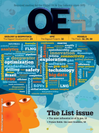
Page 28: of Offshore Engineer Magazine (Dec/Jan 2014)
Read this page in Pdf, Flash or Html5 edition of Dec/Jan 2014 Offshore Engineer Magazine
are actively being deployed in high- Eddie Valverde pro? le wells where performance, reli- is Weatherfords’s ability and innovation are required. And global product because these tools contain pressure line manager, sensors, they can be actuated via pump Performance Drilling
Drilling cycle, a major bene? t in deepwater and Tools. He joined long-lateral wells that limit the effective- Weatherford in 2009 ness of ball drop-activated tools. as Global Product
These tools also have the capability Line Manager of recording drilling data via onboard where he has spent the last ? ve years where he has spent the last ? ve years accelerometers, pressure transducers developing and commercializing RFID developing and commercializing RFID and temperature sensors, making them enabled downhole drilling tools. He enabled downhole drilling tools. He
RFID technology. Photo from Weatherford.
from intelligent measurement and con- graduated from Stephen F. Austin State graduated from Stephen F. Austin State position in the BHA allows for a sig- trol devices. Weatherford continues to University, Nacogdoches Texas, in 1995. University, Nacogdoches Texas, in 1995. ni? cantly shorter rathole (to just a few develop RFID-enabled versions of other He began his oil? eld career with Smith He began his oil? eld career with Smith meters above the RSS), without having tools that are currently mechanically International and held various positions International and held various positions to trip out of the well for a dedicated activated, thus revolutionizing their including International Sales Manager, including International Sales Manager, cleanout run. use for drillers’ most demanding Product Line Technical Specialist, and Product Line Technical Specialist, and
These deepwater-proven technologies applications. Regional Operations Manager. Regional Operations Manager. needs to deliver cost reductions to create a future for ? eld developments and improve competitiveness on existing assets.”
Chevron’s deepwater bet
May says Chevron’s deepwater tech-
By Elaine Maslin already pushed boundaries, to continue nology vision spans from “the top to eepwater is a big play for Chevron pushing the deepwater envelope, more the bottom,” from dry tree solutions to
D – one which comes with challenges need to continue to be developed, not seismic imaging. that the super major is working hard to least in drilling and completion. Subsea imaging, drilling and comple- overcome. “Technology is enabling deep water tions, subsea systems, ? oating production
According to Craig May, managing direc- development by making the impossible facilities and safe operations, are some tor Chevron upstream Europe, Chevron’s possible and the possible less expensive,” of the key areas Chevron is working on, deepwater production, which includes a he said during a deepwater-focused pre- says May. broad portfolio of projects from heavy oil vention in Aberdeen in October.
Dual gradient in deepwater to sub-salt, “big gas” and LNG, will almost “Records continue to be set around the double by the end of the decade. world as the industry explores deeper Looking at drilling speci? cally, Chevron’s
Technology, he says, will be key to prospects. We have moved from bigger drilling ef? ciency program has been look- enabling projects, but also reducing costs, to smarter developments and we need ing at dual gradient drilling, May says. he says, and while new technologies had to continue to be smarter. Technology “Dual gradient drilling is a great example of where the impact of water depth on mud weight is eliminated by placing the mud pump on the sea ? oor.
So this removes the riser effect and is essentially like drilling the well on the sea ? oor,” he says.
Chevron is currently using dual gradi- ent drilling technology in its exploratory drilling. “The dual gradient drilling tech- nology creates a step-change in our safety exposure by simplifying the well designs and reducing the drilling bundle,” May says.
“Bene? ts include fewer casing runs, as well as larger casing at the reservoir depth, which gives us more completion options. Advanced drilling ef? ciency ini- tiatives have helped reduce drilling times and therefore explosive times in the Gulf of Mexico Wilcox trend from over 160
Transocean’s drillship Discoverer days in 2004 for Chevron’s Jack number
Deep Seas, which drilled at Chevron’s 1 well to 80-90 days per well by 2009, so
Tahiti prospect. Image from Chevron - Statoil ASA quite a signi? cant prize.”
December 2014 | OE oedigital.com 30 028_OE1214_D&C1.indd 30 11/21/14 3:26 PM