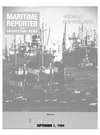
Fairbanks Morse Taking Major Steps To Improve All Aspects Of Customer Services Worldwide
In a move to strengthen its entire parts and service organization and to coordinate all field service activities for Fairbanks Morse Opposed Piston and Colt-Pielstick engines, the Fairbanks Morse Engine Division of Colt Industries is undertaking a major restructuring designed to improve all aspects of customer services worldwide.
As part of the restructuring, present parts and service facilities are being upgraded and modernized with the latest state-of-theart equipment, and new centers are being added. In addition, a new centralized warehousing network is being developed to service all locations. At its Beloit facilities, a new training center has been completed to provide handson engine service training for Fairbanks Morse and customer personnel.
As one of the first steps in its external restructuring, a regional distribution warehouse was created in Reno, Nevada, and established as its Western Service Region Headquarters. The warehouse is designed to complement the existing service shop in Seattle and sales office in San Francisco with improved inventory control and distribution effectiveness.
The location was chosen as it is central to the region's major markets and can absorb expansion as additional service facilities are added. In addition, a new fuel injection overhaul facility has been located at Reno which provides complete fuel injection service with new and modern equipment. This will allow Fairbanks Morse to have complete rebuilt and exchange assemblies in all locations to complement its new parts inventory.
Typical of the modernization that is taking place in all Fairbanks Morse Service Centers is the recently completed move in Norfolk, Va. The center now has the capability to handle complete engine rebuilding. In addition, the center is computer integrated with the central warehouse in Beloit to quickly process requirements for special and made-to-order parts.
Recently completed in Beloit is the new training school designed to give Fairbanks Morse and customer service personnel the finest in training on all Opposed Piston and Pielstick engines.
According to Tim O'Sullivan, vice president and general manager of the parts and service operation, when completed the Fairbanks Morse service organization will be one of the finest organizations of its type available anywhere in the industry.
Supporting Mr. O'Sullivan in the reorganization are: Michael Peterson, manager of marketing who will develop and implement the marketing and sales programs planned for both the parts and service segments of the operation; Mark Parsons, manager of distribution, who has the responsibility for parts order service and inventory control for spare and renewal parts in all stocking locations. He also manages the present central parts distribution center in Beloit.
Tom Skinner, manager of product service, who is responsible for developing and implementing all product and technical service programs and Roger Brenneke, manager of training.
The business is divided into five regions, four in the United States and one for export to provide a focus on customer activities.
Through its new and revitalized parts and service organization it is Fairbanks Morse's aim to provide every Fairbanks Morse and Colt Pielstick engine owner with the optimum service that will minimize their downtime and assure the maximum return on their engine investment.
Circle 38 on Reader Service Card
Other stories from September 1984 issue
Content
- Symon Appointed New Director Of Tankers At Stolt-Nielsen page: 5
- SOFEC Awarded NavSea Contract For Offshore Mooring Terminal page: 5
- Metric Constructors Win $3.3-Million Contract page: 6
- Western Gear To Build And Sell Rademakers Epicyclic Transmissions page: 6
- I MO AB Of Sweden Offers New Products Literature page: 6
- Sperry Gets $62.8-Million Navy Contract For Frigate Combat Systems Work page: 6
- New HEET Fuel Additive Saves Time And Money By Preventive Maintenance page: 6
- Fairbanks Morse Taking Major Steps To Improve All Aspects Of Customer Services Worldwide page: 7
- Two Key Appointments Announced By Halifax Industries page: 7
- A.J. McAllister Sr. page: 8
- S.S. United States To Auction Contents Prior To Total Renovation page: 8
- Imi-Tech Offers Catalog Of Insulating Products For Marine Applications page: 8
- High-Speed Ferry For Hong Kong Owner Launched At Vosper Thornycroft Yard page: 9
- Marinette Marine Lays Keel For Second Mine Countermeasure Vessel page: 9
- Maritime Innovation — Practical Approaches '84 International Symposium page: 10
- NKK Completes World's First Offshore Steel/Concrete Drilling Platform page: 12
