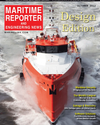
Safety: A Shift in Culture
“A quality safety culture means doing things safely even when no one is looking”
“Safety Culture” is one of those terms that is used a lot in the maritime industry. We all think it is important, and every operator wants a “good” safety culture. But how does one get it, and then keep it once it is there? This is the first of a pair of articles looking at safety culture in the maritime industry.
What is Safety Culture?
The IMO tells us “An organization with a ‘safety culture’ is one that gives appropriate priority to safety ... The key to achieving that safety culture is in:
● Recognizing that accidents are preventable through following correct procedure and established best practice,
● Constantly thinking about safety; and
● Seeking continuous improvement.”
This is a fair, but arguably limited description. Safety culture is not something that a vessel operator either has or does not have. All operators have a company culture, and their culture (whatever form it takes) impacts safety of operations. All aspects of a company’s culture are related. It is very difficult, if not impossible, to have an excellent and effective safety culture but a poor culture (for example) in terms of workplace cleanliness, employee communication or employee engagement. The question therefore is whether the company culture enables, promotes and rewards safe acts.
Safety Culture Basics
The necessary components of a quality safety culture include the following.
• Management Leadership
It is generally agreed that safety must start at the top. In fact, some organizational culture experts go so far as to say that “... the only real thing of importance that leaders do is to create and manage culture” (Organizational Culture and Leadership, Schien, 2004). Management must view safety as a long-term investment in their company, not a cost. It is their role to consistently and visibly inspire and enable a culture of safety. It is also their role to be safety culture champions, to identify other champions, and to steward the process of cultural transformation. This usually means going well beyond compliance and always means considering safety as a part of all decisions while allocating sufficient resources to safety considerations. Building an effective safety culture is not a switch that can be “turned on,” but rather a sea change, or broad transformation that takes time to nurture. It takes time to implement the necessary changes, and even more time for employees to be convinced that this is a real, lasting change and not a fad soon to be abandoned. This management commitment takes real effort, but pays incredible dividends. Without strong, consistent and long-term leadership from the top, it is not possible to improve the quality of an organization’s safety culture.
• Training
Clearly, safe operations require that all operational personnel are competent, understand and are skilled in safe procedures, and are aware of potential hazards AND how to avoid them. This is the job of initial and ongoing training. Attention to training not only guarantees the above, but it also sends a strong message that management values safety and, consequently, values its employees. An employee who feels valued and values him or herself is one who will do the right thing - even when no one is looking.
Fortunately, we are in a time of great opportunity for implementation of new, effective and visible training programs. If training is not already top-notch at an organization then it can be made so using a breadth of new educational content and techniques. And while a large budget never hurts, it does not have to be expensive. Given the importance of training, the benefits of investing in it, and the visible nature of its effects, attention to training is almost universally considered to be a necessary component of safety culture transformation.
• Measurement and Continuous Improvement
As I have written several times in earlier articles, “If you don’t measure it, you can’t manage it”. A high quality safety culture is one that requires measurement of safety performance. It uses those measurements as markers (key performance indicators or KPIs) to inform a process of continuous improvement. Without a system of measurement there is no way to learn from mistakes, nor any way to celebrate or build on successes. Measurements (and ongoing communication of those measurements) are a key form of employee communication and a powerful demonstration of management leadership in the area of safety.
• A Focus on Learning, Not Blame
Every day there are “close calls” or “near misses” that represent incredible learning opportunities. An accident is a very expensive way to learn a lesson. A close call is a practically free way - but only if the close call is reported, analyzed, turned into a learning opportunity, and made public. The problem, of course, is that near-misses are almost never reported, especially in the absence of more than a few witnesses, because those at fault fear repercussions. The way around this problem is to have a policy ensuring that employees are not punished for an honest mistake or error in judgement resulting in an accident or near miss. At British Columbia Ferries Inc. (BC Ferries) this policy, as part of their huge cultural shift, has created an environment where an employee has no reason to conceal a near miss. This has yielded thousands of documented learning opportunities through their so-called “A.L.E.R.T” (All Learning Events Reported Today) incident reporting process. At the same time serious injuries have been reduced by two-thirds and continue to decrease. After speaking with front-line BC Ferries employees, it is fair to say that many view documenting their own near-misses as a point of pride; knowing the report will help avoid a future accident, injury or even fatality. The key to this success is that employees trust (highlighted because this is a very important word here) that the company is going to adhere to the “just” culture they have set up in terms of blame. This trust is powerful and takes time to build - but it is ultimately possible for any company.
• Continuous Reflection and Focus on Safety Culture
Although somewhat covered above, this is worthy of its own mention. Safety and safe procedures must always top of mind for the entire organization. This means measurement and continuous improvement, as well as a focus on learning - both mentioned above. But it also means highly visible, meaningful and continuous evidence of commitment.
