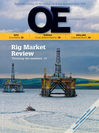
Page 33: of Offshore Engineer Magazine (Mar/Apr 2017)
Read this page in Pdf, Flash or Html5 edition of Mar/Apr 2017 Offshore Engineer Magazine
planning and execution of an ERD well, like that,” he adds. TDTECH, a New Zealand company,
DRILLING according to Halliburton. Today, every However, the newest developments has the next generation of stabilizers and bit of data can be used and analyzed au- are in the area of vibration management. centralizers, according to Hutchison. The tomatically in real-time and then used “If you avoid vibration, generally the bit company offers mold-on drilling stabiliz- to benchmark future operations. will hold up,” Hutchison says. “When ers and casing centralizers that are less “The industry, through specialized you download the report and see what expensive because these are simpler than
ERD wells push software packages, has the capability to has been happening with the vibration, previous mold-on centralizers. do automatic classi? cation of rig activity you realize that the bottomhole tools “Previous polymer casing central- with very high accuracy and de? nition,” don’t fail; we beat them to death. izers were slip-on type while polymer says Wael El Deftar, Sperry Drilling “We’re almost to the point where we drilling stabilizers used a combination chief global advisor, at Halliburton. “We can run vibration sensors all the way of materials, including steel, aluminum distance can start to benchmark our performance along the drillstring,” he continues. and fasteners to hold the tools in place. on every single activity from the mo- “Then you can see the different harmon- Our tools are a single piece, rather ment the well is spudded until the mo- ics if you have vibration. It explains benign, high-grade polymer with zero ment it reaches total depth. Over time, strange wear patterns and why we’ve metal parts,” says Geoff Murray, general we can start to identify and quantify damaged the bit. If you don’t have your manager, TDTECH.
boundaries where we are spending too much time BHA (bottomhole assembly) stabilized Its Archimedes Screw pumping effect for no reason (hidden non-productive and the bit face is vibrating, it drills an helps reduce equivalent circulating den- time). over-gauge hole, and you don’t have the sity (ECD). Drillstring rotation revolves “We can start doing performance com- same directional control.” the screw elements, thereby pumping parisons well-to-well, rig-to-rig, crew-to- crew and ? eld-to-? eld. We can standard- ize performance by capturing the areas where we are excelling and supporting the crew’s efforts. We also ? nd the areas to reduce inef? ciency,” he explains.
Halliburton does a comprehensive risk analysis method as one of its approaches.
The company analyzes the data and ? nds what types of problems will be faced dur- ing the ERD well execution. “We start to put measures into the design to overcome this risk in case it materializes. We call this approach the Global Drilling Risk
Factor Method. It allows us to be prepared for contingencies,” he continues. “Even if we run into trouble, we don’t have to spend much time on this problem because we have the contingency plans available.
That’s how we can improve performance.”
The company has a worldwide engineering group called the Drilling
Engineering Solutions Group to deal with
The Reelwell Drilling Method is a closed-loop drilling system that uses a dual drillstring. challenges such as ERD project planning.
The annulus between the dual drillstring and the wellbore remains static and is free of drill cuttings.
Image from Reelwell.
Blending old, new technology
While new technology is always a great attraction, getting more out of existing technology or even using it correctly also has huge value, Hutchison says. “We fre- quently come across opportunities that can be delivered with a bit of clever engi- neering, rather than a costly rig upgrade, which was perceived to be ‘essential.’”
One example of using an older tech- nology correctly is pumping cement plugs. “When a well is drilled, cement plugs are pumped. It’s very simple. But, have most operators pumped a cement plug to 30,000ft? It was good for wells at
With ERD operators have drilled over 40,000ft o