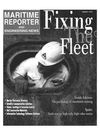
Page 43: of Maritime Reporter Magazine (March 1999)
Read this page in Pdf, Flash or Html5 edition of March 1999 Maritime Reporter Magazine
The Great Lakes ore carrier Herbert C.
Jackson suffered severe damage — four ft. cracks — to its propeller hub. The hub was restored to original specifications using metal stitching. rejuvenate a more than 90 year old
Great Lakes cement carrier. The ship is powered by a 3,000 hp Skinner Uniflow steam engine, one of just two Great
Lakes vessels still operating with this type of power plant. On a return trip from Chicago, the Medusa Challenger developed cracks in the lower heads.
Back in its homeport of Milwaukee, the owners chose to weld the damaged areas. This weld would be no easy task due to the depth of the cracks. Prior to welding, the repairmen ground out the cracks in the shape of a "V", and then filled in the area with weld. The day and night repairs took place on board over 13 days. While welding took place below deck, the entire crew remained busy with painting and general mainte- nance.
The hard work failed to pay off. Once the ship left port, the welds proved unable to hold up to the stresses of oper- ation. Having heard of metal stitching, the owners decided to try the process.
The additional work consisted of drilling a series of holes at right angles to the cracks and then filling the cracks with rods made of a special alloy. In just six days the repairs were completed and the Challenger departed.
Unlike standard welding procedures, the metal stitches held up to the demands of the ship.
Another benefit of the process is the stitch distributes torsional loads away from fatigue points. Precision dimen- sions on the repair parts are tightly held as they are cold repaired — no heat is required. Stitching is permanent, as the repair is stronger than the original metal.
March, 1999
Hub No Match for Crushing Ice
For the Herbert C. Jackson, a Great
Lakes ore carrier, battling the severe shocks of ice-bound water had resulted in 80 in. cracks into the 4-sq. ft. pro- peller blade hub.
Five days of metal stitching and $25,000 brought the hub back into ser- vice. This type of repair for a hub secur- ing 7 ft. blades had reportedly never been attempted before. Estimates for replacing the heat-fitted hub ran to $250,000 and nearly six months of work.
As proof of the strength of the repair, the Herbert C. Jackson set out to
Cleveland in early spring two years after the repair. This time the ice sheared off the propeller blades. After ballasting the tanks to start the repairs, an inspection revealed the hub was as good as new.
Metal Surgery went on to replace the blades.
Circle 97 on Reader Service Card 600 PASSENGER DINNER-CASINO SHIP • Our Shipyard can * 40 years knowledge custom build a vessel Utffw If & experience designing to your specifications. f v and building to USCG, • Full engineering capabilities. ABS, SOLAS 2010, • Skilled-dedicated craftsmanship. US Public Health - with full • Competitive Pricing. certificates ready for service.
COMPUTE CONSTRUCTION PUNS FOR OVER 280 VESSELS
BIOUNT'S 50TH YEAR
BLOUNT INDUSTRIES, INC. 461 Water Street, P.O. Box 368, Warren, RI02885 (401)245-8300 Fax:(401)245-8303
Circle 209 on Reader Service Card
Stainless Steel Acid Proof
Centrifugal Pumps
Electric or Hydraulic Driven
HIGH PRESSURE PUMPS • Fire • Deck Wash • Circulation • Thawing
LOW PRESSURE PUMPS • Cooling Water • Ballast • Bilge • Circulation
DIESEL DRIVEN
EMERGENCY PUMPS •E.P.G
MARINE EL£CTRICAl » PROCESS COWTROL
P0 Box 70648, 3931 Leary Way N.W.
Seattle, WA 98107
Tel: 206-545-2209 • Fax: 206-545-2819
Email: [email protected]
Service and Build Electrical Starters and Control Systems
Construct Electrical Panels
Distributor of Electrical Metric Frame Motors
Distributor of Stainless Steel Centrifugal Pumps
B I
When Space, Weight, or Cost is a Problem,
Technology Takes Over!
You can take a large amount of bridge control and monitoring functions and shrink them down to 81* x 11 inch sheets of technology, solving the space problem associated with bridge design.
It also lets you take advantage of an ABS, USCG approved data buss that eliminates the cable runs to the bridge while still controlling and monitoring all systems assigned.
The process is as easy as faxing us an 8l'a x 11 inch sheet of control and monitoring items and we will provide a return fax of a panel design which does it all in a fraction of the space, weight, cable and labor associated with the traditional method. Two wires to the panel shown does it all. s
ELECTRONIC MARINE
SYSTEMS, INC. 800 Ferndale Place
Rahway, NJ 07065
Call today for more information! 732.382.4344 732.388.5111 fax [email protected] e-mail http://www.emsmarcon.com
Circle 225 on Reader Service Card
Circle 261 on Reader Service Card 43