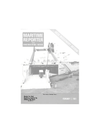
Chesapeake SNAME Discusses World Shipbuilding Practices
A discussion-provoking paper titled "Shipbuilding P r a c t i c es Around the World" was presented by Jay J. Hassani of Century Engineering, Inc., Baltimore, at a recent meeting of the Chesapeake Section of The Society of Naval Architects and Marine Engineers.
In his paper, Mr. Hassani reviewed the facilities used by various shipyards worldwide in carrying out selected phases of the shipbuilding process with significant differences in approach being highlighted. In addition, the effects of the shift in emphasis from building increasingly larger ships in the 1960s and early 1970s to environmentally safer, more fuel-efficient designs of the present clay were discussed.
He believes that f u e l - e f f i c i e nt ships with energy-saving propulsion systems, ship conversions, offshore drilling and production platforms, and other non-shiprelated work will occupy the w o r l d ' s shipyards during this decade.
In his description of shipbuilding facilities, Mr. Hassani emphasized the transition to more technologically advanced and automated techniques in ship construction, especially by nations in the Far East and Europe. The gradual shift from conventional building ways and building docks to tandem fabrication in multisection graving docks was highlighted and the approaches taken by yards in Japan, Taiwan, Germany, and Portugal described.
Also, a number of examples of steel-handling t e c h n i q u e s were discussed, including the fabrication of modules of up to 700 tons in size. The facilities using these advanced approaches are ideally suited to series p r o d u c t i o n of ships; however, Mr. Hassani believes that the demand for large production runs of similar ships has declined and will continue to do so as a result of the world economic situation. In addition, the rising labor costs in the West has moved a large amount of the remaining series production to the Far East, leaving a number of modern yards in the U.S. and Europe with excess capacity and large capital i n v e s t m e n t s to amortize.
The impacts on the shipbuilding industry of the growing role of coal in meeting the world's energy demands were touched on by Mr. Hassani as part of his assessment of the changing complexion of the type of vessels that will be built during the next 10 years. As an alternative to the conventional bulk shipment of coal, he proposed the use of containers that could be filled at the mine to alleviate the negative environmental effects of standard coal shipment. These containers need not be of the conventional ISO form; instead, they would be optimized for bulk cargo.
The prepared discussions involved a number of extensive comments concerning some of the author's conclusions. Edwin Hood of the Shipbuilders Council of America felt that series shipbuilding is still viable, citing the 10 LNG carriers built by General Dynamics along with the six additional ones on order. He also felt that U.S. shipyards are as technologically advanced as any in the world, and only the lack of government support, and in some cases outright government hindrance, is responsible for the U.S. shipbuilding industry lagging behind those of other nations.
D.M. Mack-Forlist, a consultant, concurred with Mr. Hood's comments, and added that the fluctuating, u n p r e d i c t a b l e demand for ships make large capital investments by private yards unattractive without government assistance.
Richard W. Thorpe Jr. of J.J.
McMullen & Associates, Inc., addressed the concept of containerized shipment of coal. He felt that it would be difficult to surpass in economy and efficiency the present use of unit trains, high-speed loaders and unloaders, and wide, shallow-draft bulk carriers.
The ecological problems involved in coal handling could in all probability be handled in a more cost-effective manner.
