAL PRODUCTION
ENGINEERING MANAGER
N/C DATA PROCESSING
MANAGER 3 File Clerks _ Assembly & Erection
Preparation Group
Structural Material
Ordering Group ! Sub-assembly Weight & Center Group [GL+4] [GL+2] [GL+1]
Systems Analyst
Fairing & Shell
Development Group
Parts Generation J
Nesting Group
Validation &
Liason Group _ N/C Drafting
Machine [GL+3] [GL+11 ] [GL+8] [2]
Figure 2—Recommended organization (and manning) of structural-work preparation group for capability of two different large ships per year. made significant changes to their organization, either at the time of implementation of the system or very soon thereafter. These changes usually result in improve- ments far in excess of those di- rectly related to N/C but, of course, are brought about by the use of N/C. In other words, the application of N/C has a snow- balling effect; the extent of which is only limited by the attitude and capabilities of the individual ship- yard staff and management.
A possible setup, using a com- puter-aided lofting system, is shown in Figure 3. The require- ments of modern shipbuilding structural fabrication and assem- bly methods suggest that a different approach to structural engineering is required, and the use of a second-generation com- puter-aided lofting system pro- vides the means whereby this can be accomplished.
It is suggested that the usual practice of preparing a very de- tailed structural drawing for each subassembly is no longer neces- sary, nor is it the best method.
An engineering information pro- cedure should be established that avoids duplication and ensures that adequate information is pro- vided to the production depart- ment. It should also be set up so that changes can be effectively managed and controlled. The use of computers for this control is a natural continuation to computer- aided lofting. A possible approach utilizes the usual structural-design drawings required by the classi- fication society, the shipyard's structural-standard detail booklet, an erection and welding sequence booklet, and assembly and weld- ing booklets for each type of sub- (continued on page 19) 60
Maritime Reporter/ Engineering News