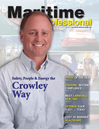
Optimize Performance via Data Analytics
Early adopters use performance monitoring and condition-based maintenance tools to cut costs, head off breakdowns, find efficiencies and ensure compliance.
The only thing harder than finding a needle in a haystack, is finding the sharpest points in a haystack full of needles, which is essentially the situation today on most vessels. Awash with hundreds or thousands of data sensors and data points, it’s the rare ship master or management team that can be certain they are culling the right information needed to cut costs and increase efficiencies to the extent possible in order to stretch razor thin operating budgets and goose tight profit margins.
Whether they know it or not, this is exactly the position that shipping companies find themselves in these days. All those sensors on all those systems – collecting and recording hundreds or thousands of data points a second, per day, each month – are building ever bigger digital piles, filling virtual bottomless cargo holds with shiny points of data. It’s just sitting there, an untapped resource going to waste instead of informing strategic business decisions and heading off expensive repairs and fines.
The problem isn’t collecting the data; it’s not even understanding what to do with it. It’s twofold, really. First, is just figuring out how to assess and analyze what you’ve got in order to pull out and focus on the salient bits that will enable ship company management and vessel masters to meet objectives – be it better fuel efficiency, lower fuel costs, longer equipment life cycles, lower maintenance and replacement costs or better environmental compliance – by making the right decisions in a timely manner.
That’s where ESRG Technology Group LLC of Virginia Beach, VA, comes in. Founded by former U.S. Navy engineers, it provides cloud-based, remote condition monitoring and data analytics to enable clients to address environmental, fuel, energy and maintenance issues at both the vessel and fleet level, while also providing ship managers with “actionable” information by automatically analyzing a broad swath of data using a variety of reporting and comparison tools and dashboards. ESRG’s OstiaEdge monitoring suite supports users on ship and on shore, across multiple platforms and server options. The company also provides custom application and consulting services.
The second problem lies in convincing a conservative industry, one often described as being in the Stone Age technologically, to leap forward more fully into the digital age and invest in the tools needed to sift through all that data. “Shipping is an old industry that has been around for thousands of years, with shipping companies that have been around for hundreds of years. It’s sometimes slow to jump on the next big thing. The marine industry in general has been burned by technology, hence they are very cautious. The required mindset to be able to leverage the cloud is more forward looking than that of the average ship owner or operator,” says Rob Bradenham, ESRG’s General Manager.
Current Maritime Market for Data Analytics
The market of ships well suited for remote monitoring or using the cloud to analyze data is about 30,000 out of 100,000 commercial class vessels globally. Bradenham expects to see the market double, if not triple, in the next 15 years or so, noting that the vast majority of new builds are prime candidates. The standard for new vessels is such that they have good sensoring on board, good automation and control systems and good communications structures.
In terms of dollar value, Bradenham said that if those 30,000 vessels were to adopt data analytics and remote monitoring, it would create a $20 billion value in terms of reductions in fuel consumption, downtime, maintenance expenses and environmental fines for those customers. He thinks that number could go to $50 billion by 2030. In terms of ESRG’s potential market - it is approximately $1 billion today, although the adoption rate is extremely low, “definitely less than 1%.”
For the handful of shipping companies to date that have decided to try navigation as an alternative to drowning in their rising ocean of data, it’s not hard to find examples of what the right kinds of decisions can get you. For example, monitoring can mean the difference between a successful voyage and coming to a dead stop somewhere in the middle of the deep blue because you didn’t know how to read the data points telling you over the last two weeks that an engine breakdown was imminent. (Heading off system failure is one of the two top reasons users are attracted to data analytics; cutting fuel costs and consumption is the other.)
Or, in the case of an offshore supply vessel, the decision to compare the difference in exhaust temperatures between cylinder banks at different operating modes. This led that company to make a simple, yet timely repair, which prevented a potential future failure that ESRG says could have cost $750,000 in repairs and downtime.
