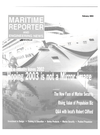
A Proven, New Approach for Vessel Insulation
Special Advertising Section for Mascoat Products • www.deltacoat.com Vessel insulation has changed very little in many years. Normally hidden from direct view, thermal insulation systems can become ineffective over time due to poor installation, vibration or moisture intrusion. In fact, if moisture is ever introduced into the insulation from a leak, poor installation, or inadequate repair job, the conventional insulation methods are worse than if insulation had not been used at all.
Common Methods of Thermal Insulation Inside Vessels In the past, most shipyards and owners have been at the mercy of technology that only incorporates one aspect of heat/cold transfer known as conduction. These insulation systems have been designed to retard heat and cold over time and treat & solve heat transfer as a symptom, not as the inherit problem.
Common pin-and-blanket insulation found on most vessels requires the painstaking task of bringing the insulation material into an area, placement of attachment pins, cutting, tapping and finally fitting of the insulation.
With this multi-step process, which is quite labor intensive, only around ten square feet (one square meter) of insulation can be installed in a one-man hour time period. If not managed well, this process could lead to dramatic man-hour cost overruns. In addition, over time these blanket insulation systems lose their power to retard heat/cold and therefore are a direct gate for thermal transfer into the vessel.
Another common way of insulating vessels is to use foam-in-place insulation systems.
This system requires special equipment, highly trained personnel and usually complete shut down of other ongoing tasks of a job during an application due to safety and PPE (personnel protection equipment) concerns.
Since foam systems work on chemical reactions of component products that are highly flammable, these systems do not pass the current FTP codes and can in fact contribute to the dangers and damage caused by fire. Just recently, there have been two incidents of fires onboard crew vessels where foam insulation contributed to death.
Other problems of these foam systems include, outsourcing of personnel for an application, bonding and detachment issues, degradation of the insulation due to vibration, and most importantly corrosion under insulation. Though this is a cheaper method of insulating, foam systems have been highly scrutinized as an antiquated technology.
A New Approach to Thermal Insulation and Protection of Vessels In 1995, Mascoat Products, Houston, Texas, developed a new spray application thermal barrier system, Delta T Marine Insulating Coating, which has been successfully used worldwide on more than 200 vessels.
The system is a water-based acrylic binder that encapsulates air-filled ceramic insulating particles to help reduce or eliminate most radiant heat/cold transmission.
Delta T Marine is sprayed on the inside shell of most modern vessels at a thickness of 20- 60 mils (0.5-1.5mm). By direct bonding, a substrate becomes thoroughly protected and eliminates the potential of development for Corrosion Under Insulation. Vessels employing the coating system are now insulated and protected with a thermal transfer rating of RvE 9-13 factor when compared with conventional insulation. Thus, this spray system used alone or in conjunction with conventional wallboard provides equal or better protection of thermal transfer at a reduced cost and time effort.
Most shipyards that have used the Delta T Marine find that application is quick to learn as well as easy to apply. Normally sprayed with an airless sprayer, Delta T applies much like thick consistency paint. With little training, the existing paint crew of a shipyard can be taught to spray the coating efficiently. This allows shipyards to control insulation with existing paint crews thereby reducing the outsourcing need in most circumstances. Crews can average 1000 sq. feet (100 sq. m.)/hr.
This equates to a substantial man-hour savings and a fantastic way to trim or maintain man-hour costs.
Although the material price is somewhat higher for Delta T Marine, total installation costs after labor are dramatically reduced.
Additional benefits include escalation in the time frame of the vessel and ease of repair if change orders require additional fabrication.
Most yards see up to 50-80 percent time frame escalation and 30-45 percent reduction on total installed costs.
How can a coating replace 3-in. of conventional insulation? This is a common question that arises. According to George More, president of Mascoat Products, "Insulation has changed very little for many years. Most thermal blanket and foam insulation systems use only the principle of conduction as a sole blocking agent of heat transfer. This means using only one of five methods that reduce thermal transfer. Our system uses all basic principles of thermal dynamics to our advantage.
Our coating deals with heat or cold before it enters or penetrates typical vessel insulation. This allows our system to work more efficiently and keep thickness to a minimum.
