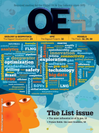
Page 46: of Offshore Engineer Magazine (Dec/Jan 2014)
Read this page in Pdf, Flash or Html5 edition of Dec/Jan 2014 Offshore Engineer Magazine
holding (tensioner) capacity during instal- be in a position to win a share of the lation. Due to the heavy, thick-walled contracts. That means having a combina-
DNV GL – Oil & Gas pipe and long section of the pipe from the tion of the right people, relevant assets,
The main challenge vessel to the seabed, the required tension innovative technology and ability to related to pipelines in or holding capacity restrict the number of work in remote locations.
Pipelines deep and ultra-deep available installation vessels. As projects become more complex, waters is the high Both these additional challenges limit contractors will need to be able to handle external pressure that the maximum pipe diameter at differ- deepwater umbilicals, install heavy may cause the ent water depths. Below 1000m, the wall structures and handle ever increasing pipeline to collapse. thickness increases almost linearly with top tensions making future assets such
This potential failure the water depth and pipe diameter. At as the DLV2000 essential to the indus- mode is normally the same time, the ability to manufacture try. Without vessels such as the NO102,
Asle Venås,
Segment Director dealt with by line pipes decreases according to the a truly deepwater enabler for ? exibles
Pipelines increasing the pipe pipe diameter and the tensioner capacity and umbilicals, and the DB50 with its wall thickness. At large water depths, this requirements increase. This means there specialized deepwater lowering system, will require very costly thick-walled pipes, are some practical limits for the maximum
McDermott could not have completed which in turn are dif? cult to manufacture pipe diameter to be installed at different projects such as the recent Jack and St and also to install due to the weight. water depths.
Malo in the Gulf of Mexico.
When a pipeline is installed, it is In addition to the wall thickness and Each project has its own distinctive exposed to high bending in the so-called weight, deep water can also provide chal- challenges which often require unique sag bend close to the seabed. In deep lenges with respect to seabed interven- solutions and innovative technology. water, high external overpressure may, tion, geo-hazards, buckle detection, pre- One such innovation is the creation of especially in combination with this commissioning, surveys and inspections, the world’s largest forged specialty valve bending, increase the risk of pipe cross- hydrates as well as any repairs needed. for the Ichthys project offshore western section collapse. In addition to increasing Australia. Six 42in valves have been the wall thickness the collapse resistance designed and created for the project;
McDermott International may also be increased by improving the each one measures approximately nine
D line pipe characteristics through manu- espite a ? uctuating meters high and weighs more than facturing procedures with improved oil price, the experts 100-tonne.
material characteristics, resulting in a predict growth in the Assets and technology alone do not more perfectly round pipe as well as subsea market and make a successful project, particularly in improved collapse resistance. continued opportu- emerging countries where new oppor-
However, when solving the collapse nities for expansion tunities are opening up. A successful challenge by increasing the wall thick- into new frontiers. approach requires a contractor to be ness, two new challenges occur; the man- The challenge for experienced in investing and sensitively
Tony Duncan, ufacturing challenge caused by the heavy any contractor such developing the necessary onshore infra-
Executive Vice pipe wall and the challenge relating to the as McDermott is to structure, and building local participa-
President, Subsea tion by employing and growing local talent. By taking this approach, projects can have a real and positive transforma- tional change.
Allseas
Challenging aspects are the high wall thicknesses of pipelines and risers, which are driven by external deepwater collapse pressures.
Pipeline end ter- mination structures
Edward Heerema,
Allseas’ and in-line structures founder in deep water are complex with their valves, connector assemblies and other equipment, oper- ated by remotely operated vehicles.
Deepwater risers are subject to envi- ronmental loadings which affect their fatigue lives, leading to strict welding criteria.
Allseas’ pipelay vessel, the . Solitaire Image from Allseas.
December 2014 | OE oedigital.com 48 046_OE1214_Pipelines1and2.indd 48 11/21/14 6:10 PM