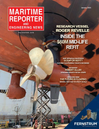
Ship Repair: Inside the $60m Refit of RV Roger Revelle
This month MR dives inside the $60 million refit of RV Roger Revelle, a project which leverages a treasure trove of ‘lessons learned’ from recent refits in the academic research vessel fleet and highlights the value of slimming the vendor list.
Research vessel (R/V) Roger Revelle is back at work after a midlife refit involving upgrades from top to bottom, bow to stern. The ship is owned by the Office of Naval Research and has been operated by Scripps Institution of Oceanography at the University of California San Diego since 1996. It is one of the largest ships in the U.S. Academic Research Fleet, an important asset to U.S. oceanographic research due to its range, payload, duration, and ability to safely conduct scientific operations in remote areas around the globe.
"Roger Revelle isn’t just revitalized, it is better than new,” said Bruce Appelgate, associate director and head of ship operations at Scripps Oceanography. “The midlife refit was an opportunity to apply everything we’ve learned about the ship since 1996, in order to make a great research vessel even more effective.”
The $60 million refit was supported by the Office of Naval Research (ONR), National Science Foundation (NSF), and UC San Diego, and highlights included:
- Repower: The repowering involved replacing the six existing air-cooled generators and split electrical bus configuration (auxiliary and propulsion separate) with four new water-cooled generators and an integrated bus (auxiliary and propulsion together). This included replacing major switchboards and transformers, as well as the propulsion motors and drives.
- BWMS: An Optimarin ballast water management system to help stop the spread of invasive species.
- Bow thruster: The installation of a new retractable ZF bow thruster to improve performance, vibration and noise.
- Cranes: An overhaul and replacement of overboard handling systems, with new cranes, a refurbished A-frame and hydrographic boom.
- Scientific Gear: The addition of a scientific instrumentation gondola.
Lessons learned
Ship design, construction and operation technology has changed mightily since RV Roger Revelle was delivered nearly a quarter of a century ago, and the team tasked to design, outfit and update the ship sought to use ‘lessons learned,’ both from the operation of the ship itself as well as experience from recent refits of other research vessels in the U.S. Academic Research fleet. A big factor in many of the refit decisions, in fact, were the shared experiences from the refit of the Thomas G. Thompson, operated by the University of Washington. “One of the great advantages that we’ve got at Scripps is being part of the community of ship operators in academic research fleet,” said Appelgate. “They shared everything with us, (including) their lessons learned.”
One specific area was taking the decision to replace a noisy, inefficient bow thruster with a new retractable unit from ZF, a change which drops the bow thruster – and the related noise and vibration related to its operation – several feet beneath the hull, making living conditions on the ship more palatable and enhancing the collection of scientific data.
While Paul Mauricio, Port Engineer, and his team did extensive work to improve the efficiency and noise signature of the original bow thruster, including pulling, machining and fine-tuning the impeller on the water pumper, “It would max out at about 270 rpm, it would start to cavitate and it would shake the entire boat.” As Appelgate and his scientific colleagues will attest, external noise and vibration at sea is not a friend of good science, particularly as research ships like the RV Roger Revelle use the bow thruster for many hours and days at a stretch to stay on station while equipment is in the water.
With the new retractable bow thruster from ZF, “once it’s deployed, the noise is below the ship, not transmitted through the hull” said Mauricio. While the performance of the unit was critical, so too was being able to efficiently fit it into the ship, minimizing the level of modification work needed to get the new unit installed. “One of the driving factors to (which unit we picked) was the fact that it would fit in a retrofit without drastically modifying the entire bow,” said Mauricio.
While noise and vibration is bad for science, it’s equally bad for quality of life on any ship. “On Roger Revelle, up in the bow is where a bunch of our berthing quarters are located,” said Appelgate. “Typically that’s where the graduate students get put, so I was stuck up there (a few times). The reason you get ‘stuck up there’ is because it was noisy as heck because you were next to that (old) bow thruster. Even without cavitation, it was super loud. By installing the extendable bow thruster, it moves the source of noise farther away.”
The R/V Roger Revelle pictured at sea for a 10-day commissioning and calibration cruise following its midlife refit. Photo Copyright: Scripps Institution of Oceanography
Better science, minus the bubbles
“I’m a geologist,” said Appelgate. “Back when I was doing research, my interest was in sea floor mapping,” and I sailed on the Roger Revelle as a scientist before I worked at Scripps. According to Appelgate, the configuration the ship’s mapping sonars when built in 1996 was “the worst place you could possibly pick on the ship for your mapping sonars.”
“Ships like Roger Revelle are very broad and not super long; so it pitches a lot,” said Appelgate. “As it goes through the water pitching, it makes lots of bubbles and the bubbles sweep down along the hull. Bubble masking is something that we understand very well now, but not so much back in 1996. The place where all the transducers were (originally placed) were right in the place where bubbles would wash down and, basically, wipe out your sonar signals.”