Other stories from February 1981 issue
Content
- Irv H. Dennen Named President Of Fairbanks Morse Engine Division page: 4
- Sale Of IOT To Southern Natural Resources Closed —Executives Announced page: 5
- Two New River Terminals Added By Alter—Third To Be Constructed page: 6
- Dockery Succeeds Warden As President Of Raytheon Marine page: 6
- Omnithruster Awarded INMA Tuna Fleet Contract page: 6
- Gulf Fleet's 102nd Vessel Is Powered By EMD Diesels page: 6
- Newport News Acquires Plant In North Carolina For Sub Support Work page: 6
- Conference Papers On Coal-Fired Ships Available From Polytech page: 6
- Kongsberg Relocates To New Facilities page: 6
- Alvin Goodspeed Named General Sales Manager At GM-Detroit Diesel page: 7
- Bath Iron Works To Build $25-Million Training Simulator For U.S. Navy page: 7
- Port Of Galveston Announces Four Management Promotions page: 7
- Electro-Nav's New Watch Receiver Meets I M C O Requirements page: 7
- Avondale Lays Keel For Largest U.S.-Built Diesel-Powered Containership page: 8
- Cargo Ship For Philippines Owner Delivered By Hitachi page: 8
- Vemar Shipyard Delivers Its First Offshore Rig To Glendell Drilling page: 8
- Report On Domestic Offshore Oil Published page: 8
- Crane Manufacturers Friedrich Kocks And Peiner Have Merged page: 9
- Baxter Named President And Board Member Of The Foxboro Company page: 9
- MARINE DECK MACHINERY A REVIEW page: 10
- Swiftships Delivers GM-Powered Utility Boat To CO-MAR page: 10
- James Thompsen Heads Marketing Of Woolsey Commercial Products page: 10
- Sun Ship To Focus On Ship Repair Work page: 10
- Robert Scott Named Assistant Vice President Of Gibbs & Cox, Inc. page: 10
- SUNY Maritime College Gets $2,000 Grant From Gulf Oil Foundation page: 10
- SAME's Philadelphia Post Elects Officers — Pistilli Named President page: 12
- Waukesha Engine Will Manufacture Sulzer Diesels Under License page: 13
- Halter Delivers Large Pilot Boat For Middle East Service page: 14
- $142-Million Contract For Two Tankers Awarded To Bath Iron Works page: 14
- FMC Coffin Pump Will Produce And Distribute TCU Turbochargers In U.S. page: 14
- New National Officers Elected By Marine Technology Society page: 14
- Blancke Marine Awarded Design Contact For Inter-Island Combo Vessel page: 16
- Shipboard Habitability Conference Sponsored By SNAME April 7-9 page: 16
- Swiftships Takes Over Mangone Shipbuilding From Stewart And Stevenson page: 16
- Petersen And O'Hara Elected Vice Presidents For Todd's L.A. Division page: 17
- Stanwick Corporation Appointed Exclusive Agents For Fredriksstad page: 17
- Hitachi Zosen Gets Orders For Two More Semisubmersible Rigs page: 18
- Bethlehem Boston Yard 1980 Workload Of 80 Ships Equaled 1979 page: 18
- NASSCO Launches Products Carrier For Union Oil Company page: 18
- New Satellite Navigator Receiver Announced By Racal-Decca Navigator page: 18
- T.J. Lamb Named Systems Department Sales Manager At Engelhard Industries page: 18
- Navy Honors Sperry Contribution On 25th Anniversary Of FBM Program page: 19
- Jumboized 'Seawise Giant7 Is Now World's Biggest Tanker page: 19
- Haig And Hayward Honored At Navy League Annual Dinner page: 20
- Bethlehem's Beaumont Yard Had Outstanding 1980—Booked Into '82 page: 20
- China Shipbuilding Will Build Third Jackup For Santa Fe International page: 22
- Thomas Moran Named Chairman Of The Board For Moran Towing Corp. page: 22
- B&W Yard To Continue Technical Assistance To Samsung Shipbuilding page: 24
- Robert McCarthy Joins DEBEG Marine As Sales Manager page: 24
- Halter Marine Delivered 64 Commercial Vessels In 1980 page: 25
- Donald Chrisco Named Director Of Materials At St. Louis Ship page: 26