Then there’s the kind of decisions that enabled Bernhard Schulte Shipmanagement (BSM) to achieve a 2% to 5% reduction in fuel consumption three years into its five-vessel ESRG real-time data analytic installation. It doesn’t sound like much, but in actuality, it adds up to a lot more than chump change. As explained by project manager Romuald Wojtaszczyk, who held a variety of positions at BSM over a 24-year career, most recently as project manager for its ESRG install, before moving to Nordic Hamburg Shipmanagement to work on another ESRG project, “If consumption is 100 tons a day, and you are able to save 5%, and if the price is $500-$600 per ton, now you are saving $2,500 a day. If you calculate for the month, now it’s $75,000. Money like that cannot be ignored.”
That’s exactly the kind of fuel optimization and efficiencies-related savings that American Roll-on Roll-off Carrier (ARC) thinks is realistic, and hopes to achieve as it pilots ESRG’s OstiaEdge package on a single vessel. If all goes well, ARC will expand the software to the rest of its seven-vessel fleet later this year.
“We are looking for a nominal improvement in fuel consumption – 2% to 4%,’’ says Fred Finger, vice president & general manger, FLP and Vessel Operations at American Roll On Roll Off Carrier. “We’ll be happy if we get an incremental increase in vessel reliability and reduce off-service time by 5% to 10%. Then as we see what the capabilities [of the system] are, we’ll have a better idea of where to go beyond that. Right now, we are being very conservative in our expectations, but if the system works as we expect, our payback will be well less than a year.”
Condition-based maintenance is also paying off for companies like BSM. For example, Wojtaszczyk explains how something as simple as looking at the bearings on the shaft of an electrical motor can lead to savings. “The recommendation was to change them out every one and half years. We were finding that the bearings at that point were still very well conditioned. But if you take them out, you cannot put them back in. You have to install new ones.” Using CBM, BSM discovered it could wait two and half years before replacing the bearings – saving time and money.
And in cases where equipment maintenance schedules are mandated by class rules, users can take the historical data from CBM to the classification society and request that it extend the maintenance intervals for that piece of equipment. The opposite situation is true as well. Companies can bring historical records that show underperforming equipment to manufacturers in a bid to seed corrections, and also use those records to make new equipment or maintenance allocation choices for their fleet.
It can be hard to compare equipment use across a fleet with vessels of different ages, running different routes, dealing with different environmental issues. But data analytics can nonetheless ferret out trends that show some brands or types of equipment are more problematic than others. “So when you make plans for your next new builds, you say, ‘ok, we’ll eliminate this equipment because it costs more to maintain,’ ” says Wojtaszczyk.
The U.S. Navy – On Board from the Start
The potential for those kinds of results and more, are what captured the attention of the U.S. Navy, which has been working with ESRG since 2000, first to help develop the real-time analytics and monitoring software, and then to deploy the technology as the first user. Today, via its OstiaEdge platform, ESRG supports the remote condition monitoring of over 100 US Navy surface fleet ships, producing a wide array of performance reports for a range of vessels from aircraft carriers to container ships.
The predictive diagnostics capabilities of the software have proven their worth to the Navy on more than a few occasions. In one case, ESRG did an initial analysis of the equipment on a Navy destroyer preparing for an extended deployment. A generator was observed to have a similar anomaly during start-up as a recently failed generator for a sister ship. Combining the ESRG analytics and expert review with an in-person follow-up enabled the Navy to avoid suffering a catastrophic and expensive failure during deployment.
Environmental issues are big for everyone, and violations can mean stiff fines. Performance optimization and better equipment maintenance have trickle down impacts on environmental compliance, notes ARC’s Andy Anantharam, an independent technical consultant who owns Maritime Consultancy Services, Inc. “Our main focus initially was on fuel consumption. But with impending new sulphur emissions regulations, fuel cost becomes a critical operation element for us and we need to manage it as best we can. If you reduce fuel consumption, you are in turn restricting these emissions to the atmosphere and then of course, the same for carbon monoxide and green gas emissions,” he explained.
