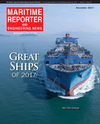
Driver-less Ships: Autonomy in the Maritime Sector
By William Stoichevski
In a show of prototypes, a pod of unmanned sailboats from around the world competes to cross “The Atlantic” test tank in Horten, Norway. Cross the real ocean, and the Sail Bots race similarly challenges scholarly robotic-vessel designers to North America for a bit of station-keeping, collision-avoidance and “cargo moves”. For all, the future seems bright — the first commercial runs of unmanned vessels are underway or scheduled worldwide. These earliest movers have the support of governments, Google and grateful clients.
Further ahead than most is Trondheim-based Maritime Robotics, builder of unmanned surface vessels, or USVs. Their designs already represent business streams: the 6 feet by 3 ft. catamaran Otter is tipped to be “mass produced” for fish-farm operations; the Mariner is available for offshore survey and supply. Both vessels are in-field, data-acquisition “platforms” that save money by replacing vastly more expensive options like crews and six-figure day rates. A Maritime Robotics deal with Seabed Geosolutions introduced the first USV for infield seismic surveys, where typically gigantic vessels might represent too much “risk”. Other, science-based clients have needed water-analysis, wind, inspection or survey work.
The larger Mariner — an enclosed RIB-like vessel built locally — can acquire data for military, science or commercial purposes and is already on two-year seismic survey contract for Seabed Geosolutions. The Mariner started with a pilot project in 2011 that produced a commercial hit for the Mariner two years into development and before trials were over. “In the beginning, it was doing special cargo transport between offshore supply vessels,” said Erik Hovstein, COO, on the phone from Trondheim. “Certain smaller cargo transfers couldn’t be done at night, normally, due to (safety concerns). That was the start for us in 2011.”
Hovstein quickly found applications for their USVs in other markets, especially as unmanned sensor carriers. “The vessel itself isn’t of tremendous value. It offers value when you give it sensors that give back temperatures at sea or seabed mapping or accurate communications. It’s the data. The hardest part was making it robust and reliable (via testing and development). Now we see (the Mariner is) operational all the time with no downtime.” Paid 24/7 work has put Maritime Robotics on the cusp of greater success in other markets.
UN Gambit
In June 2017, after the 98th meeting of the UN Maritime Organization’s Maritime Safety Committee (MC 98), it was learned that regulatory support for autonomous shipping had been sought in a joint proposal from Norway, Denmark, Estonia, Finland, The Netherlands, South Korea, the U.K. and the United States. For its part, the Norwegian Maritime Authority, or NMA, said it was trying to preserve Norwegian innovation.
As was done for lead-free anti-fouling, a local innovation, the NMA-sponsored drive at the IMO aims to cement a coming role for — and the regulatory needs of — autonomous shipping. “This (initiative) shows that Norway is at the forefront with regard to facilitating new technology,” an NMA communique says, adding, “The proposal (at the IMO) to put autonomous ships on the agenda faced no opposition, which came as a surprise to many” who had expected countries that supply large numbers of mariners to balk.
Maritime Robotics’ early success predates these latest political strivings, but the company helped maritime agencies in Norway declare in late-2016 the entire 126-km-long waterway, Trondheimsfjord, a national autonomous-shipping test bed for the researchers of NTNU, Sintef Ocean or the Norwegian Forum for Autonomous Shipping, or NFAS. Oslo has allotted generous funding for research on unmanned vessels, and shipping interests in maritime stronghold Alesund disclosed plans to “wire-up” their own Storfjorden for autonomous vessel testing, starting with oceanographical data extracted from the fjord by sensors set up to model bridges and test ferry designs. It’s their “virtual ocean”
Virtual Oceans
It isn’t just a Norwegian thing. In May 2017, crane specialist MacGregor (part of the Helsinki-listed Cargotec that earned $4 billion in 2016) joined a smallish but elite unmanned Baltic Sea test grouping called One Sea Alliance, where companies aim to produce “the first fully remote-controlled vessels … in three years”.
One Sea is funded by the Finish Funding Agency for Innovation. “The benefits of co-creation are obvious — software experts, together with systems and equipment experts, can improve efficiency and safety throughout the whole value chain,” a MacGregor R&D exec is quoted as saying. The crane maker hopes to add a “scout” function to do predictive maintenance on the cranes of unmanned vessels. Wärtsilä and NFAS are along in One Sea.
Remote OSV
In September 2017, Wärtsilä remotely controlled from its San Diego, California, office an offshore vessel off of Scotland. The Gulfmark Offshore OSV was maneuvered for four hours by dynamic positioning, or DP, and a joystick 8,000 km away. The 80-meter Highland Chieftain had been fitted with a Wärtsilä Nacos Platinum package for navigation, automation, dynamic positioning and propulsion. Software was added to the DP system to route data over the vessel’s satellite link to staff onshore. “The onboard preparation for the remote testing was limited to one service engineer attending one afternoon,” a company source writes in an email. “A software update and establishing connection to the ships (satcoms) was needed to enable the tests.” The Gulfmark test bolsters Wärtsilä’s “virtual” services in the market while ironing out controls needed during auto-docking procedures.
