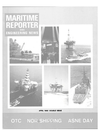
Gulf Coast Shipyards
A Facilities Review ALUMINUM BOATS Aluminum Boats, Inc., is a new shipyard in south Louisiana that is rapidly earning a reputation for high-quality construction and repair of aluminum boats at reasonable prices. As the name indicates, the shipyard specializes in the construction and repair of a wide variety of all-aluminum vessels.
Located at Crown Point, La., close to the Gulf of Mexico and New Orleans, the shipyard has already built and delivered eight new vessels, and modified four others since its establishment in 1983. Three additional boats are under construction now for 1985 delivery.
Aluminum Boats, Inc., set a record recently by building and delivering two 85-foot crew/utility boats within 12 weeks. Salvador J.
Guarino, president of the company said that quick deliveries such as these are indeed a challenge, but they are welcomed as they have proven his shipyard's ability to respond quickly to customer needs.
Included in Aluminum Boats' new construction deliveries are: one 115-foot crew/utility boat; three 85- foot crew/utility boats; one 78-foot, and one 65-foot crew/utility vessel; and two 110-foot security vessels. In addition, the shipyard has added a 12-foot mid-body section to a 100- foot crewboat for additional tankage, and converted two 77-foot crewboats and one 100-foot crewboat to ferries for use in Boston harbor.
Aluminum Boats, Inc., is currently building three boats; a 150-passenger, 87-foot whalewatch excursion boat for use olf Provincetown, Mass; a 110-foot crew/utility boat for use in the Middle East; and a 100-passenger, 95-foot, triple-screw, crew/utility vessel, also for use in the Middle East.
Mr. Guarino pointed out that his vessels carry the designation "crew/utility" as those so designated are outfitted with tanks and other equipment which extend their use beyond the water taxi mode.
Aluminum Boats, Inc., also operates an efficient, rapid response spare parts and replacement parts program which is based on Mr.
Guarino's more than 30 years' experience as a marine purchasing agent. He served as chief purchasing agent for a major shipyard for 16 years and was president of a marine and industrial supply company. Mr.
Guarino said his company welcomes inquiries from clients and non-clients alike.
The shipyard occupies the site of the former Camcraft, Inc., on the Intracoastal Canal. It is equipped with covered manufacturing facilities, high-capacity overhead cranes, and all of the equipment required for high quality production.
"We received another distinct advantage by locating at the former Camcraft facility," said Mr. Guarino.
"Most of our shipbuilders were employed by that company, and they are highly trained and skilled craftsmen. They take great pride in the quality of their work, and I think we build the best aluminum boat you can buy." Principal officers are Salvador J. Guarino, president, and Ken Deshotel, CPA, secretary and treasurer.
Circle 61 on Reader Service Card AVONDALE SHIPYARDS Avondale Shipyards, Inc. near New Orleans is continuing with the construction and conversion of six vessels, including the newbuilding of two T-A0-187 Class fleet oilers for the U.S. Navy, two T-5 forebodies under subcontract from American Ship Building of Tampa, and the conversion of two SL-7 containerships into T-AKR service for the Military Sealift Command. In addition, the yard is constructing three large, gas-turbine-driven, modularized compressor skids for industrial service. All work is either on or ahead of schedule.
Two additional T-A0-187 Class ships and three dock landing ships of the LSD-41 Class are also under contract, and construction will start late this year and in 1986. Avondale also has an option, to be exercised by the Navy when funding becomes available, for two additional LSD- 41s. Areas of future interest include the lead ships of the AOE-6 and AE- 36 Classes, as well as the follow-on ships of the LSD-1 and DDG-51 Classes.
Avondale is also continuing its program of productivity and facility improvement, resulting in a continuation and increase in the cost savings that have been previously experienced.
The yard initiated the transfer of Japanese technology in late 1979. The development of this technology, which has resulted in dramatic savings, is continuing with the further refinement of the system to adapt to the domestic environment, increased use of computers for design, construction, and management, and to more effectively accommodate the greater complexity of Naval vessels.
