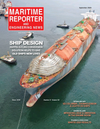
New Lives for Old Ships: Inside Keppel O&M’s FLNG Conversion Solution
As the focus on carbon emissions comes to the fore across all industries, Keppel O&M, which supports the circular economy concept and is a ship conversion leader, is able to help companies reduce their indirect emissions. Proof of this was delivery of the world’s first FLNG conversion solution that dramatically reduced the carbon footprint of the project as compared to new construction. There’s a second conversion project currently underway, and by the way: it’s faster to market and billions of dollars cheaper than a newbuild.
Keppel Offshore & Marine’s (Keppel O&M) conversion of a Liquefied Natural Gas Carrier (LNGC) into a Floating Liquefaction Vessel (FLNG) using a design and execution model jointly engineered by Keppel O&M and Golar LNG Limited (Golar), is estimated to save approximately 33% of greenhouse gas (GHG) emissions compared to an FLNG newbuild, according to a study conducted by environmental consultants, Environmental Resources Management (ERM).
The study, which assesses the converted FLNG Hilli Episeyo and a new build FLNG of a comparable design and specification, concluded that the converted FLNG saves a total of 63,343 tons of GHG emissions.
“Golar has long understood the merits of repurposing its fleet of high quality assets, having repurposed five vessels over the last 13 years with a further 2 currently in the process of being converted,” said Iain Ross, CEO of Golar LNG in a press release statement on the project. “The company has never scrapped an asset. The advantages of cost and speed to market have always been well understood and easy to quantify. Golar has consistently believed in the sustainability of this approach too and Keppel’s study now quantifies the environmental advantages of this part of our FLNG business model.”
“Keppel O&M has been the leader in conversions in various solutions since the first FPSO that it converted in 1981 and has amassed strong engineering and conversion know-how in this space over the decades,” said Chor How Jat, Managing Director (Conversions & Repairs) of Keppel O&M. “The push towards energy transition and cleaner fuels has also made our customers including the oil majors and field operators explore more sustainable solutions that can quantifiably reduce their carbon footprint. Companies are reviewing not only their own emissions, but also emissions throughout their value chain. They are relooking their business models and making commitments to their shareholders to reduce emissions.”
Keppel O&M supports the circular economy concept and the role conversions have played in providing sustainable solutions. “While the savings in GHG emissions from a conversion solution were intuitively clear, we wanted an objective study to quantify the significant savings after having completed a full scope FLNG conversion like the Hilli Episeyo which was the world’s first,” said Chor How Jat. “As steam-propelled LNG carriers are phased out by the industry, owners can also leverage this solution to repurpose their vessel for other uses, adding decades to the life of the vessel and reducing their carbon footprint. This study would also help shipowners make informed decisions as they think about what to do with some of their older assets.”
Gimi, the “World’s Second”: Following the delivery of the world’s first converted FLNG in 2017, Keppel O&M is currently undertaking its second FLNG conversion, Gimi, for Golar LNG. Photos: Keppel O&M
The repurposing of LNGCs into FLNGs adds decades to the life of the vessel, recapturing value that would have been lost through disposal. It also reduces the consumption of materials that would have been needed for a new build. For example, the use of virgin steel was reduced by 39% in the converted FLNG Hilli Episyeo, contributing significantly to the reduction in GHG emissions.
While there are an increasing pool of candidate vessels coming online for conversion, no two conversion projects are the same, and for Keppel O&M the key challenges were space constraint on the vessel as well as ensuring safety and efficiency in the integration and organization of the systems, said Chor How Jat. “We were able to draw on our experience to develop with our client an innovative method to create more space on the vessel while outfitting it with the latest technology. Jointly developed by Golar and Keppel O&M, the concept of using sponsons was an innovative game changer, creating new acreage to house additional equipment on the vessel and segregating the hydrocarbon and non-hydrocarbon systems to meet safe design requirements.”
As with any major conversion project, cost-efficiency is gained, or lost, in the intital design phase, as changes to plan raise costs exponentially as the project progresses. “We first conducted a robust one-year FEED study jointly undertaken by the key partners to identify upfront the critical issues concerning design as well as constructability,” said Chor How Jat. “That helped to define the product and project plans more accurately and enabled an efficient 39-month shipyard execution and six-month site commissioning on arrival at the Sanaga field, both of which are exceptional for a prototype.”
At the end of the day, as is the case in nearly every shipbuilding and conversion endeavor, experience goes a long way toward ensuring an effective, efficient conclusion. “Generally, LNG carriers can be converted into production and storage vessels - FLNGs, FSRUs and FSUs,” said said Chor How Jat. “Each conversion is different – it requires an experienced team with a specific and technical set of capabilities to meet the design and specification requirements of the project. For example, the type of containment system and storage capacity will impact the engineering considerations and technical feasibility of the project.”
To date Hilli Episeyo has performed consistently, providing proof of concept and attesting to the solution put forth by Keppel O&M and Golar. The FLNG has maintained 100% commercial uptime since its delivery in 2017, and recently surpassed its 42nd cargo dispatch. Keppel O&M is currently undertaking its second FLNG conversion, Gimi, for Golar which is being repurposed for the 20-year BP Greater Tortue Ahmeyim contract offshore West Africa. Keppel O&M has an extensive track record in the conversion of vessels. In addition to converting the world’s first FLNG in 2017, Keppel O&M converted the world’s first Floating Production Storage and Offloading vessel (FPSO) in 1981 and the world’s first Floating Storage Regasification Unit (FSRU) in 2008. It has converted 134 production vessels including FPSOs, FLNGs and FSRUs.
Read more in the September 2020 edition of Maritime Reporter & Engineering News: https://magazines.marinelink.com/nwm/MaritimeReporter/202009/#page/1
Read New Lives for Old Ships: Inside Keppel O&M’s FLNG Conversion Solution in Pdf, Flash or Html5 edition of September 2020 Maritime Reporter
Other stories from September 2020 issue
Content
- Training Tips for Ships #16: Using Student Exam Results to Measure OUR Performance: Part 2 page: 12
- History and Overview of U.S. Cabotage Laws page: 14
- “It’s my dream job”: One-on-one with Søren Andersen, CEO, StormGeo page: 18
- Maritime History: Columbia Lighting the World; How Classification Can Make a Difference page: 22
- Will Customers Redefine Design and the Science of Marine Propulsion? page: 26
- New Lives for Old Ships: Inside Keppel O&M’s FLNG Conversion Solution page: 34
- Mitigating Underwater Noise page: 42
- Fit for Fight: Navies challenged by COVID at sea, ashore page: 44