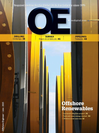
Page 47: of Offshore Engineer Magazine (Jun/Jul 2015)
Read this page in Pdf, Flash or Html5 edition of Jun/Jul 2015 Offshore Engineer Magazine
Pipelines (HPHT) environments where pressure, to create a model for sand transport in long-distance subsea volume and temperature (PVT) changes tiebacks. The ideal model would have the potential to solve are more pronounced and occur very problems of pipe and equipment sizing, locate places of sand quickly. Flow assurance issues can be deposition and improve sand management strategies. The previ- very costly to repair, or if unrepaired, can ous particle transport models did not refect the critical factor lead to erosion and corrosion and can of fow pattern transition and therefore can be unreliable under
STRONG endanger asset integrity. Furthermore, varying operational conditions. deposition of solid matter reduces the Several experiments were conducted during a study to line throughput, sometimes leading to establish the minimum transport velocity (MTV) for rolling and complete blockages and making proft- suspension for different fow patterns. The result of that study able production of hydrocarbons practi- (Bello et al (2011)), were empirically derived equations for the cally impossible. MTV and fow velocity profles under different fow regimes. As
Many researchers have attempted to a continuation of that study, the subsequent project was to cre- understand the physics of unprocessed ate an analytical model in MS Excel (using the concept of MTV)
LIGHT fuid fow, characterized as multiphase to locate places of deposition in pipelines and to formulate a fow. Primarily, the scientifc efforts were method to assess the severity of blockages.
focused on understanding the phase interaction between and its impact on Originally from Komi Republic, Russia, fow dynamics. The greatest diffculty Alexander Belkin earned his frst degree in is that the nature of the fow is transient Drilling Well Engineering in 2013 from due to constantly changing fow patterns, Ukhta State Technical University. He so it is hard to predict fow behavior. recently graduated from RGU with an MSc
SAFE
As part of the development of a com- in Oil and Gas Engineering. prehensive subsea tieback management strategy, the Well Engineering Research Belkin presented this paper at the Energy
Group at Robert Gordon University in Institute’s Msc Energy Paper competition, in which he was one
Aberdeen, Scotland, has endeavored of six fnalists. the solid phase was transported in suspension. It is important to note that the safest method of the solid phase transport is
FAST the production system, the project moved to the second phase in suspension, as when particles roll there is the possibility of – creation of the analytical model in MS Excel with the main deposition as pressure drops further down the pipeline. objective of fnding places of solid phase deposition. The solid In places of deposition, the severity of blockage is determined phase loading and dimensions were assumed, specifying the fow by the height of the deposited bed, which can show the degree as diluted with spherical particles. The fuid fow parameters were of production impairment. In this project it was attempted to transferred onto the Excel spreadsheet for calculations, which analytically derive it from the given equations. Evidently, the top started with plotting fuid fow velocity feld profles for diferent of the deposited bed is at the point where transport occurs, in fow regimes. In order to do this, other words, where the actual fow velocity is equal to MTV for
RELIABLE the pipeline diameter was divided rolling. Thus, the two equations were equalized and the distance in fve segments on each side from from the pipe center where transport occurs was expressed. It the pipe center and the fuid velocity then became possible to fnd the height of the bed by subtract- was found at each of them. ing this distance from the rest of the pipe diameter space. The
With the velocity profles thus method proved to be reliable and demonstrated only small error generated it became clear how margin (<0.5 %). quickly the fuid moves in the pro- The project has laid the ground work for further develop- duction system. The next step was ment and industrial application. Apart from enabling location of to fnd the minimum transport veloc- places of deposition in the pipeline, it has given the insight into ity at which particles would roll and the key relationships between fow parameters and the solid be transported in suspended mode. deposition behavior as well as severity of blockage. The next
Obviously, if somewhere in the pipe- step for this model will be its application in a feld case study line the lowest barrier for transport and comparisons of results with a real-time data. There is the (MTV for rolling) is not met by the opportunity to further complicate the model by adding parame-
TESTED & PROVEN PERFORMANCE actual fuid velocity it means that ters close to a real case scenario (non-spherical particles, paraf-
Extension Pendants particles will deposit on the pipeline fn, hydrates and wax occurrence, dense fow, varying operating
Heavy Lift Slings wall. Therefore, the comparison between the two velocities was conditions).
done and showed that the condition for solids transport was not On demonstrating the reliability of this model and acknowl-
Tow Lines satisfed only in the vertical section of the wellbore. edging its practical importance it would be possible to incorpo-
Winch Lines
The higher barrier (MTV for suspension) was also found and rate it into an industrial software. Thus, it would be a useful tool compared with the actual fow velocities. The comparison showed in the production engineer’s hands for predicting solid deposi- that although the condition for transport was satisfed in most tion behavior in the production system under varying operating
SamsonRope.com of the pipeline, particles were rolling alongside of the wall. Only conditions. Subsequently, it might act as a part of an integrated ®
Dyneema is a registered trademark of Royal DSM N.V. Dyneema is DSM’s high-performance polyethylene product.
in the horizontal section of the pipeline and close to the manifold subsea tieback fow assurance management strategy. • oedigital.com June 2015 | OE 49 048_OE0615_Pipelines.indd 49 6/1/15 7:42 PM