Engineering improvements include the more effective application of modularization and packaging, improvement and more extensive use of standards, the commercialization of non-mission-oriented Military Specifications, continued refinement of CAD/CAM, and the improved application of the yard's advanced material control system, COPICS.
Improvements in logistic support, cost/schedule control, quality assurance, and other Naval shipbuilding disciplines continue.
New facility improvements include a lifting and turning frame with a lift capacity of 250 tons to handle and turn over large pre-outfitting assemblies, three new 130- ton revolving cranes, the switch to two numerically controlled plasma arc burning machines, and a new beam fabrication line to save structural weight and cost.
The award of contracts and the progress of these contracts is proceeding well, but added work is required if the yard is to maintain economical levels of employment and properly utilize the continuing investment in facilities and improved technology.
Avondale maintains seven drydocks for major conversions, major repairs, and the quick turnaround of offshore oil and inland waterways vessels. The largest dock is capable of lifting 81,000 tons. This dock is 900 feet long on the platform, with 220 feet between wing walls, making it capable of lifting the largest vessels, including semisubmersible rigs, that can transit the Mississippi Riv- er. Up to 37 feet of water can be obtained over the blocks.
The other major dock is a Panamax floating unit with a lift capacity of 20,000 tons and a length over the blocks of 656 feet. Both docks are U.S. Navy certified. All repair services are offered, including the rubber lining of tanks and 600-ton heavy-lift services. Full new construction engineering support services are available for repair clients Circle 62 on Reader Service Card BENDER Despite the low level of activity in the marine industry, Bender Shipbuilding & Repair Company of Mobile, Ala., continues to maintain its position as one of the nation's leading builders of the new breed of trawler/processor vessels. These boats catch, clean, freeze, and package their fish within minutes, and deliver to dockside the freshest possible ready-for-market product.
Recent deliveries include two 115- foot trawlers for Pacific Enterprise of Seattle, and two 133-foot trawler/ processors for Pete Njarvik, also of Seattle. Two additional trawler/ processors are currently under construction.
Other deliveries include the 192- foot cruise vessel Pilgrim Belle for Coastwise Cruise Lines of Hyannis Port, Mass., and a 98-foot scalloper for Jakob J. and Jarry Shervo of New Bedford, Mass.
Improvement and expansion of Bender's ship-repair facilities include the recent addition of a floating drydock with a lifting capacity of 18,000 tons. The new drydock will enable the Mobile yard to accommodate an even larger capacity of ships that are expected to pass through Mobile with the recent opening of t h e Tennessee-Tombigbee Waterway.
Currently at Bender is the Patroit State (ex Santa Mercedes) that is being converted into a training ship for use by the Massachusetts Maritime Academy under a $5,643,778 contract awarded by the Maritime administration. Also at the yard are two Tidewater Marine offshore supply vessels that are getting new 16- foot sections to expand their cargocarrying capacity.
With an aggresive sales approach, Bender plans to promptly meet the repair and overhaul needs of the maritime industry, and to deliver state-of-the-art steel vessels that can compete successfully in today's market.
For more information, Circle 82 on Reader Service Card BLUE STREAK INDUSTRIES Anyone driving near, or flying over, the Blue Streak Industries, Inc., shipyard would be impressed by the 12 tall steel legs or columns piercing the sky. The legs are attached to four self-elevating, selfpropelled lift boats which are currently at the facility for annual inspections and overhaul.
The hydraulically operated legs are lowered to the ocean floor making the boat a stable platform from which a variety of work is performed.
A closer look will also reveal nine additional huge legs being fabricated for three new lift boats that are also under construction at the Pearlington, Miss., shipyard.
At water's edge crews are install- ing 260 feet of concrete bulkhead, and others are working on a new line of lightweight, high-lift-capacity marine cranes which will soon be introduced to the marketplace.