One example that helps demonstrate company commitment to safety is regular visitation from top-level management (preferably the CEO) discussing the company’s actions around safety, providing evidence on safety KPIs and listening to feedback. I have seen the effect of this kind of top-to-bottom transparency at BC Ferries and it is nothing short of impressive. Other examples include employee safety focus groups, consistent safety messaging in the workplace, the celebration of “jobs done right” alongside the dissemination of near-miss information, and more. For safety to be top of mind, it must be continuously communicated and reflected upon in meaningful ways - and I stress the “meaningful” part of that. A sign on the wall reminding people of their role in safe operations will be respected if employees believe in management’s commitment to safety, but will be a sad joke otherwise.
Talking with the Expert
One person who has not only seen safety culture shifts, but has also been the architect of the same, is Captain John Wright of WrightWay Training Services in the U.K. He is a master mariner and the recent recipient of an IHS Safety at Sea training award. I had the very good fortune of meeting Captain Wright because of his involvement with the BC Ferries SailSafe project - a multi-phased project aimed at improving safety (and one that the company I work for, Marine Learning Systems, is fortunate and proud to be a part of). Under SailSafe, time loss injuries have been cut in half, serious injuries have been reduced by two-thirds, and annual insurance claims costs have been reduced by over three-quarters. This is possible for every vessel operator.
I recently interviewed Capt. Wright and asked him what was the secret to safety and loss avoidance. Here is what Capt. Wright had to say:
John: Put simply it’s real workforce involvement. It is necessary to close the ‘chasm’ that often exists between the front line workers and their managers and directors and create a ‘one team’ environment. This is achieved by running the business such that the health, safety and welfare of the employees are put first, second and last by the leadership team – genuinely and transparently. Inhabiting this morally invulnerable high ground satisfies the hugely important human need in the employees of being valued and listened to. When this trust is built there is absolutely nothing better an organisation can do to improve all aspects of its business.
Next month’s edition of Maritime Reporter and Engineering News will present the remainder of the interview with Capt. Wright looking at how an organization can establish a healthy and effective safety culture.
(As published in the October 2013 edition of Maritime Reporter & Engineering News - www.marinelink.com)
Read Safety: A Shift in Culture in Pdf, Flash or Html5 edition of October 2013 Maritime Reporter
Other stories from October 2013 issue
Content
- LeBeouf Celebrates Double Christening page: 10
- Sofware Solutions Picking up Steam page: 12
- Winn Willard: Bringing Venerable Designs Forward page: 14
- U.S. Defense Conducts Maritime Strike Ops page: 18
- Safety: A Shift in Culture page: 20
- Hidden Exposures Can Sink a Business page: 24
- MARIN Debuts Tug Simulators page: 26
- Blowing in the “Vind” page: 28
- Year of the C-Dragon page: 32
- Maersk & New Containership Economics 101 page: 34
- GOL SALVAGE Taking on the Global Giants page: 40
- Advancing Monitoring Requires Advanced Oversight page: 44
- The Netherlands: Maritime Nation Thrives Despite Downturn page: 47
- Anything but Standard: Damen Newbuild and Repair Group Targets Global Growth page: 48
- Barge Master Provides Stable Platform for Crane, Offshore Ops page: 50
- Offshore Logistics: Wilson, Sons Group & Brasco Offshore Logistics page: 54
- Subsea Vessels Poised for Increased Global Demand page: 56
- APL Saves $30M/Year through Hull Optimization page: 58
- Bore, NAPA & ClassNK Team for Energy Consumption Study page: 60
- Damen Quick Docking/Fuel Saving Package page: 69
- MTU Series 8000 Marine Engines page: 69
- Air Products Nitrogen Membrane Generator page: 69
- FloScan: ABS Certification for New Flowmeters page: 69
- Fitch Fuel Catalyst page: 69
- Portable Industrial Combustion Gas & Emissions Analyzer page: 69
- Survitec: PFD Innovations page: 69
- Fire Detection from Fireboy-Xintex page: 70
- Paint Gun Washers Maintenance Kit page: 70
- Videotel Launches New Ports and Pilots Catalogue page: 70
- Onboard Drinking Water: Martek Marine Advises page: 70
- Bestobell FLIV for LNG Carrier page: 70
- New Diesel Welder/Generators page: 70
- Clean Marine’s EGCS First to Operate Inside ECA page: 70
- Victaulic Unveils Press-To-Connect Pipe-Joining System page: 71
- ExxonMobil Environmentally Acceptable Lubricants page: 71
- MTNW Debuts LCI-90i-IS page: 71
- Rolls-Royce Gas Turbine for Combat Ship page: 71
- Home Study For Mariners page: 71
- Anti Corrosion Technology Clam page: 71
- New Engine and Steering Solution page: 71