More importantly, our system will not degrade due to vibration or moisture intrusion and is not flammable like foam systems are." Basically the coating works because Delta T Coating employs its highly reflective white surface and ceramic composition structure to reflect heat away from the substrate and back to the atmosphere. Imagine a Thermos® bottle. The coating is very similar in this respect. The coating actually reflects upward of 85 percent of the heat /cold generated back to the respective substrate or atmosphere.
Its hollow, microscopic glass and silica airfilled beads provide an excellent "k "or conductivity factor by dissipating the heat over the entire surface hindering the conductive process. This means there is no hotspot or vertical heat pipe effect like conventional insulation. (The vertical heat pipe effect is the way in which conventional insulation passes heat via free air convection through the insulation vertically. This heat is then transferred to the overhead deck area. Temperature increases can be as much as 5°C or around 25°F.) Also Delta T Coatings' unusually low emittance allows little heat to be re-radiated into the atmosphere starting a convective process.
The coating also employs other heat blocking agents of absorptance and transmittance, increasing its insulating factor. By adding up the conduction, reflection, emmisivity, transmittance and absorptance properties of Delta T Marine coating, all aspects of thermal transfer can be employed in one product.
Another beneficial aspect of the product includes its sound deadening characteristics and weight savings. Delta T Marine applied inside a vessels shell drops air borne structural noise 50-80 percent depending on thicknesses and substrate. Its lightweight composite bead structure equates to 0.07 lbs. / sq. ft.
applied as opposed to 0.51b-1.51bs sq. ft. for conventional systems. This is very important in yacht and ferry construction where sound and weight materials are highly scrutinized.
New Series of Products Just recently, Mascoat Products has introduced its second-generation series of products.
This new series employs advanced chemistry techniques to make the coating more paint-like as well as expanding the coating's insulation abilities. This allows for increased square footage per gallon and an increase in thermal efficiency.
Classifications Delta T Marine has passed rigorous testing and is classified in accordance with IMO/SOLAS guidelines. This product is certified by U.S.C.G., A.B.S., D.N.V., and Lloyd's (MCA) to the new FTP Codes. The product is packaged in one (4 liters), five (18.9 liters), and fifty-five gallon containers and is sold factory direct to the shipyard or owner or through various distributors.
For further information, contact: Sales Department, Mascoat Products, 10890 Alcott Drive, Building # 102, Houston, Texas 77043, tel:(713)465-0304, or log on to www.deltacoat.com.
Circle 199 on Reader Service Card
Other stories from February 2003 issue
Content
- The USCG, MTSA '02 and IMO - The New Faces of Security page: 8
- Littoral Combat Ship Takes One Step Closer to Reality page: 10
- Secure Marine Transportation... Priceless? page: 12
- Three PacifiCat-class Fast Ferries to be Sold page: 18
- The Rising Value of Propulsion Business page: 19
- Navigator of the Seas—A New Course for Profitability page: 24
- Plug and Play page: 28
- Cruise Ship Design Trends Mirror Marine Marketplace page: 31
- Deltamarin Expands to China to Thwart Cruise Downturn page: 34
- Gotar: Keeping Ships Clean From the Inside page: 35
- Coral Princess Debuts With Unique Propulsion System page: 35
- Sick Ships, Project America and a Merger page: 36
- A 360 O page: 38
- Swimmin' With the Fishes STN Atlas, WirtsilS Propulsion "Dolphin" Pod Proves Popular page: 38
- M/S Zuiderdam: Modern With Elegant Taste page: 40
- Construction on 10-Boat, $57-M Contract Commences for Brazil page: 44
- INCAT — A Delicate Balance for the Future page: 46
- NCL Debuts Newest Star with NYC Flair page: 48
- Damen Delivers High Level of Tug Tech page: 49
- A Proven, New Approach for Vessel Insulation page: 50
- The Dilemma: Competent Crews vs. Costs page: 54
- Blue Ridge Officers Complete Safety Training page: 57
- Shipping 2003: Don't Stop Thinking About Tomorrow page: 58
- Cruise Industry Gathers in Miami page: 61