The shipyard occupies an 18-acre site and is staffed by 122 shipbuilders who can produce in excess of one vessel per month. As the pilothouses and cabins of lift boats are made of aluminum, and the hulls are constructed of steel, the yard has the necessary equipment and facilities for the construction and repair of both steel and aluminum vessels.
Blue Streak Industries was established in January 1978, at Chalmette, La., by Dennis L. Good, president and owner. The yard began building a variety of aluminum and steel workboats. As the demand for larger lift boats increased, the company outgrew its suburban New Orleans facility and moved its lift boat production to a new, larger site at Pearlington, Miss. In 1979, Mr.
Good decided to specialize in lift boat construction and maintenance, and all activities were shifted to the Mississippi operation. It is located on the East Pearl River which provides quick, easy access to the nearby Gulf of Mexico.
Today Blue Streak Industries, Inc., is the nation's largest builder of self-elevating, self-propelled lift boats. The company offers lift boats with legs from 75 feet to 200 feet with crane capacities of 10 tons to 100 tons. Quarters and galley facilities for 14 to 42 people can be provided, and electrical generation capacities range from 40 kw to 300 kw.
The boats are designed and built at Blue Streak Industries, Inc., P.O.
Box 92, Pearlington, Miss. 39572.
The phone number is (601) 533- 7892.
Blue Streak also has manufacturing license agreements with Sing Koon Seng (PTE) Limited of Singapore, and Montreal Engenharie S.
A. of Rio De Janeiro.
Circle 63 on Reader Service Card BOLLINGER Thirty-eight years of experience provided much of the groundwork toward growth patterns for Bollinger Machine Shop & Shipyard, Inc.
in Lockport, La. The New Construction Division there is busy on a government WPB contract that should take some 33 months to complete.
The first of the U.S. Coast Guard's new 110-foot patrol boats is expected to be delivered on August 4 this year, and at 45-day intervals thereafter.
The contract awarded August 8, 1984 calls for 15 patrol boats, based on the internationally known 110- foot Vosper-Thornycroft design.
The cutter's superstructure and living areas have been redesigned to meet Coast Guard needs. Its operating capability, endurance, and habitability will vastly exceed that of any 82- or 95-foot patrol boat currently employed by the Coast Guard.
Improvements in the accommodations include the use of sounddeadening and isolation-dampening treatments, expanded deck space, and more crew storage capacity. An active-fin roll stabilization system is used to improve seakeeping characteristics.
The value of the contract to Bollinger was some $73,000,000.
A new addition to Bollinger's Larose Division is a 3,500-ton drydock that was officially operative on No- vember 16, 1984. Christened the Big D after chairman of the board Donald G. Bollinger, the new dock is 200 feet long with an 18-foot draft, and measures 81 feet between the wing walls.
Special features of the new dock include ten 4,000-gpm pumps, four 1,000-gpm stripping pumps, shore power hook-ups, floodlights, air-operated valves for submerging, and a 57-foot trolley system that allows the dock to be moved out into the slip and to submerge to haul up 300- foot-long vessels. With this latest addition, Bollinger-Larose now has three drydocks to offer to its customers.
The company's Lockport Marine Repair Division has six ways to handle haul-ups; the latest, No. 6 ways, can handle supply boats of up to 165 feet in length. The current project on that ways is a 165-foot supply belonging to Cheramie Brothers that is being lengthened to 186 feet.
A 21-foot midbody to carry liquid mud and calcium chloride is being prefabbed and will be installed forward of the engine room. A bow thruster and two 500-cubic-foot bulk mud tanks are also being installed.
