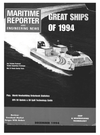
Page 17: of Maritime Reporter Magazine (December 1994)
Read this page in Pdf, Flash or Html5 edition of December 1994 Maritime Reporter Magazine
Welding Technique Helps
Navy Save Millions
When maintenance welding re- quired cutting into the hull of a
Navy submarine, John Bartly knew there had to be an easier way.
Mr. Bartly supervises 15 weld- ing engineers as a U.S. Navy em- ployee on Mare Island in San Fran- cisco Bay. A former president of the American Welding Society, he has decades of experience.
He and his engineers approached
Hobart Lasers & Advanced Sys- tems in May 1990 (formerly Martek) to create a multi-faceted program which would meet several welding challenges he faced in his assign- ment to repair Navy submarines and other seagoing vessels.
To date, Hobart has evaluated equipment, developed accessories and conducted feasibility studies on a number of innovative processes for the Navy. Hobart's Application
Development Centers provide an opportunity to test applications on state-of-the-art CW Nd: YAG la- sers; Orbitig control systems; Viper tube-to-tube welding heads;
HAWCS computer-controlled vari- able polarity plasma/gas tungsten arc systems; and other equipment.
A challenge Mr. Bartly faced was the repair of deteriorated valve seats on the steam chest, which contains control valves to throttle the submarine's steam flow. Con- ventional welding processes in these applications are low yield and must be repaired several times. The low power density process required
Mr. Bartly's welders to cut through the pressure hull of the sub, remove the item to be repaired, take it to the shop, preheat it, manually re- pair the item, post-weld heat it, machine it, return it to its original position, and repair the opened pres- sure hull. To cut down on this process, saving time and money,
Hobart's engineers found that by using laser technology they could perform the repairs without having to remove the component, as the preheat and post heat are not re- quired. "Because it has a 150-ft. (45.7-m) fiber optic delivery sys- tem, our 2,400-watt CW Nd:YAG laser welding head can be brought internal to the vessel and locally tooled with accessories, potentially saving millions of taxpayer dollars," said Tim Webber, a Hobart Laser
Applications manager.
In repairing the steam chests, old material must be machined off and replaced to a precise finish, size and polish. Currently, Hobart is developing a system with a small articulated gantry robot, small enough to get in the operator's lap.
Using rotary motion, the robot welds a hardface alloy place from a small mechanical bridge. A pendant-like controller is used by the operator at the welding site to set up param- eters as necessary. The laser gen- erating equipment sits outside the vessel.
For more information on Hobart Lasers & Advanced Systems
Circle 103 on Reader Service Card
December, 1994
Avondale Awards Mapeco
Contract For Keyless
Hydraulic Shaft Couplings
Mapeco Products, a divsionofWalz & Krenzer, Inc., was awarded a con- tract from Avondale's shipyard
Divsion for eight keyless hydraulic shaft couplings for the first ship of its Sealift new construction program.
They will reportedly be the largest keyless shaft couplings to be made in the U.S. m date.
Mapeco has previously supplied couplings for the T-AGS 45 and LSV- 21. In addition to the couplings.
Mapeco is also supplying Pilgrim
Radial Fit Bolts to be used in con- junction with the flanged keyless cou die popular in Europe, this is reportedly the first U.S. marine ap-
Iication for the Pilgrim Radial Fit olts.
For more information on Mapeco
Circle 22 on Reader Service Card • IK I m" - -
REPAIR QVQTFM nErftln aiOICIYI
WORLD LOCATIONS
LOS ANGELES
Using SIFCO Process technology and our selective electroplating system, you can perform many repairs in-place. The SIFCO
Process selectively plates localized areas without using an immersion tank. In addi- tion to providing corrosion resistant coat- ings, you can repair: • Pinion gear shafts 'Impeller bores • Propeller shafts • Valve stems • Cylinder liner seats • Slip rings • Shaft couplings "Reduction gear boxes ...and many other components that require metal build up or defect repair — all with a portable, compact system with minimal environmental concerns.
Purchase the system — we install and train — or let us provide contract services.
HARTFORD
NORFOLK
FT. LAUDERDALE
REDDITCH, UK
PARIS
SINGAPORE
TOKYO
SEOUL
SIFCO
SELECTIVE PLATING 5708 SCHAAF ROAD
CLEVELAND, OH 44131
PH: 216/524-0099
FAX: 216/524-6331
ABS # 93-QE-10247-X
Circle 264 on Reader Service Card
Bite Through RUST,
SCALE 8 PAINT ' - „. //
There is an AURAND tool that's right for EVERY job!
I Aurand's patented cutting teeth bite right through tough accumulations on ANY hard I surface. On decks, walls, or ship hulls, in tanks, pipelines or boilers, results like 1 sandblasting are yours. Aurand's unique Centrifi-Clean® action quickly peels off build-up.
Adjustable depth settings protect the underlying surface and prevent overloading, stalling | | and excessive cutter wear. • LIGHTWEIGHT • ADJUSTABLE DEPTH SETTINGS • EASY TO USE • SAVES HOURS OF WORK
Accepted 1210 ELUS STREET • CINCINNATI, OHIO 45223-1843
MADE IN
USA
PHONE: (513)541-7200
FAX: (513) 541-3065
TOLL FREE: 1-800-860-2872
Circle 204 on Reader Service Card
SWAN ^HUNTER
ONE OF THE
MOST FAMOUS
SHIPYARDS
IN THE WORLD
For sale on the instructions of the joint administrative receivers
A. M.Homan FCA,G. C.Horsfield FCA and A.E.James FC«.
The Wallsend Shipyard: birthplace of such famous ships as SS Mauretania,
HMS Ark Royal and Atlantic Conveyor. • The Swan Hunter name • 39.5 acres (16 ha) site • 4 slipways • 560 metres river frontage • Substantial engineering and fabrication facilities • Extensive plant and machinery • Deep water berth (8 metres below chart datum) • North East England - River Tyne • Close to Newcastle upon Tyne • Excellent access to European market • Craneage includes 2 of 180 tons iy Sanderson ® Townend & Gilbert £ V CHARTERED SURVEYORS
Contact Robert Patterson
NEWCASTLE
Tel: +44 (0)191 261 2681
Fax: +44 (0)191 261 4761 1 'HENRY BUTCHER
Contact Richard Corby
LEEDS
Tel: +44 (0)113 245 7356
Fax: +44 (0)113 246 7364
Circle 267 on Reader Service Card 42A