New-build Showpiece
In May 2017, after the IMO proposal, Norwegian fertilizer firm, Yara, and the Kongsberg group announced they would build the world’s first fully electric and autonomous container ship.
Kongsberg will deliver controls for the electric drive, battery and propulsion systems while also fitting sensors and integrating the Birkeland’s electronics for remote operations that were due to start in 2020 (delivery in 2018, sea trials in 2019). A yard choice has been delayed pending more model trials. The 120 TEU, open-top container ship will begin life assisted by humans in a containerized bridge that’ll be lifted off when the vessel goes solo. The 3,200 dwt concept targets 10 knots though only expected to travel 6 knots moving between southern Norwegian town, Porsgrunn (fertilizer plant), and Larvik, a RoRo port. The electric propulsion is two azimuth pods and two tunnel thrusters fed from a 9 MWh battery back. Automatic loading and unloading will happen by electric crane once an automatic mooring system berths the ship.
“We’re comfortable”
Keys to autonomy for the Birkeland will be its proximity sensors of Radar, Lidar, AIS and an array of camera types (plus the all-important VPN connection by Inmarsat).
The Birkeland’s Internet hookup will connect three onshore centers handling emergencies, condition and operational monitoring, decision support and vessel surveillance. All are needed, as the ship will sail a regular 12-mile journey through a popular waterway. “Technologically, we’re very comfortable with this project,” CEO of the Kongsberg Group tells Norwegian E24. “The biggest challenge is of course the rulebook. I think we’ll put together a good (regulatory) solution here in Norway … but the big challenge becomes changing international regulations.”
Rolls-Royce Edition
Rolls-Royce Marine is also pursuing autonomous strategies, starting with remote monitoring sites for fleet and onboard systems in Aalesund and at Longva, a company assembly facility just across the fjord. A partnership with Google was announced as we were dropping in for a look-see.
“Since Birkeland and Ampere (an all-electric ferry), ship owners have been more willing to accept autonomous solutions,” says Rolls-Royce Marine’s VP of autonomous and integrated systems, Geir Olav Otterlei. Rolls-Royce is looking to automate (for data analysis) “one to two vessels” for a “Phase 1”, which is “getting (enabling system ACON) onboard”. “Phase 3” is a vessel becoming autonomous. “We believe (unmanned vessels) will be rolled out in a phased way,” says Otterlei. Rolls-Royce has captured data from 22 vessels, a nod to their possible future “autonomous” use, and is building a data analytics center. We visit the Logva site. “He’s logged on to the vessel,” Otterlei says. Screens show a fishing vessel, its temperature sensors blinking. “We’ll troubleshoot a little bit on the vessel.”
The deal with Google lets Rolls-Royce use the Cloud Machine Learning Engine “to further train the company’s (AI-based) object classification system for detecting, identifying and tracking” objects a vessel might encounter at sea. Google algorithms analyze faster “and better” than humans, and Rolls-Royce aims to use Cloud software to build machine-learning models that “interpret” terabytes of marine sensor data and link ship systems —including every vessel’s Automatic Identification System for better area awareness.
Robo-tug
Although he didn’t name the vessel, Otterlei seemed to think the only truly autonomous vessel currently earning commercially was a tug. We didn’t ask if he meant the Robert Allan RAmora, a Canadian design that uses controls derived from ROVs, AUVs and aerial drones and can be operated by a tug master in a nearby vessel with “a level of control no different from being onboard”. It’s main aim is tandem-tug ship handling, but it looks “robot-ready.”
While many are in the race, it seems Maritime Robotics may be the only group making money on a working pair of autonomous vessels. “We may be different than other companies because we actually do unmanned shipping with vessels already out there earning while others may still be doing the R&D,” Mr. Hovstein says. “We have this platform, and it works 24/7 for 40 to 50 days.”
It isn’t just the smaller autonomous platforms with “competition”. The Birkeland’s competitor launches in 2019 as Nippon Yusen Kaisha’s unmanned box ship, according to a Bloomberg report. Yet, Maritime Robotics also has an answer for larger vessels — a Robotics USV Conversion System. In May 2017, the Fugro Alumaster was converted and piloted remotely from shore in Trondheimsfjorden.
Things are happening quickly.
(As published in the December 2017 edition of Maritime Reporter & Engineering News)
Read Driver-less Ships: Autonomy in the Maritime Sector in Pdf, Flash or Html5 edition of December 2017 Maritime Reporter
Other stories from December 2017 issue
Content
- Interview: John C. Pfeifer, President - Mercury Marine page: 8
- El Faro and Perceived Deficiencies in the ACP page: 12
- Maritime Cyber Security: The Wrong Formula page: 14
- Navigating the New Norm page: 16
- Driver-less Ships: Autonomy in the Maritime Sector page: 22
- Maritime's Digital Transformation & Simulation-based Training page: 26
- Ship of the Year: MOL FSRU Challenger page: 36
- LNG: Maritime's Fuel of the Future page: 48