For more information, Circle 83 on Reader Service Card CONRAD INDUSTRIES In continuous operation since its founding in 1948, Conrad Industries, Inc. is located at the junction of the Intercoastal Canal and the Atchafalaya River in Morgan City, La. The yard has river frontage of more than 500 feet, plus a dredged basin 320 by 100 feet that is used for dockside repairs as well as loading and unloading. The entire area is bulkheaded, and compacted and shelled for heavy traffic. Approximately 90 percent of the 5.4-acre yard is concreted. ' Conrad specializes in boat repairs, and in barge and miscellaneous construction.
Servicing the boat repairs are two floating drydocks, each with a lifting capacity of 1,500 tons and dimensions of 120 by 70 feet, and two 120- by 52-foot drydocks rated at 900 tons each. All are new and were built at the yard.
Two crawler cranes of 50- and 40- ton capacity, and a 20-ton cherry picker are permanently on site; heavy-lift equipment is readily available. Services for propeller reconditioning, machining, electrical, carpentry, and other work are provided.
Sandblasting and painting are performed with ample and convenient equipment. Three 40,000- pound sand hoppers are located near the drydocks, and 2,400 cubic feet of air per minute is piped throughout the yard.
New construction is done indoors in two buildings. One is 360 feet long, 100 feet wide, and 45 feet high; the other is 200 by 80 by 28 feet.
Overhead cranes handle the materials needed for the variety of barges, drydocks, and miscellaneous vessels built here. More than 100 welding machines of various types are available, as well as special tools for greater efficiency.
Circle 64 on Reader Service Card GRETNA MACHINE Gretna Machine & Iron Works, Inc. is a wholly owned subsidiary of Trinity Industries of Dallas specializing in barge construction, repair, and gas-freeing, as well as steel fabrication.
The Harvey, La., yard has been in business for 25 years, and normally has a work force of approximately 350, manning two shifts per day. The facility covers 47 acres and includes two barge graving docks, outside platen area, and steel fabrication and pipe shop. Two galvenizing plants are located nearby.
The new-construction graving dock is 600 feet long and 100 feet wide. It is served by a 50-ton portal crane traveling the length of the dock and a pre-fabrication platen area. A graving dock measuring 300 by 100 feet is used primarily for repairing river barges. The yard has a complete gas-freeing plant, with steaming, Butterworthing, and flaring facilities. The fabrication shop includes automatic welding and burning equipment, plate shear, press brake, and pipe-bending equipment.
Gretna's new-construction work has been confined mainly to large oceangoing barges, many of them designed by the yard's in-house naval architects and engineers. This leads to less expensive construction due to incorporating many in-house standards into the designs. The yard has also built highway bridge caissons.
Repair and gas-freeing work concentrates on river vessels, due to the yard's strategic location on the Harvey Canal near the meeting of the Mississippi River and the Intracoastal Canal.
Circle 65 on Reader Service Card HALTER MARINE Halter Marine is operating six shipyards in the U.S. Gulf Coast area. When combined, the current workload at all six yards makes Halter a leader on the Gulf Coast.
In addition, Halter has supplemented its normal oil field supply vessel and crewboat business with a sizeable quantity of work for the military. Halter is building a solid Booster recovery vessel for Lockheed and the Air Force at its Moss Point Yard, and it recently delivered a 65-foot utility boat for the U.S. Navy from its Chalmette Yard.
The Chickasaw yard completed a jumboizing of the Moana Wave for the University of Hawaii who operate the vessel for the U.S. Navy, and the Industrial Canal Facility is heavily involved in the WPB Program by cutting all the steel and building the aluminum main decks for the patrol boat builder, Bollinger Shipyards of Lockport, La.
Innovative tugboats are presently under construction at Halter's Lockport facility for Otto Candies, and the company has under construction, for stock, a large supply vessel at its Moss Point yard. Two stock crewboats are under construction at the Chalmette yard, in addition to present contract work underway.
Jack Edwards, president of Halter Marine, told his management team that the company is in an excellent position to be competitive on any vessel of a size Halter can build. He told of plans to further consolidate the facilities and mentioned that Bell-Halter, the company jointly owned by Halter and Bell Aerospace have agreed to a lease on Halter's Chef yard. Halter's corporate office, presently located at the chief yard will move to new quarters in East New Orleans.