“In the period since then, there’s been a lot of work done on how to mitigate that on a vessel without rebuilding the ship.”
The answer was a gondola that puts the transducers a few feet below the hull “on a big metal structure that looks like a hammer head shark. It allows the bubbles to stay up next to the hull while the transducers are below them.” While the gondola was a boon for the science, it was one of the major design and construction challenges in the project. “Building that and then reconfiguring all the cable runs and moving the sonars down onto that thing was a big deal,” said Appelgate.
“You know, the ship is the science,” said Appelgate. “I cut my teeth on making and operating sonars that were towed behind a ship. As we got better with sonars and motion sensors, those evolved into multi beams. Then we put them onto the ship. Now, all of a sudden, the ship is your sensor. I think it’s a valuable exercise to look at a ship holistically in that there’s an instrument on the ship, let’s say a multibeam, that’s only as good as everything that it’s attached to. Just like vibration, if you’re transmitting a bunch of mechanical sound into your sonars, you’re going to get junk. The ship is the instrument.”
The answer to 'bubble masking' was the addition of a 'gondola' that puts the transducers a few feet below the hull on a big metal structure that looks like a hammer head shark. Image courtesy Glosten
Cleaner power
The original ship contract value was for $35 million to take care of specific ship systems – propulsion, controls, HVAC, piping, ballast water management – and steelwork to extend the life of the ship another 15 years or more, said Appelgate.
But “we knew that other issues on the ship needed to be addressed, or the primary users of the vessel just wouldn’t be satisfied.” That’s where the upgrades to science systems came in, adding another $25 million to the project.
“The repower itself was intense,” said Mauricio. “We gutted the entire engine room and we pulled about six miles of cable, and we replaced about six miles of cable. There was not a square foot of that ship that wasn’t disturbed.”
“We ended up going with Caterpillars for our main engines, two 3516’s and two C32’s, running them at 1800 rpm,” said Mauricio. “We put 2100 KW generators on the 3516’s and 940 KW generators on the C32’s.” He said while the addition of the scientific gondola increased fuel consumption by about 4%, the efficiency of the new machinery made it break even.
“The biggest challenge with this project is the integration of all new and existing systems,” said Benton Strong, Vigor, the shipyard. “Nearly every major system was either replaced entirely or upgraded significantly, merging elements of new construction and ship repair into one cohesive project.” To streamline the flow of information among multiple parties, Vigor commissioned a custom document control system that allowed key partners to upload, review, comment and approve documents on a shared web based platform.”
“We made the mistake in the past by having different vendors supply equipment,” said Mauricio. “The integration is always difficult, and on a retrofit like this, it’s one of the biggest deals. It’s inevitable that if you have multiple vendors with multiple equipment there is always a problem, but it’s always ‘his problem, not mine.’”
To that end, according to Mauricio, minimizing the number of vendors and use COTS equipment was critical, as when the ship was built it included a broad diversity of equipment and manufacturers, which ultimately made the ship more difficult (and costly) to service. “Our goal here was to simplify everything in common off-the-shelf equipment,” and it was able to use experience building the RV Sally Ride five years ago to help in the process. “A lot of our choices were driven by that familiarity with vendors, our crew’s familiarity with equipment,” said Mauricio. “We felt that if the crew is more interchangeable and you’re familiar with equipment, we can keep our boats in better condition.”
A point of focus too, for all machinery was to mitigate noise and vibration. “We have learned a lot about power management and efficiency,” said Mauricio. “We incorporated all of that when we did the designs for the new propulsion systems. (Critical was keeping the vessel quiet as) Bruce’s sonars, their data, relies on the vessel being extremely quiet as far as noise transmitted through the hulls.”
To that end much time and effort was expended in the engineering phase to evaluate noise sources and devise means to mitigate. “Nothing makes direct contact with the hull; to sonars,” said Mauricio. In addition, Vigor partnered with Bruce S. Rosenblatt & Associates (BSR) to provide detailed engineering support of structural, mechanical and electrical systems. BSR used 3D modeling to develop detailed production level drawings suitable for material procurement and shop prefabrication. The 3D modeling process also helped identify design issues such as equipment and piping system clashes early in the design phase.
Engine room removal access. Image courtesy Glosten
Cadmatic model of main engine room with new equipment. Image courtesy Glosten
Autonomy versus crewed ships
While there is a decided move towards increased use of autonomous systems in the ocean study space, Appelgate contends that there are still many jobs – particularly those that are far from shore and power intensive – that still demand a combination of crewed ships and autonomous systems.
