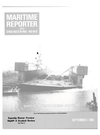
Cincinnati Gear Completes Testing Of New, Sophisticated Marine Drive For Navy T-AO 187 Class Oilers
Last month the Cincinnati Gear Company successfully completed back-to-back full-load testing of a sophisticated new marine drive for the U.S. Navy's new T-AO 187 class of fleet oilers. These ships, powered by two Colt-Pielstick PC4, 16, 272- hp diesel engines, represent a giant technological step forward for the Navy. The essential elements in the new T-AO gearboxes are the carburized, hardened and precision ground (CHG) gears having a highpower density. CGCO, under contract to provide these main propulsion gearboxes, stated they developed a cost-effective, high-performance drive package that is stronger, quieter, and 35 percent smaller than a conventional design using through-hardened gears.
CGCO's high-performance marine facility, Plant III, is utilized to manufacture and test these types of products.
Weighing 23 tons, the surfacehardened bull gear is the largest designed and manufactured in the free world. The T-AO back-to-back test stand is the seventh and largest facility of this kind that Cincinnati Gear has designed, built and operated.
CGCO is the first U.S. company to offer back-to-back testing in this size range.
Incorporated into each gearbox are unique features, such as single helical coarse pitcb surface-hardened gearing, thrust collars for axial load canceling, integral PTO, threepoint mount configuration, and an input quill shaft for main reduction pinion isolation.
The full-load, back-to-back test arrangement had the port and starboard units mounted with the input and the output shaft flanges facing each other and connected with appropriate couplings. The input coupling system incorporated a torque meter in the input quill shaft isolation system to monitor applied torque. The output flanges supported, and were connected by, a large custom-designed hydraulic torque applier.
The "load loop" was accelerated to speed by a 1,000-hp variable speed motor driving the PTO shaft flange of the port unit. This motor was sized to overcome gear mesh and journal bearing power losses.
With these key elements in place, virtually any power/speed combination within the design envelope could be simulated. The tests have established basic performance parameters while the units were subjected to a closely simulated shipboard operating environment in terms of torque, speed and mounting arrangements.
The hydraulic load cell in this test stand in capable of applying loads in excess of 13,000,000 lb.in. torque and 25,000 horsepower. For the TAO test the unit operated for 25 hours at 100 percent of rated power and speed—16,272 hp at 95 rpm with 900,000 lb.ft. of torque. To demonstrate adequate design margins, the unit was operated at 115 percent of rated power. This backto- back full-load test confirmed that the units meet given specifications at rated power and speed.
Full face contact of the main pinion/ bull gear mesh was verified by dynamic strain gage measurements of a series of bull gear teeth while the test unit ran at rated power and speed. Comparison of variations in peak strain gage measurements of the bull gear teeth verified the accuracy and correctness of the input pinion/bull gear longitudinal and profile corrections. These measurements confirmed that blueprintspecified tooth corrections are adequate to insure a uniform load distribution and allow evaluation relative to current ABS gearing derating factors.
The thrust collar concept demonstrated and proved the effectiveness of canceling the axial force directly at the single helical gear mesh.
Loaded thrust collar surfaces were inspected by visually comparing documented static collar pattern/ surface finish before testing and collar surface finish after testing.
Airborne and structureborne noise measurements taken throughout the test established a baseline data point for future large, coarse pitch, single helical, main reduction gears.
A post teardown inspection at the conclusion of the test program on both the starboard and port units provided engineering/quality assurance data of all gears, bearings, and thrust cones. The units were subsequently reassembled to production configuration, packaged, and shipped.
To the military there are obvious benefits of carburized, hardened and precision ground (CHG) marine gears for applications which are sensitive to noise generation and/or detection.
Currently there is a growing interest in CHG gears from engineers with commercial marine and other industrial applications looking for ways to better utilize space in a cost effective package.