Halter has its own Engineering Department, giving Halter the ability to design a vessel to the owner's requirements, however unique. In addition, changes to the vessel to meet changing market conditions or owner's preferences as construction progresses may be accomplished with the minimum of disruption to the end delivery of the vessel. Mr.
Edwards commented that an inhouse Engineering Department does not mean that the company has a not-invented-here attitude.
Halter has an excellent history of building to other qualified designs.
Halter Marine is owned by Trinity Industries, a large well financed company with a wide range of products.
MOSS POINT Halter Marine's Moss Point yard is located five miles above Pascagoula on the Escatawpa River. This yard has been owned by Halter Marine for over 20 years. To date 207 new vessels have been delivered from this facility. In a single contract of nineteen 200-foot vessels, the rate of delivery averaged 2% weeks between completions and in some cases as many as two vessels were launched in a single week.
Halter's Moss Point facility has cranes with capacities to 175 tons.
Moss Point also has a complete pipe shop equipped with automatic pipe bending equipment that serves their needs, as well as all other Halter shipyards. A completely equipped machine shop can take care of all customers' needs on the spot.
Recently Moss Point delivered a 180-foot supply boat for State Boat that had sunk in the Gulf and was salvaged. This vessel was further damaged during salvage operations and had to be completely rebuilt.
CHICKASAW Halter Marine's Chickasaw shipyard, located just north of Mobile Bay on the Chickasaw River, is Halter's largest shipyard. While the Chickasaw yard specializes in repair and conversion work, it has delivered many new construction vessels, such as the large Cat Tugs, supply boats and lift boats. Chickasaw has a drydock that has a lift capacity of 4,000-dwt that measures 160 feet long with 120-feet between wing walls. It is completely self-contained and is powered by two 450- kw generators.
This yard has the capability of translating vessels from the water to the shore for major conversion or extended repair.
Halter recently signed a contract with Nicor for two 200-foot anchorhandling tug/supply boats. The contract required the vessels to be jumboized by the addition of a 16-foot midbody. Both vessels were moved from the drydock onto land where they were cut in half to receive the midbodies, releasing the drydock to serve additional customers. Halter Marine's Moss Point yard fabricated both midbodies for this job.
Halter's Chickasaw facility has two 300-ton cranes, one 100-ton plus others with smaller capacities. It has a complete fabrication shop, electric shop, machine shop and pipe shop.
This facility also has more than 2,000 feet of wet dock space.
INDUSTRIAL CANAL As further support of the Halter facilities the Halter Industrial Canal facility in New Orleans is equipped with Plazma Arch Numerically controlled burning machines that are capable of cutting all the steel and aluminum needs for Halter yards with precision quality.
CHALMETTE The Halter Chalmette facility lo- cated in Chalmette, La. specializes in the construction of both steel and aluminum high-speed craft such as crewboats, patrol vessels, pilot boats, ferries, mooring launches, yachts and survey launches. New construction takes place in a covered building in the facility. A 100- ton Travelift handles the translation of vessels throughout the yard plus launching and retrieval.
The Chalmette Yard also handles drydocking and repair.
The yard recently delivered three 101-foot crewboats to a customer in the Far East and is presently building a fourth 101-foot for the same client. A 65-foot utility boat was also recently delivered to the U.S.
Navy. A 112 and 101-foot aluminum crewboat are presently under construction for stock.
LOCKPORT The Halter Lockport facility was opened in 1966. Lockport specializes in the construction of supply vessels, tugs, river push boats and barges. The yard is also capable of handling repair work and shipboard modifications. A fully equipped machine shop supports all of the Halter facilities and customers with machine work and repair support.
