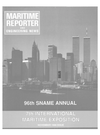
Modern Cargo Pumps For Tankers And Barges
*Editor's Note: Dipl. Ing. Heinrich Moller is general manager and technical director of Bornemann Pumps, Obernkirchen, West Germany.
Asmus W. Feck, P.E., based in Pawleys Island, S.C., is an international marine engineering consultant. This article has been excerpted from a technical paper written by Mr. Moller and Mr.
Feck.
Accurate cost estimating is a fundamental part of operating a profitable vessel. Nowadays, sea voyage time can be estimated fairly accurately.
However, one area that continues to defy accurate cost estimates is the time spent after the ship docks at a tanker terminal.
Generally speaking, the docking time of a tanker or barge is inherently dictated by the shore facilities and the design of the cargo pumping and loading systems, as well as the type and size of the main cargo pumps and drivers installed on board. Naturally, shipowners want to keep docking times as short as possible.
For this reason, every shipowner should guide the shipbuilder in selecting the best main cargo pumps for his needs. Ideally, they should be from a well-established, experienced manufacturer with an identifiable presence in the marine industry and a worldwide after-sale/ service network. And, as we believe, the external gear two-screw pump is the pump all modern tankers and barges should be using for their main cargo loading/unloading and stripping services.
In practice, it is difficult to estimate the discharge time of a tanker or barge equipped with reciprocating duplex piston cargo pumps. One problem is the inherent cargo product vaporization of highly volatile solvents as benzene, benzol and similar fluids. This characteristic tends to vapor lock cargo pumps suctions, and when it does, it automatically voids all unloading time estimates.
It is common marine engineering knowledge that piston-type cargo pumps cannot cope with high-volume percentages of vapors and air bubbles entrained in pump suction lines. From the very first moment of "lost suction" conditions, all reciprocating piston cargo pumps are exposed to "dry running" conditions if not stopped immediately. Continuous dry running operation wears piston rings, cylinder liners and pump valve chest suction valve services.
It can take more than 30 minutes before a piston-type cargo pump is able to regain suction flow.
Under these dry running conditions, i.e., with little or no suction flow passing through the piston pump liquid cylinders, it will be impossible to control or estimate the overall unloading time of the vessel.
Not all conventional centrifugal cargo pumps are self-priming. This means that if exposed even momentarily to lost suction conditions, they will not be able to pick up suction quickly. Hence, continued cargo unloading is not possible. The end result in most of these lost suction cases is that unacceptable delays in cargo unloading have to be accepted.
However, there are modern cargo pumps available that offer more efficient, versatile and economical operation.
Twin-screw main cargo pumps have been successfully used on board European motor tankers for many years.
The twin-screw cargo pump is a self-priming, positive displacement pump designed for cargo loading/ unloading and capable of tank stripping service. They combine the characteristics of a piston pump (positive displacement) with the characteristics of a centrifugal pump (rotating, pulse-free delivery) but without the inherent operating disadvantages of both.
Twin-screw pumps can be operated at speeds of up to 2,000 rpm.
Space requirements for them are relatively small, requiring as little as 50 percent of the space required for otherwise equal capacity piston pumps. And, equally important, the twin-screw pump offers absolutely continuous performance with suction line capability of up to 95 percent by volume of entrained air or gases. One of the biggest advantages a twin-screw cargo pump offers is the capability of extremely high suction lifts.
In the case of light viscosity cargoes, such as solvents, benzene, benzol, or even seawater, the two-screw pump can lift a suction vacuum of 24 in. Hg (about 27.5 feet). Furthermore, when pumping viscous cargoes, a viscous fluid film is formed around the pump screws. This film acts as a sealant and serves to increase the pump suction lift to 27.3 in. Hg (about 31 feet).
It is, of course, true that any amounts of entrained air or gas will reduce the actual flow at the pump discharge. These actual losses in discharge flow rates cannot be eliminated.
However, even under these trying suction conditions, unloading with twin-screw cargo pumps will never be disrupted unless the volume percentage of air or gases exceeds 95 percent.
It is also important to note that with their inherently balanced design, two-screw cargo pumps are far quieter running than equivalently sized piston or centrifugal pumps operating under the same conditions.
The observed noise level will be about the same as a well-balanced electric motor sized to drive the pump. And while it is possible to observe higher noise levels when pumping through too small suction or discharge piping, or with high air or vapor bond fluids, the increase in noise levels from these conditions will be less for two-screw pumps than for the other types of cargo pumps mentioned.
At present, over 20,000 twinscrew pumps are in service on board modern European coastal tankers and barges.
What is generally not well known is that over 5,000 twin-screw cargo pumps are installed in Europe in land-based tanker off-loading terminals to serve river barges not equipped with their own cargo unloading pumps. These pumps are often driven by reversible rotation drivers and fitted with special piping so they can be used for both loading and unloading.
