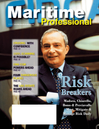
Reduce Boatbuilding Risk by Starting with Requirements
Managing the risks associated with a new ship acquisition, whether commercial or military, can be a daunting process. For the commercial operator, the new ship must make a reasonable profit after the cost of design and the annual operating costs are accounted for. The warfighter must fit his new acquisition into ever-shrinking fiscal budgets while ensuring that a vital mission capability is met. Among the risks that must be considered are:
- Programmatic Risk – Will the selected hull form and associated requirements successfully meet the owner’s needs?
- Cost Risk – Are the desired requirements affordable, and will they result in a successful and profitable operation?
- Technical Risk – Are the desired requirements driving the ship design to a point that is beyond the current state-of-the-art?
- Schedule Risk – Will the desired requirements result in a ship design that can be designed and built in a timely manner?
All of these risk areas ultimately influence cost in one way or another. The common theme to all risk areas is requirements. Requirements are often set by what owners/operators would like to have and not necessarily by what they have to have. This “Requirements Setting Practice” is seen in both the military and commercial world and has resulted in numerous ventures failing before they ever really had a chance to succeed.
History has shown that design decisions that are made very early in the ship design process impact approximately 75% of the total ship cost as shown in Figure 1. These design decisions by the naval architects are primarily driven by the requirements that were provided to them.
Requirements Trade-Off Analysis
Considering the significant impact that design requirements can have at a very early stage of the ship design process, the logical approach to maximizing the Cost/Risk/Benefit trade-off is to perform a robust “Requirements Trade-off Analysis” very early in a program’s life. By doing so, the impact that requirements have on all the risk areas is well understood. Thus, informed decisions can be made at a time when overall program success can be most readily assured. Such an approach to early stage ship design has been the cornerstone of CDI Corporation’s practices and procedures for several decades.
To efficiently do this, CDI developed a proprietary ship design synthesis process and engineering model that has been successfully used to help assess the cost of requirements, and the cost versus capability of new technologies, for naval and commercial surface ships. Assessing and understanding the cost of escalating requirements and technology options via “what if” games early in the design process has been the principal key to minimizing or eliminating the potential for spiraling cost over-runs.
Ship design, however, is one of the most complicated engineering tasks. There are a large number of systems involved, and the interactions between and among them are so complicated that the description and quantification of every aspect of them is extremely difficult, if not impossible. The larger and more elaborate a computer model is, the more difficult it is to use and the less reliable it will become. Even in the traditional detail design process, where every detail is sought, there are still margins on the weight, space and power to account for the accumulation of many small uncertainties, as well as the vagaries of individual and shipyard work practices. The “exact” answer is extremely difficult to achieve, if it exists at all.
The CDI ship design synthesis tool has been, and continues to be, a living and ever-evolving program. Even though it is built with all the expertise accumulated over more than 35 years, and has gone through extensive debugging and testing, minor problems are still possible and improvements are almost certain to be necessary. Additionally, modifications are inevitable in order to keep up with new technology development. Electric propulsion, for example, is undergoing significant evolution. Catamaran technology is evolving quickly as faster and bigger ships are introduced to the market. Trimarans are also gaining significant recognition. Fuel cell technology is advancing rapidly as well. Technology of this nature needs constant and careful data gathering and monitoring, and this will be vital to maintaining CDI’s ship design synthesis process as a premier technology assessment tool.
Ship Design Synthesis Engine
The ship design synthesis engine is where the simulation of the ship design process is carried out. It starts with an initial estimate of ship displacement. The geometry module generates a set of offsets to provide the necessary hull displacement. With the offset information, the structure module predicts the structural loads and, based upon the selected material properties and starting with a minimum plating gauge, it sizes the hull plating and structural scantlings to resist the predicted seaway loads and then sums up the structure weights. The resistance module then calculates the total drag. With the required thrust known (equal to drag), the program then calls for the propulsor module to design the propellers and/or waterjets. The shaft power required by the propulsor is then divided among each engine. The program then proceeds to design or select the engines, motors, generators and transmissions, and adds up all the propulsion machinery weights, deck area and volume.
