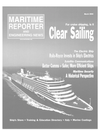
Training the Trainer to Keep Knowledge Afloat
Northrop Grumman Newport News Shipbuilding invests to maintain its skilled workforce.
Shipbuilding, like other industries that rely on a skilled workforce, faces a serious problem: an alarming "knowledge loss" in the area of specialized machining. Not only are many workers with machining expertise reaching retirement age, but fewer people are entering the machine trade. There's also the cyclical nature of shipbuilding which adds to the problem: use of a specific piece of equipment or a particular skill might occur only once every three or four years in the process of constructing a submarine or carrier. In the interim, these skill workers retire, are promoted or otherwise change jobs. Gradually, the ability to use a piece of equipment can be lost.
Northrop Grumman Newport News, a shipbuilding customer of Climax Portable Machine Tools, recognized a dwindling level of expertise among its workers in the use of our portable boring bar equipment in the construction of submarines and carriers. Northrop Grumman Newport News is the nation's sole designer, builder and refueler of nuclear-powered aircraft carriers and one of only two companies capable of designing and building nuclear-powered submarines. Like many companies, Newport News realized that unless its skilled machinists improved and shared their knowledge, skills could very well be permanently lost.
The Time has Come to Train the Trainer Ed Elliott, General Foreman in the Trades Management Division at Newport News, recognized the need to address his company's knowledge loss in the area of portable machine tools, and together with Robert Downing, initiated a training program for Newport News in 2002. Downing, who at the time functioned as Senior Operations Coordinator, discovered a lack of internal expertise in boring techniques, especially using portable tools that many workers hadn't been exposed to. He turned to Climax to help coordinate a training program.
"By bringing in experts," said Downing, "we were able to cost-effectively begin a program aimed at educating a select group of people not just on the latest boring techniques, but on how to effectively train others." The five-day program — one day in the classroom and four days in the shop — focused primarily on the use of two Climax machines, the 2-in. BB5000 boring bar. and the 3-in. BB6000.
In the classroom. PowerPoint presentations covered equipment safety, as well as machine tool applications, operational techniques and maintenance. "At Newport News, we take safety as our number one priority and what impressed me is Climax does too," said Elliott.
"We covered the proper way to handle the equipment and the potential dangers - how things like loose clothing, poor lighting, improper ventilation and inadequate eye and ear protection represent potential dangers." Enhanced productivity was stressed, too, and demonstrated with hands-on training during the four-day in-shop portion of the program. New, time-saving boring techniques were covered, as well as innovative machine tool applications and maintenance recommendations to extend tool lifetime. "It's the kind of information that a lot of organizations don't share," said Elliott.
"Most just sell you a piece of equipment, and you have to figure it out for yourself." After learning how to set up, operate, and become familiar with all functions of the machines, trainees were required to undergo skills assessment and tested on the information they'd learned.
The original five people who attended the initial training course have been joined by two other instructors, and have to date succeeded in training 16 others.
Ultimately, as many as 40 workers will be trained, reinforcing Newport News' work force and enabling the company to stay on the cutting edge of portable machine equipment, processes and tooling. Since training took place on-site, travel expenses were minimized and the number of participants maximized. Ed Elliott also anticipates an additional payoff in terms of machine tool usage. "As we've train our young mechanics, we discover that they're extremely creative.
They'll look at a job and find a totally new application for the boring bar and more and more uses for it on the ship, which is what we were hoping for. I doubt that our BB5000s and BB6000s are going to sit on the shelves the way some specialized tools usually do." Elliott sums up the training experience this way.
"Climax did a good job training our people, and I think our people are doing an outstanding job passing what they've learned along. The whole concept really worked out well — we're all becoming much more knowledgeable." Circle 6 on Reader Service Card Jim Miller is a senior applications engineer for the shipbuilding systems group of Climax Portable Machine Tools. He has more than 18 years experience with Climax and is a specialist in the area of solving on-site machining needs of the shipbuilding industry. He served four years with the U.S. Navy as Submarine Tender Machinist servicing the U.S. Naval Fleet in both the Pacific and Atlantic arenas.
Other stories from March 2004 issue
Content
- Bollinger Delivers Tidewater Supply Boat Jonathan Rozier page: 8
- World's Largest Dry Transport Vessel Delivered page: 10
- Port security: A Historical Perspective page: 12
- Delayed Enforcement of Change to "Shipper" Element page: 16
- MTSA: Another Key Layer of Port Security page: 17
- When Security is Made Simple page: 20
- Business Milestone for Vietnam page: 24
- "Made in Germany1 — a New High page: 24
- Miracle on Ice page: 26
- New President & CEO at Kvaerner Masa-Yards page: 28
- He's No Regular Joe page: 30
- Cruise Passenger Travel Grows 8 Percent; New York and Galveston Post Big Gains page: 32
- HAL's Vista Sails with ROCHEM Technology page: 33
- Royal Caribbean Takes Mariner of the Seas page: 34
- NorseMerchant Ferries Plans Service Upgrade page: 37
- Grimaldi Continues Fast Track Expansion page: 38
- Costa Places $450m Order With Fincantieri page: 40
- Losing ontact... Not an Option page: 44
- Ship Security Alert Systems (SSAS) page: 50
- GALILEO Lifts Off page: 52
- Icebreaker Uses Satellite to Break Through Communications Barriers page: 55
- Cellular Fixed Wireless Helps Deliver Mercy page: 57
- Homing in on Ships' Electrics page: 58
- Shipconstructor Chosen as Standard page: 61
- Contract for New Product Tanker Design page: 62
- BollFilter: 50 Years of Success and Counting page: 65
- The Corrosion Control Challenge page: 66
- Nippon Paint Restructures page: 69
- Metal Fusion Helps Stop Corrosion page: 69
- Maritime Security Professional Training page: 72
- Training the Trainer to Keep Knowledge Afloat page: 74