Many tankers and barges are equipped with independent main suctions and separate cargo stripping lines of smaller nominal diameters.
In those cases, it is possible to switch twin-screw cargo pumps from the main lines to the cargo stripping lines and continue stripping the cargo tanks with the main cargo pumps. In essence, the main cargo pumps can be used as highcapacity strippers.
In the case of moderate-size tankers (about 50,000 dwt), when fitted with twin-screw cargo pumps, only three or four twin-screw cargo pumps are recommended per ship set. This excludes independent cargo stripping pumps but retains independent cargo stripping lines of smaller diameter, which are required for future tank cleaning services by the main cargo pumps.
Twin-screw cargo pumps can be driven by electric motors, diesel engines, steam turbines, gas turbines, turbo generators, hydraulic motors, PTOs from main engines or gear boxes.
They are preferably operated at speeds ranging from 1,000-2,000 rpm. Thus, shipboard 60 Hz AC power supply is suitable to operate electric motor-driven twin-screw pumps at 1,150- or 1,750-rpm speeds.In all cases, it is always recommended to provide amble driver bhp so in the event of lost cargo heating, when liquid viscosity and absorbed pump bhp gradually increase, adequate horsepower is still available In practice, cargo pump drivers are installed in the engine room or on the main deck in a deckhouse.
The pumps, either in a pump room or submerged in a cargo tank-well, are driven by jack shafts or cardan shafts via the bulkhead or engine room flats. The drive shafts are sealed by gas-tight, self-aligning bulkhead stuffing boxes. It is not essential to place twin-screw pump suctions close to the ship's bottom, i.e., inside a pump room. It is, however, still good engineering practice to locate cargo pump suctions as low as possible in a pump room or cargo tank suction well so the main pumps can be used for tank cleaning and cargo stripping.
Twin-screw pumps can also be installed directly into a cargo tank.
There may also be a choice between single- or two-speed motors, if so desired. Deck space required for these arrangements are minimal.
For the transportation of heavy viscous crudes, Exxon Corp. installed aboard several existing 40- 51,000-dwt steam tankers three to four horizontal twin-screw cargo pumps per ship set to replace centrifugal cargo pumps. The new units have a cargo discharge capacity of 5,000 gpm each, at 1,200 rpm pump speed driven by 1,000-hp geared steam turbines capable of speeds from 250 to 1,200 rpm. All units were retrofitted by a major East Coast shipyard in 1980/81. The large twin-screw pumps are also used to strip the cargo tanks dry at low pump speeds and eliminated the need for special self-priming air pumps. The cargo pumps were installed at the lowest possible level in the main pump room aft. By request of the shipowner, the ships were refurbished with vertical positive displacement cargo stripping pumps. The independent cargo stripping pumps serve a separate cargo stripping piping system for cargo tank cleaning.
Some U.S.-flag shipowners have been looking for main cargo oil pumps suitable for handling an ever-increasing range of cargo products— from the lightest to the heaviest viscosities. Others are inter- ested in handling crude oils only, but with viscosities up to 35,000 SSU (7,600 est) at low temperatures.
Others still ask for pumps capable of handling alternately such cargoes as bitumen, asphalts, tar, bunker C, fuel oil, heating oil, marine diesels, benzene, benzol, solvents, molasses, caustics, alkalies, and fresh or seawater.
In this regard, it must be admitted that the existence of a "universal" tanker is not foreseen in the very near future. Nonetheless, interested shipowners ought to remember that the existing twin-screw cargo pumps have successfully demonstrated their unsurpassed capability in handling all of the aforementioned cargo products. They have also proven themselves aboard an offshore storage and treatment vessel, located on the U.S. West Coast, since 1981.