For complete free literature on Cincinnati Gear Company equipment, Circle 63 on Reader Service Card
Read Cincinnati Gear Completes Testing Of New, Sophisticated Marine Drive For Navy T-AO 187 Class Oilers in Pdf, Flash or Html5 edition of September 1985 Maritime Reporter
Other stories from September 1985 issue
Content
- Tidewater Marine Acquires 5 Vessels From Otto Candies page: 5
- Hawker Siddeley/Kongsberg Collaborate In Venture page: 5
- American Air Filter Offers N e w Brochure On Cartridge Filters page: 5
- Big Supply Vessel 'Nicor Sailor' Converted By Eastern Marine page: 6
- Owen And Richards Named Managers At Honeywell page: 6
- MSC Announces FSS Award Totaling $30.7 Million page: 6
- Autronica's New NK-5 Unit Monitors Ship's Engine page: 6
- Grow Group Acquires Napko Coatings Division page: 6
- Bollinger Shipyard Dedicates Island Class USCG Patrol Boat Fleet page: 7
- Sulzer ZA40 Diesels Will Power Two Ferries Ordered In U.K. And Japan page: 8
- Cummins-Powered Construction Pushboat Delivered By Keith A. Record page: 8
- Tenneco Oil And Sohio Will Use Canmar Rig For Arctic Drilling page: 8
- Canadian Offshore Resources Exposition page: 8
- Shipboard Liquid-Level Sensor O f f e r e d By Tecnomatic Controls page: 9
- Maritime Association Installs New Officers And Directors page: 9
- Royal Cruise Line To Build Two Luxury Liners At Cost Of More Than $200 Million page: 10
- Goldstein Named Chairman Of COMSAT—Joseph Promoted To President page: 10
- Krupp MaK Consolidates In North America page: 11
- Innovative Triple-Screw Tugboat Launched By Halter Marine page: 11
- Truman Joins INDEECO As A d v e r t i s i n g Manager page: 12
- Moss Point Marine Delivers New Sternwheeler, Colonel page: 12
- Aluminum Boats Delivers High-Speed Crew/Utility Vessel To A&P Boats page: 12
- Matson Asks Bids On $30 Million Conversion of 'Matsonia' page: 14
- Brown & Root Awarded Feasibility Study Contract For Chevron Offshore Unit page: 15
- Congressional Maritime Caucus Establishes An Advisory Board page: 15
- SHIPLIFTING AND DRYDOCKING SYSTEMS page: 16
- OUTSTANDING RIG DESIGNS page: 16
- Bethlehem's Newest Jackup Design Can Drill In Water 600 Feet Deep page: 19
- Congressman To Address OMSA Meeting On Warehouse Vessels page: 19
- Alsthom Unit Strengthens Position In Norwegian Offshore Market page: 20
- Sandy Hook Dispatch Boat Delivered By Gladding-Hearn page: 20
- Saab Receives Order To Supply TankRadars From Tampa Shipyard page: 21
- Bertrem Products Importing Straub Couplings For U.S. And Canadian Distribution page: 21
- Conversion Of Fast Sealift Ship 'Regulus' Completed By NASSCO page: 22
- ASRY's 1984 Revenues Up Nearly 20 Percent page: 22
- Wartsila Wins Contract To Build Rig Transport Vessel For USSR page: 22
- E X P O S H I P Riomar85 page: 24
- Midland Ross Offers Free, 20-Page Brochure On Max-Gard® System page: 25
- Wilson W a l t o n Receives Two Contracts For Emergency Service page: 26
- Sale Of Imperial Survival Suits Approaches 100,000 page: 26
- Laursen Selected As New Managing Director Of Hemple Holding page: 28
- Owen And Richards Named Managers At Honeywell's Marine Systems Division page: 28
- CANADIAN SHIPBUILDING AND REPAIR YARDS page: 28
- Hollming Opens Louisiana Office For Marketing Aquamaster Product Line page: 29
- Two N e w Instruments To Measure C u r r e n t / V o l t a ge Introduced By Amprobe page: 29
- U.S. NAVY SHIP PROCUREMENT page: 30
