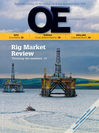
Page 34: of Offshore Engineer Magazine (Mar/Apr 2017)
Read this page in Pdf, Flash or Html5 edition of Mar/Apr 2017 Offshore Engineer Magazine
Extended reach drilling
Industry achievements
DRILLING
This industry noseplot shows the record ERD wells worldwide.
Image from Merlin ERD Ltd.
the drilling mud and reducing ECD. the risk of swabbing and surging, which with aluminum drillpipe is the connec-
Another means for reducing ECD is via are key causes of wellbore instability. tions, which are generally made of steel. better hole cleaning, wherein less cut- The tool pro? le and monoblade orienta- The body is quite soft so it wears. The tings in the hole equate to less pressure tion reduces torque, drag and torsional TDTECH mold-on centralizers can be drop, Murray explains. vibration, which are key causes of bore- attached to the aluminum drillpipe to
Its Python Polymer Rotating drilling hole enlargement and subsequent BHA reduce the wear,” he explains.
centralizer/stabilizer provides 60% to 95% component failure. Another technology undergoing wear reduction along with more than 50%
There are also improvements in trac- development is the Reelwell drilling torque and drag reduction, which might tor technology and intelligent comple- method (RDM). A trial was performed as enable use of smaller drillpipe. The wear tions, Hutchison notes. “It is often not part of a joint industry project on ERD reduction results of the slippery, ? ber-re- the drilling; it is the completion or the wells (called ERD 20km+) by Norwegian inforced polymer exhibits a fraction of the well service that is the problem. Drilling company Reelwell, supported by The abrasive wear of metal-on-metal contact, is the easy part.” The really clever solu- Research Council of Norway, op- he continues. It also reduces stick/slip and tion is how you complete the well, and erators Total, Petrobras and DEA, and associated vibration.
then how you service the completion if Halliburton.