- Manson Construction Builds Pacific Northwest's Heftiest Floating Crane page: 12
- Krupp Shipyard In Duisburg Delivers Two Harbor Tugs To Guinea page: 14
- NKK To Build Floating Offshore Production Unit For Norwegian Consortium page: 14
- Van Houten To Head New Parsons Brickershoff Marine Facilities Unit page: 14
- Lykes Gets Title XI Guarantee To Upgrade Fleet Operations page: 15
- USP&I Home Office To New York Area— Other Changes Announced page: 15
- American Marine Gets $390,000 Contract For Two Cutterhead Dredges page: 15
- MARINE SALVAGE page: 16
- Crowley Named President Of Newly Organized States Africa Line page: 18
- Simplex Gets $5.7-Million MarAd Contract To Supply Petroleum Transfer System page: 18
- General Dynamics Quincy Yard Will Build Four Containerships For USL At Cost of $341 Million page: 18
- Scripps Institution Acquires Another Research Vessel page: 18
- RDI's Satcom I Communications System Approved By INMARSAT page: 18
- American Transport Asks Title XI On $17-Million Barge Conversion Work page: 19
- Canter Named President Of At-Sea Incineration page: 19
- Coast Guard Orders Schottel Jet Thruster page: 19
- SMM '84 International Ship, Machinery, and Marine Technology Trade Fair page: 20
- Tenn-Tom Waterway Project Nearing Early Completion page: 20
- BP And Harland And Wolff Forming Joint Venture For $145-Million SWOPS Project page: 21
- Naval Ship Maintenance & Modernization/Affordability page: 22
- The "Ultimate" Compact SSB page: 23
- IBM Appoints Marine Management Systems As Authorized Dealer page: 25
- Twin City Shipyard Lays Keel For Gulf Coast Trailing Dredge page: 26
- Pearlson Begins Construction Of World's Largest Ship Transfer System page: 26
- Screw Compressors Improve Air Conditioning Reliability page: 27
- NASSCO Receives Exxon Contract For Two Alaska-Class Tankers page: 28
- Tacoma Boat Division Gets $210,000 Contract To Build Propeller Hub Assembly page: 28
- AMMCO Licensed To Market O&K Dredging Bucket And Cutting Wheels page: 32
- Westinghouse Electric Awarded $2-Million Navy Contract For Frigate Study page: 32
- John Cave Appointed Vice President For Boland & Cornelius page: 33
- Norwegian Caribbean Acquires Royal Viking Line For $240 Million page: 33
- Marinette Marine Corporation Gets $24~Million Navy Contract To Build Six Yard Patrol Craft page: 34
- New Drydock At Halifax Shipyard Operating At Close To Capacity page: 34
- Stephens-Adamson Wins Ship Unloading System Orders Worth $12 Million page: 35
- Ice-Strengthened Ship Chartered By Navy's MSC From Central Gulf Lines page: 35
- Penn Ship Awarded Navy Contract For Overhaul And Maintenance Of Frigate page: 35
- John Deere Developing Family Of Rotary Engines page: 35
- Unique High-Speed Catamaran Delivered By Nichols Brothers page: 36
- Specialized Support Vessel 'Anfitrite' Acquired By O.D.S. Italia S.P.A. page: 36
- Moss Point Awarded $3.6-Million To Build 15 Barges For U.S. Navy page: 36
- WEST GERMAN SHIPBUILDING page: 38
- CORE Canadian Offshore Resources Exposition page: 38
- Meyer Named Assistant Vice President-River Area Of National Marine Service page: 43
- New Harbor Navigation System Designed To Increase Operating Revenue And Safety page: 44
- Murdock And Hunt/Leslie Use Computer To Design 'Compliant' TLP Coupling page: 45
- Samsung Wins $45-Million Contract To Build Huge Bulker For Australian Firm page: 46
- WABCO Fluid Power Adopts Worldwide Sales And Marketing Strategy page: 46
- $79-Million Coast Guard Contract Awarded to Bollinger Shipyard page: 46
- New Busiship™ System Brochure Available From Nav-Com page: 46
- Rose Named Vice President Of Mechanical Equipment's Marine Products Group page: 47
- MSC Forms New Unit To Oversee Operations Of Fast Sealift Ships page: 47
- Independent Tests Show Drew Ameroid's Amergize® Cuts Fuel Consumption page: 47
- Sulzer RTA Engines Will Power Two Containerships Building In Germany page: 48
- MonArk Delivers Fire Boat To Memphis Fire Department page: 48
- Penn Ship Provides Emergency Repairs For Two Foreign Ships page: 48
- Smith Berger Marine Names Two East Coast Distributors page: 48
- Sperry Opens New Facility In Panama City Beach, Fla. page: 51
- AMPS Appointed As Service Facility For MaK Diesels page: 52
- Halifax Shipyard Completes Major Damage Repair Contract page: 52
- Big Towing/Supply Vessel Launched At Moss Point Marine page: 52
- Serck Evaporators Installed In USSR Fish Factory Ships page: 53
- Third USN Rescue/Salvage Ship Launched At Peterson Builders page: 54
- USS Seamless Pressure Vessels Detailed In New Catalog page: 57
- ASRY Completes $3-Mlllion Overhaul Of Mobile Offshore Jackup Drilling Rig Dana page: 57
- Todd Awarded $10-Million In Contracts By Australia For Technology Transfer page: 58
- First Oceangoing Sail-Assisted Bulker Delivered By NKK page: 63