Circle 96 on Reader Service Card
Read Modern Cargo Pumps For Tankers And Barges in Pdf, Flash or Html5 edition of November 1988 Maritime Reporter
Other stories from November 1988 issue
Content
- Program For U.S. Shipyard Revitalization Proposed page: 5
- $135-Million Luxury Cruise Vessel Ordered From Wartsila Marine By Finnish Shipowner Birka Line page: 6
- Newport News Announces Management Restructuring page: 7
- Moss Point Marine Completes Four-Ship U.S. Army Contract page: 8
- Joint Venture Formed To Build, Operate Passenger Submarines page: 8
- Anders Wilhelmsen Buys Royal Admiral page: 9
- Gladding-Hearn, LQMoffitt Develop Bearing Flange Design Solution page: 9
- Shrimper/Crabber Built By Mid-Coast Marine page: 10
- Omnithruster Waterjets Offer Maneuverability In Polar Regions page: 11
- World Orderbook Highest In Two Years page: 14
- Westmont Receives $24-Million Contract For Five Floating Cranes page: 14
- Colonna's Shipyard Elects Owen VP And GM page: 14
- Bender Delivers Two Factory Ships—Receives Contracts For Two More page: 15
- MMC International Announces New Tape And Valve Catalog page: 15
- Cargo Ship To Undergo $19.8-Million Conversion At Bay Shipbuilding page: 15
- McDermott International Forms Executive Operating Committee page: 16
- Nichols Bros. Wins $8-Million Contract To Build Six Ferries page: 16
- Non-Ferrous Offers Free Literature On Full Range Of Fasteners page: 17
- Falk Brochure Details Concentric Shaft Reducers page: 17
- SNAME 95th Annual Meeting and 7th International Maritime Exposition page: 20
- Mobile Telesystems Begins Operations page: 46
- New 42-Page Catalog On Flanged Ball Valve From Jamesbury page: 46
- Exxon Offers Exxcare— A Cost-Cutting Computerized Solution To Maintaining/Monitoring Oil page: 48
- Crandall Railway System Again Proves Its Versatility/Dependability page: 49
- Marine Travelift Brochure Describes Benefits Of BFM Mobile Boat Hoist Design page: 49
- Warren Screw Pump Meets High Viscosity Demands page: 50
- Nalfleet, Bull And Roberts Introduces New Approach To Water Treatment page: 52
- SPD Technologies Expands Through New Acquisitions And Product Development page: 56
- CALS Conference Slated For December 8 At USMMA-Kings Point page: 58
- Free Butterworth Brochure Details Types K/Super K Tank Cleaning Machines page: 58
- TBT-Containing Antifouling Paints —The Legislative Position— page: 59
- AT LAST, A GOVERNMENT PROGRAM THAT CAN BENEFIT ALL Implication of CALS to Industry page: 60
- OUTSTANDING WORKBOATS OF 1988 page: 62
- MAN B&W Engines Continue To Make Impact page: 71
- Gladding-Hearn Announces Sale Of Its Fourth INCAT To New York City Ferry Service page: 72
- Volvo Penta Engines Stipulated For Each Of Two 'Hybrid' Ships page: 72
- Port Of Iberia Acquires 70 Adjoining Acres In Master Development Plan page: 73
- Employee Buyout Helps Seattle Yard Emerge From Bankruptcy page: 74
- Hempel's Reports Good Response To New Cargo Barriers Coatings page: 74
- Stauff-Test Pressure Check System Developed By Stauff Corporation page: 75
- Safety Lifting Clamps For Plate And Structural Steel Featured In New Brochure page: 76
- Kiene Diesel Accessories' New Injector Puller Saves Time And Money page: 77
- New ARQ Radio Telex Station Offered By Hull page: 78
- Schroder Offers Six-Pcige Color Brochure On Marine Propulsion Control Systems page: 78
- Krupp MaK Wins $21.6-Million Retrofit Contract For Canadian Icebreaker page: 79
- Navy Approves PPG Coating To Stop Cable Fires page: 79
- Modern Cargo Pumps For Tankers And Barges page: 80
- Furuno Introduces High-Power FR-1500D Series Radar page: 82
- Acurex Introduces 'AutoNet'—Its Latest Portable Software System page: 82
- 75-Page Book On How To Survive Abandoning Ship Offered By Viking page: 83
- Tidewater Marine Adds Five M a r A d Vessels To Worldwide Fleet page: 84
- MAN B&W Diesel Introduces Two More Large Bore Engines page: 85
- Cospolich Develops Refrigerators With Extraordinary Capability page: 86
- New Rules To Mandate Sealing Of Barges page: 87
- Brochures From Hagglunds Describe Computerized Cargo Handling Systems page: 89
- Nichols To Build Advanced Technology 'Wave Piercer' For Fast Passenger Service page: 90
- Custom, Design-lt-Yourself Continuous Liquid Level Indicators Introduced By Gems page: 90
- Complicated RO/RO Conversions Completed By Danyard A /S page: 91
- B&W To Build 84,000-Dwt Products Carrier page: 91
- Bird-Johnson Names Vaughn Seattle Operation's Marketing And Sales Manager page: 93
- Harris SSB Radio Has Noise Blanker page: 94
- Sulzer-Powered French Containership Is Designed For Minimum Crewing page: 94
- Advanced Fiber Technology From Allied-Signal Division Improves Marine Rope Performance page: 99
- 'Space-Age' Simulator Program At MarineSafety Prepares Officers To Handle Super Containerships page: 106
- Munson Introduces Fast, Low-Wake Boat Designed For Harbor Commuter Routes page: 106
- AESA To Build Three More Reefers For Del Monte page: 107