Data analytics not only helps ship owners catch potential issues early, but data automation and ship- to-shore exchanges of data and reports enables ship officers to provide on the spot documentation to port and regulatory agents.
Likewise, Nordic’s Wojtaszczyk sees the potential for providing similar historical data in another context – in the event of a collision or other big damage on board ship, the ability to take data from the ESRG system and later prove to the insurance company that what happened was not the result of a crew mistake, but perhaps an indication that something else went wrong. If it did, it will be in the data, he says.
For now, early adopters like the U.S. Navy, BSM, Nordic and ARC are the savvy exceptions to the prevailing industry mood. Given that many consider today’s economic environment to be one of the worst down cycles ever for shipping, the cautious, mostly shorter-term focus of many ship owners is not surprising. That said; getting a handle on big data and putting it to work is not only a strategic must, but more doable than they might think.
Data analytics: A Competitive Advantage
From a competitive standpoint, the ability to analyze data streams looking for patterns and early hints of problems, and the ability to do comparative analyzes – i.e., how does system A affect system B under X weather, speed and load levels – is critical to making the longer-term investments and business planning needed to enhance productivity and profitability.
Real-time analytics also allows users to “nowcast,” or ascertain probabilities about more current and ongoing events, enabling companies to further better optimize performance and find efficiencies. “The whole ideas is to give the ship’s crew, and via satellite transmission, the shore-based system, a condition-based program that will allow them to get really good, accurate information on the current condition of the equipment they operate - the main engine, generator and boiler – and pre-advance warnings of parameters that could give earlier warnings of the likelihood of any failure risks,” says ARC’s Anantharam.
In short, sophisticated analytics can substantially improve decision-making, minimize risks, and unearth valuable insights that would otherwise remain hidden, according to the McKinsey consultants who authored a July 2012 paper, “Why Big Data is the new competitive advantage,” published in the Ivey Business Journal.
Technical Obstacles to Installation
Of course, there are technological obstacles in general, and particular to shipping, that needs to be resolved before there is likely to be any mass adoption. These include communications costs, retrofitting aging ships, data storage and management, and the need in some cases to convert analog sensors to digital signals. One of the biggest causes for pause for many companies is the cost of satellite communications. Before you can analyze your data, you have to get it off the ship. But while ESRG’s Bradenham insists satellite costs have fallen to less than $1 per megabyte, he also says connectivity doesn’t have to be a sticking point. It’s all a matter of how often the shore side office wants to get data feeds. For some companies – a couple of times a day is sufficient. Where companies have broadband, and crew connectivity is considered a priority, it’s easier to send hourly or more frequent data streams.
ARC has broadband and sends updates every 2 minutes. “We are looking at having an essentially instantaneous import from the ship,” says Anantharam. ARC has ambitious plans for taking advantage of its data stream. In addition to creating a proactive environment for maintaining equipment, from a risk management standpoint, “the ability to be able to manage and document activity, such as emissions monitoring, is something we’ve always wanted to do,” says Finger.
The kind of documentation that Finger is talking about is very important, above and beyond maintenance and optimization issues, says Wojtaszczyk. In addition to helping document insurance claims and environmental issues, he says those reports can be used both to get charterer agreement to route or speed changes, as well as to sell them on claims of more efficient, lower fuel cost service.
Retrofitting may actually be a bigger issue for companies to get their heads around. New builds, like the two ships Nordic has under construction, will come pre-prepped with the necessary communications structure to handle data streams. But many ships in today’s fleet are more apt to fall in the 10- to 20-year-old range, and lack the updates needed to take full advantage of monitoring and analysis packages like OstiaEdge.