- Holman and Wildasin Elected At Raymond International page: 31
- MIROS To Market New Products In U.S. page: 32
- Furuno Introduces New Low-Cost, High-Performance Loran Navigator page: 32
- NMEA Plans Expansion Of Interface Standard page: 32
- Kockums Completes Advanced Car/Truck Carrier For Wallenius page: 33
- Cincinnati Gear Completes Testing Of New, Sophisticated Marine Drive For Navy T-AO 187 Class Oilers page: 34
- New Alarm Reduces Boiler Failures, Diesel Failures And Repair Costs page: 34
- ADS Workshop Scheduled For October 2-3 In Chicago page: 35
- Seattle Yard GM Elected To Todd's Board Of Directors page: 35
- Caterpillar Offers 20-Page Catalog On Marine Diesels page: 35
- Wagner Wins $4.5-Million Contract For Steering And Control Systems page: 35
- Three Major Beth Steel Programs Highlight New Offerings To The Offshore Industry page: 36
- LiCausi Establishes New Boiler Consultant Firm page: 36
- West Coast Manly Shipyards Delivers Fisheries Patrol Vessel Leonard J. Cowley page: 36
- Free 12-Page Brochure On Marine Control System Offered By Forney page: 37
- Detroit Diesel Allison Announces Significant Engineering Advancements To Its Series 149 Engines page: 37
- Tyne Shiprepair Awarded Defence Ministry Contract To Convert Fleet Auxiliary page: 37
- Product Carrier 'Lucy' Christened At Hyundai's Ulsan Yard For Overseas Shipholding Group page: 38
- New Brochure Highlights Capabilities Of Marathon LeTourneau Offshore page: 38
- Aalborg Vaerft Awarded Danish Navy Contract For Seven Flex 300 Convertible Combatant Vessels page: 38
- McDermott Completes Twin Drilling Rig Ordered By Helmerich & Payne International page: 41
- Meyer Werft Shipyard Converts Containership Into Livestock Carrier page: 41
- Marine Drive Systems Announces N e w Shaft Systems page: 41
- N e w X-FLO Turbo Compressor Represents Major Advance In Impeller Technology page: 41
- Kockums Yard To Build Universal Ferry For Polish Shipping Company page: 41
- Transtema Kockumation Introduces New Computer System For Shipping Industry page: 41
- Huge Drydock At Bethlehem's New Sabine Yard Now Operational page: 42
- Marinette Marine Lays Keel For First Of 13 Yard Patrol Craft page: 42
- Avondale's Harvey Division Finishes Major Refurbishing Of Offshore Tug page: 44
- Meco's " T a r g a " Technology Boosts Water Maker Efficiency page: 45
- Orders A n d Deliveries Of T w i n - S c r ew Schottel-Tugs Continue W o r l d w i de page: 45
- N e w M e t h o d Of Inspection Used By Pacific M a r i ne Is Cost-Effective page: 45
- Report Shows Amerlock 400 To Be Cost-Effective Maintenance And Repair Coating page: 46
- MHI Develops Energy-Saving Marine Super Turbo Generating System page: 46
- Centurion Industrial Marine Offers The 'Crew Seat page: 47
- New Brochure Available From SKF Steel Couplings On Its OK Coupling page: 47
- New Instrument Manifold Improves Safety In Process Control Systems page: 47
- Inventive Machine Introduces Improved B l a s t / V a c u um Units page: 54
- Barksdale Controls Presents Line of Pressure Transducers page: 54
- Limitorque Introduces New Worm Gear Operators For Valve Or Mechanism Control page: 54
- Electronic Mail Techniques Save Thousands Of Dollars In Message Costs, According To NAV-COM Report page: 55
- Uniden To Introduce Six New Marine Radio Models At IMTEC Show In Chicago page: 55
- A New 12-Inch Radar From Krupp Atlas Elektronik page: 55