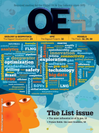
Page 27: of Offshore Engineer Magazine (Dec/Jan 2014)
Read this page in Pdf, Flash or Html5 edition of Dec/Jan 2014 Offshore Engineer Magazine
Drilling
Weatherford
As drilling operations keep moving to deeper waters and more remote reser- voirs, conventional means of downhole tool activation are unable to keep pace.
Mechanical actuation via ball drop, shear pins or push-pull mechanisms means that tools may only be opened or closed
XBAT azimuthal sonic and one to two times before the entire bot- ultrasonic LWD. Image from Halliburton.
pore pressure and fracture gradient issues tomhole assembly (BHA) must be pulled resulting in tight drilling windows. where maximizing reservoir recovery to replace the equipment.
Halliburton
Hess uses enabling technologies such as through placing wells in the best spot Weatherford has called on its 80-year underbalanced, managed pressure, and The drilling industry has seen two major has been challenging. A major sweep of history of providing high-performance air drilling with low rheology drilling infection points in the last fve years developments in well placement tools drilling tools to address the limitations muds and cements to improve wellbore – proliferation of horizontal drilling (Geosteering tools) and planning tools of mechanical actuation. One area of pressure control in more than half of linked to the growth of unconventional has helped the industry make a step focus is the development of drilling tools our current projects. Another example drilling and accessing complex reser- change in well economics. This is an area that are activated and controlled via of improved drilling methods is on- voirs in deeper water environments. of continued rapid development where radio frequency identifcation (RFID). command expandable reamers for hole Both of these challenges have guided the reservoir models will evolve in real Programming and pumping small RFID enlargement to help reduce equivalent the key technology developments and time as the well placement tools observe tags downhole to control equipment in circulating density during drilling and applications. reservoir horizons. the BHA provides several benefts to casing installation. The latest generations The frst major infection point was The last and probably highest impact well construction, chief among them the of rotary steerable tools improve our abil- the advent of horizontal drilling required trend is moving from drilling tools to ability to activate and deactivate a tool ity to more precisely place wellbores to to economically exploit the unconven- performance based matched drilling multiple times and on demand. The tool maximize production with better reliabil- tional resources and the consequent systems. A system involves the drill bit, can thus remain in the hole for much ity and reservoir evaluation telemetry. development of drilling systems that the drilling bottomhole assembly (BHA) longer than tools controlled by mechani-
Equipment reliability is a cornerstone were effcient, able to deliver high dog and the fuids (the mud system). This cal means, which improves drilling of drilling and completion performance. leg wellbores and highly reliable to integrated approach has allowed the ser- effciency and lowers rig costs.
Hess’ quality assurance program partners avoid multiple trips into the wellbore. vice providers to match the best systems, Weatherford’s RipTide RFID drilling with contractors to align objectives and
An additional feature has been systems leverage on past knowledge and add a reamer, for example, is the industry’s expectations to create a clear plan for that can drill the entire well trajectory common consolidated planning platform, frst high tech, intelligent underreamer. controlled equipment deployment in the in one run i.e. avoid downhole drilling with technical experts to help reduce risk Fitted with RFID technology, this drilling feld. Continuous improvement methodol- assemblies that are specifc to a hole to the operators. The integrated drilling underreamer is capable of being activated ogy ensures the overall service delivery section. This major development can be systems approach projects have in most and deactivated on demand multiple processes are actively assessed for oppor- summarized as the High Dog Leg Rotary cases outperformed standard discrete times while tripping or drilling. The tunities based on industry performance
Steerable Drilling systems provided product-based projects. The integrated ability to control when the premium data. This approach ensures reliability can by various major service companies. drilling systems will eventually lead to PDC cutter blocks are deployed during be planned into the business while manag-
The need for effciency has also led to automated systems in the near future borehole enlargement operations is key to ing the reactive aspects inherent in well a resurgence of drilling mud motors with access to global lessons learnt and increasing drilling effciency.
operations.
(positive displacement motors), includ- technical expertise as well as address the The JetStream RFID circulation sub
Operators face the challenge of engi- ing customized high performance basin critical industry need to reduce rig site builds on the success of the RipTide. neering and integrating these capabilities specifc mud motors. personnel. With its RFID-activated circulating into a well design for operations teams A related development has been the valve, the JetStream features essentially to deliver. A robust well delivery process need for drill bits that are matched or Akshay Sagar is the unlimited opening and closing capabil- organizes the technical work and lever- aligned with these new drilling systems global business ity, without the need for fow-restricting ages past learning to fnd the best engi- and a number of new drill bits have manager for Drilling mechanical actuation devices such as neering solutions to maximize the value emerged especially for the high dog leg and Drilling ball seats. This provides full-bore pump- of the well. effciency drilling. Engineering ing and improved hole cleanup at higher
The next major development has Solutions for annular velocities.
Matthew Isbell been the drive to acquire information in Halliburton (Sperry Most recently, Weatherford intro- serves as a drilling drilling time and not post drilling. This Drilling). Akshay duced the RipTide RFID Rathole Killer, optimization advisor has led to the increase in measurements looks after the Drilling Engineering an underreamer based on the RipTide at Hess, specializing while drilling/ logging while drilling Solutions (DES) group – Sperry’s latest RFID technology but designed for place- in drill bits and which in turn has supported well bore integrated service offering. He also looks ment between the BHA’s measurement- drilling optimization. integrity and well bore stability during after the Directional Drilling portfolio while-drilling (MWD) tools and the
He holds 26 drill bit drilling operations. The most notable and strategy and future roadmap. He rotary-steerable system (RSS). Unlike patents and has achievement has been the sonic and high received a Bachelor of Technology with a the conventional RipTide reamer that published 23 technical papers. Isbell has resolution imaging LWD systems. concentration in civil engineering from is placed above the MWD assembly, the held a number of drilling technology Another major development in the the Indian Institute of Technology in New Rathole Killer is opened and closed via roles in R&D, feld engineering, market- drilling world has been the move to com- Delhi and an MBA from the Rotterdam pump-cycle activation to underream the ing and managerial roles. plex geologies and Deepwater prospects School of Management in Holland. rathole section of the well. The tool’s oedigital.com December 2014 | OE 29 028_OE1214_D&C1.indd 29 11/21/14 3:25 PM