- Giant Belcher Barge Launched In Galveston page: 26
- NASSCO To Retrofit Three Tankers At Total Cost Of $19.8 Million page: 26
- Zigler Yard Launches 80,000-Barrel Tank Barge For Louisiana Marine page: 26
- Advanced Vessel To Join Fleet Of Tidewater Marine Joint Venture page: 27
- Zidell Awarded Big Repair Job On Army Dredge 'Pacific' page: 27
- Jackup Rig For Foramer Completed By Hitachi page: 28
- Wall Shipyard Completed $11.5 Million In Vessel Repair Work And Service In 1980 page: 28
- ASNE Flagship Section Hears Report On Craft's Aerodynamic Enhancement page: 29
- Dock Express Transports Offshore Modules To Bahrain page: 29
- Bond And Houston Get New Posts In Texaco's Marine Sales Department page: 29
- Caterpillar-Powered Trawler Completed By G&W Industries page: 32
- Cadiz Yard Of AESA Delivers Three Containership Conversions page: 32
- Saint John Yard Selects Sperry, And Gibbs & Cox For Frigate Design Team page: 32
- NICOR Inc. Acquires Acadian Marine Service page: 33
- Subsidy Board Approves CDS For $1.7-Million Delta Line Retrofits page: 33
- Guralnick Associates Awarded Study Contract By State Of Alaska page: 33
- Two Big Bulkfleet Barges Christened At Quincy Yard page: 34
- Dravo SteelShip Delivers Three Towboats To Radcliff page: 34
- Wesmar's Scanning Sonar Has Long Range For Greater Efficiency page: 34
- C.G. Caras Rejoins Ogden Corporation As Vice President page: 34
- GE Reorganizes Its Installation & Service Engineering Division page: 36
- Gulf Oil Opens New Service Facility In Staten Island, N.Y. page: 36
- Students Present Papers At Meeting Of SNAME New England Section page: 36
- Brochure Describing New Diesel Lube Oil Available From Mobil page: 36
- Captain McVay Named Vice President Of Moran Towing & Transportation page: 37
- Mynaugh Appointed Engineering Manager At Interocean Management page: 37
- Robert Nystrom Named Division Chief At Anderson Associates page: 37
- Todd Gets $32 Million In Commercial Contracts- Earnings Up For Quarter page: 37
- Allis-Chalmers Named U.S. Licensee For B&W Slow-Speed Diesels page: 39
- Newport News Completes Jumboizing Of Two Tankers page: 40
- Marine Industries Hosts Reception For NYC Shipowners page: 40
- Gulf Fleet To Provide Five Vessels For India's Offshore Operations page: 40
- NKK Delivers Its First Car/Bulk Carrier With Hoistable Decks page: 41
- Naval Civilian Administrators Establish New Chapter page: 41
- IOT Announces Two Management Appointments page: 41
- Burmeister & Wain Delivers First Panamax Bulk Carrier page: 42
- Floating Weir Skimmer Collects Oil Spills In Harbors Or Offshore page: 42
- Todd-Seattle Yard Promotes Five—McDonnell Appointed Assistant General Manager page: 43
- Future Ship Designs Topic At ASNE Northern New England Section Meeting page: 43
- Hitachi Completes Jackup Drilling Rig For India page: 43
- $2.5-Million Order For SPM Inventory Buoy Awarded To IMODCO page: 43
- Executive Appointments Announced By Crowley Caribbean Division page: 43
- VHF Automatic Digital Direction Finders Announced By Simrad page: 43
- Blount Marine Delivers Deutz-Powered Cruise Vessel page: 43
- Chesapeake SNAME Discusses World Shipbuilding Practices page: 44
- Roland Malins-Smith Joins Concorde Line As Vice President page: 45
- New Brochure Describes Repair Facilities At Norfolk Shipbuilding page: 45
- F.A. Martin & Ottaway Expands Operation To United Kingdom page: 45
- Benson Named Manager Of Peterson's Hazardous Materials Division page: 58
- Derrick/Supply Vessel Now In Gulf Service For Tidewater page: 58
- Two Detroit-Powered Tugboats Completed By Manly Shipyards page: 58