The next step is to design the ship service electric plant and estimate the total electrical system weights, deck area and volume, which is accomplished in the electric plant module. If manning is not a direct input, the manning module will predict a complement mix based on the type and size of the ship, its various systems, and the automation level specified. The auxiliary module sizes all the auxiliary machinery and sums up their weight, deck area and volume for the auxiliary machinery group, while the outfit and furniture module assesses the total outfitting group weight, deck area and volume. Finally, various aspects of ship performance and cost are evaluated and the total fuel load is determined. Detailed weight updates are then made to establish the lightship weight, and then all the ship’s loads are calculated. Arrangements are then created to check for sufficient deck area and volume. Insufficient space results in the required volume being added to the ship’s superstructure.
Finally, a balance check is performed to determine if the weight used to establish the hull form matches the bottoms-up weight estimate just performed. This process is iterated around the spiral until two successive weight estimates are within 0.5 percent of each other. The Longitudinal Center of Gravity (LCG) and Vertical Center of Gravity (KG) are then estimated, based on the location of major systems. LCG is then matched to the Longitudinal Center of Buoyancy (LCB) and intact stability is calculated based on hull form offsets and KG, comparing area ratios and Metacentric Height (GM) to the corresponding stability standards to determine if the design has adequate intact stability. Cost analyses are then performed to determine acquisition and life-cycle cost. The final result is a balanced design that meets the specified mission requirements with sufficient internal volume for all required items. From here, the hull lines are developed and faired using other programs such as the NURBS modeling software “Rhinoceros”, and, along with an estimate of the radii of gyration in pitch, roll and yaw based on the mass distribution, all geometries and mass properties are ready to feed to other programs such as those for predicting seakeeping.
Unique Model: User Friendly Interface, too
The model is unique inasmuch as it uses, to whatever extent practical, algorithms derived from first-principle physics rather than from empirical data to characterize all major subsystems and their relationship to the overall ship. This approach was taken in order to ensure that new technologies were realistically modeled without being unduly biased by existing (and possibly outdated) trends in ship or ship-subsystem design.
The software features a user-friendly Excel interface and is capable of being used effectively by designers to assess the whole-ship impact of changes in technology and operational requirements. The code uses an object-oriented architecture and executes very quickly, even on a standard PC. The time taken to produce a single, balanced design is typically just a few seconds. Large parametric runs, where numerous combinations of parametric variations can be analyzed, can thus be executed in minutes. Effectively, the tool frees the designer from the tedious, iterative calculations of the naval architecture design spiral. This enables users to spend their effort assessing the results, observing trends, and determining the desired configuration.
The information contained in the parametric results is at least as important as the details of an optimized solution, and the intent is to provide the user with the information needed to make the appropriate choices so they can maximize their Cost/Risk/Benefit assessment.
About the Author:
Brian Forstell is Vice President and General Manager, Government Services, for CDI Corporation’s Global Engineering and Technology Solutions business. Forstell has earned a reputation as one of the industry’s leading innovators in the research, design and development of advanced marine vessels. Brian has a Bachelor of Science degree in Aerospace and Ocean Engineering from Virginia Tech University.
(As published in the 1Q edition of Maritime Professional - www.maritimeprofessional.com)
Read Reduce Boatbuilding Risk by Starting with Requirements in Pdf, Flash or Html5 edition of Q1 2013 Maritime Logistics Professional
Other stories from Q1 2013 issue
Content
- Reduce Boatbuilding Risk by Starting with Requirements page: 16
- Insights: Maritime Mergers and Acquisitions - All About Risk page: 20
- Risk Breakers: Henrik O. Madsen CEO, DNV page: 24
- Risk Breakers: Giuseppe Bono CEO, Fincantieri page: 26
- Risk Breakers: Craig Perciavalle President, Austal USA page: 28
- Risk Breakers: Anthony Chiarello, CEO, TOTE Inc. page: 30
- 100% Container Scanning in Ports: It is Possible page: 34
- CMA CGM - Showing the Way Forward page: 40
- The Riskiest Places to do Business – and Why page: 44
- LNG as the Ultimate Solution? Not so fast … page: 48
- Costa Concordia & Maritime Error Management page: 53