“The utility of unmanned systems is that you can achieve a persistence at sea that’s not possible with presence,” said Bruce Appelgate. “Unmanned systems that we’re deploying extend the ability of us to do our sensing at sea. It makes ships more useful.”
“Maybe in 50 years it will be different, but things like going to the southern ocean and doing CTE profiles, and the kind of hydrography that the big ships do routinely, you just can’t do it (with fully autonomous systems alone); you need too much power. Autonomy extends the utility of the service vessels. It makes us more efficient and gives us persistence.
The Network
Upgraded network capabilities support the significant amount of data collected from these instruments. A new virtual desktop infrastructure (VDI) includes display consoles for all systems throughout the ship, reducing the workload for scientists and crew members alike who use these during their operations. New cyberinfrastructure and centralized computer management helps the ship’s technicians maintain security and reliability of onboard computing and networking. “Something that has totally been fast tracked in the last nine months is our ability to use SATCOMs; we have realized the potential of SATCOMs in the academic research fleet in a way that we knew was possible, but there really hadn’t been the pressure to do it. In the midlife refit of Roger Revelle, Appelgate said “we completely rethought how we were going to do our cyber infrastructure on the ship.”
“What we did with Roger Revelle is we reimagined and reengineered how that infrastructure could be configured in order that we could make the most advantage of existing SATCOMs, and anticipating things like these low earth orbit systems that would be coming out soon that will allow even higher bandwidth at lower cost in a broader geographic area.”
“We did a demonstration with Roger Revelle on sea trials, a test shot with a SATCOMs provider (where we) bumped up the internet connection on the ship to be equivalent to about what I experience at home. All of the sudden we went from a situation where you could barely get an email out to streaming video and real-time sending undecimated data sets, big data sets back to shore to be analyzed in near real time and returned to the ship. We’ve demonstrated that it can work, and it really is going to be a game changer for how U.S. scientific community does work at sea in the short term.”
The ship RV Roger Revelle
R/V Roger Revelle was put into service in 1996. It honors former Scripps Oceanography Director Roger Revelle who is widely regarded for not only establishing the institution as an internationally prominent science center, but for solidifying the decades-long relationship between Scripps Oceanography and the U.S. Navy.
“Roger Revelle was a visionary who – back in 1946 – envisioned the Office of Naval Research as a world leader in sponsoring oceanographic basic research, and later foresaw the need for a new University of California in La Jolla that eventually grew around Scripps,” said Tom Drake, director of the Ocean Battlespace and Expeditionary Access department at the Office of Naval Research. “He also suggested the likely trajectory of the Earth’s climate, which we are now observing.”
Revelle served as an oceanographer for the U.S. Navy during World War II and was instrumental in the founding of the Office of Naval Research. Roger Revelle worked at Scripps Oceanography before and after the war and served as its director from 1950 to 1964. He was among the first to consider the implications of the accumulation of carbon dioxide in the atmosphere and absorption rates of the greenhouse gas by the ocean. A continuous profiling system under the ship will also measure carbon dioxide in seawater, an essential component of ocean acidification research.
The first research expedition on the all-new R/V Roger Revelle got underway in early November, an essential research mission led by UC Santa Barbara to retrieve ocean bottom seismometers measuring seismic activity and to collect rocks from seamounts and underwater volcanoes.
“The ship went down to about the Cook Islands where we recovered ocean bottom seismometers,” said Appelgate. “We retrieved 30 out of 30 of these ocean bottom seismometers, which is terrific as these things are worth half a million dollars each; the data on them are priceless. They had been up for a year and they were running out of batteries, so we had to go get them. It was a high priority cruise.”
The second research cruise began on Christmas day 2020.
The R/V Roger Revelle pictured at sea for a 10-day commissioning and calibration cruise following its midlife refit.
Photo Copyright: Scripps Institution of Oceanography
RV Roger Revelle Refit ‘By the Numbers’
- Value: $60m
- Shipyard contract value: $43.8m
- Workers: 1,000 – including subcontractors and vendors.
- Duration: 14 months (April 15, 2019 – July 3, 2020).
- Cable: more than 21.75 miles of cable installed.
- Pipe: More than 3 miles of pipe installed.
Read Ship Repair: Inside the $60m Refit of RV Roger Revelle in Pdf, Flash or Html5 edition of January 2021 Maritime Reporter
Other stories from January 2021 issue
Content
- Designing Boats: Robert Allan Ltd. Surpases 90 Years (& Counting) page: 14
- Fuel, Propulsion, Emissions & the Decision to Scrap or Refit page: 24
- Ship Repair: Inside the $60m Refit of RV Roger Revelle page: 30
- Interview: Tim Leach, Glosten, Discusses Efficient Refit by Design page: 36
- Op/Ed: SS United States, the Maritime Thoroughbred page: 58