At ARC, for instance, it was necessary to upgrade the shipboard alarm monitoring system to add serial port communications in order to use the OstiaEdge package. It took 6 months to get the system delivered, and four days in port to get it installed, during which ESRG installed its software. “Our ships are 15 to 20 years old. The equipment and alarm systems are not the most current, so we had to do some upgrading there,” says ARC’s Finger.
But first, they had ESRG come in and do a survey of their equipment and systems to analyze what they had, and what additional inputs (sensors) they’ll need versus what is there today, based on the kinds of reports they want, and how they want to manipulate the data. ”We have had to do several upgrades to take full advantage of the program,” adds Finger.
Still, one of the reasons ARC and Wojtaszczyk choose OstiaEdge is because of its flexibility, saying they are finding it relatively easy to use even with older systems and ships, in part because the OstiaEdge platform does not require replacement of current systems, but rather integrates existing data into its system.
However, ships with analog sensors will find they have to upgrade to digital to work with OstiaEdge, says Wojtaszczyk, which he notes, is significantly more expensive than having it installed as part of a new build. “But ESRG is the champion of modifications,” he adds. Retrofitting BSM’s first ship took three months, after that, most changes were installed in two weeks, while the ESRG software was installed and synchronized with ABS classification software, in three days.
Nordic is launching its pilot with new builds, but plans to expand the application to the rest of its fleet of vessels, the oldest of which was built in 2008.
Besides their willingness to bring their operations into the digital era, one of the things that stands out about these early adopters is that they are so certain of the ROI of real-time data analysis that they are unfazed by retrofitting issues and costs. It’s the same for communications costs. These users simply see plenty of evidence, in and out of their market sector, that control and analysis of their data is going to be the key to long-term success on so many levels. And they don’t think most shipping companies will be able to hold out for long.
From an international perspective, Wojtaszczyk believes the market for data analytics will be forced by charterers. “If they have the choice, they want you to have the tools on board to operate the vessel in the best possible way for them and the owners. If you can offer the ship with the lower fuel cost, and you can prove it using ESRG’s data, it absolutely helps a lot during contract negotiations.”
In the U.S., the drive is going to be more primal, believes Finger. “Depending on mortgage and types of ships, I don’t think all will have to do it. However, if you are a U.S.-flagged vessel, with the cost structure we have here, the savings to be had are larger than what it might be for someone operating a non-U.S.-flagged ship. Our costs for crew and daily operating expenses are higher, so initial savings will be higher.”
“The bottom line is improved performance, better risk management, and the ability to unearth insights that would otherwise remain hidden. As the price of sensors, communications devices, and analytic software continues to fall, more and more companies will be joining this managerial revolution,” predicts the McKinsey report. It’s not hard to see why. The ROI to be had, and the breadth and speed of that return on investment across the many layers of a shipping operation, should prove irresistible to anyone paying attention to the bottom line and all the factors affecting that number.
(As published in the 1Q 2014 edition of Maritime Professional - www.maritimeprofessional.com)
Read Optimize Performance via Data Analytics in Pdf, Flash or Html5 edition of Q1 2014 Maritime Logistics Professional
Other stories from Q1 2014 issue
Content
- Energy: Moving it & Using it page: 8
- Energy Growth Fuels Transactions page: 10
- Cruising Beyond Compliance page: 16
- Catching up with Vice Adm. William Burke (Ret.) page: 20
- The Changing Face of Piracy page: 24
- Registries: Strength in Numbers page: 28
- The Crowley Way page: 32
- Crowley’s “Commitment” page: 38
- Optimize Performance via Data Analytics page: 50
- MLC Mandated Medical Management for Mariners page: 55
- Seall Passage Planner Strengthened with AIS Feature page: 56
- Hobart Stick Electrode Improves Control and Quality page: 56
- SCI Simulator Offers One-on-One Training page: 56
- Regulatory Profile: William P. Doyle, Commissioner of the Federal Maritime Commission page: 58