The yard is presently building two innovative offshore tugs for a local client. The vessels incorporate a triple-screw arrangement comprised of one conventional propeller drive and two fully azimuthing propellers for maximum power and maneuverability.
A number of offshore supply vessels are nearing completion at the Lockport facility.
For complete information and literature detailing Halter's services, Circle 66 on Reader Service Card INGALLS Ingalls Shipbuilding division of Litton in Pascagoula, Miss., has been building Navy ships since 1938. The company's east bank facility produced troopships in World War II, as well as escort aircraft carriers, submarine tenders, and net layers. After the war Ingalls built amphibious assault ships, Forrest Sherman Class destroyers, and beginning in the late 1950s, nuclearpowered attack submarines.
In the late 1960s, Litton and the State of Mississippi joined forces to build an entirely new, modern shipyard— the only new shipyard that has been built in the U.S. since WWII. This 611-acre facility was built on a new concept pioneered by Ingalls in the 1970s, that of modular construction. This system has since been applied to the construction of Spruance Class destroyers, Tarawa Class amphibious assault ships, Kidd Class guided-missile destroyers, and is currently being applied to the construction of Ticonderoga Class Aegis guided-missile cruisers and Wasp (LHD-L), first in a new class of multipurpose amphibious assault ships.
Ingalls has also established a reputation in the surface ship overhaul business. Since 1982, the yard has overhauled six Spruance Class destroyers, work that normally requires nine months of intense effort, an average of 33 days ahead of schedule. Two additional Spruance overhauls will be completed this year.
Ingalls facilities have also proven adaptable to a variety of products and services requiring heavy manu- facturing, especially in the areas of building and repairing offshore drilling rigs and support structures.
The company's design, engineering, and technical divisions offer a versatility of superior design services unmatched in a production facility.
Ingalls has an ongoing capital investment and improvement program to continually upgrade its facilities to utilize the latest available technology.
The use of computer technology for ship design and production, especially computer-assisted design and manufacturing (CAD/CAM), has unlimited potential for improving shipyard productivity—from engineering to production shops to the building bays and outfitting docks. Ingalls installed its first CAD/CAM system' in 1979, and is now increasing production significantly over manual drawing.
This equipment has three-dimensional capability, allowing engineers and draftsmen to detect system interferences on the drawing board, not on the ship where they are costly and time-consuming. Ingalls is also linking computer design with automated fabrication equipment already in place in steel, aluminum, pipe, and sheetmetal shops, further increasing productivity.
Circle 67 on Reader Service Card KOCH-ELLIS Further expansion for Koch-Ellis Barge and Ship Service has been completed. A family-owned marine company, Koch-Ellis has worked out of tbe New Orleans area for more than 50 years. Ship bunkering was its main concern until Harriet Harrison became president of the company in 1979. Since that time, Koch-Ellis has slowly but steadily increased its services.
Besides adding a new ship-bunkering office in Houston in 1981, the company's main direction in expansion has been to supply complete service facilities for both inland and oceangoing barges and ships. Koch- Ellis in 1982 acquired Barge and River Service, its neighbor on mile 104 of the Mississippi River, and has continually upgraded that facility since then.
The multi-function service area has a complete wet dock repair staff able to handle everything from electrical problems to above-water damage repairs. Koch-Ellis specializes in mid-period and alternate internal inspections.
There are two modern cleaning and gas-freeing plants, and a large inland barge steaming operation that can steam up to 14 barges at a time. Last year the company complemented this by adding a new liquid bulk carrier cleaning and gasfreeing facility.
Koch-Ellis is a pioneer in aerobic digesting systems for on-site treatment of wash water. It has worked closely with the Environmental Protection agency to help set industry waste disposal standards.
This year Koch-Ellis moved into new expanded offices at its Westwego, La., plant location. The company plans to continue its growth in order to handle the over-changing demands of the maritime industry.
Circle 68 on Reader Service Card LEEVAC Specialized vessel construction, predominantly conversion work, is the real area of activity for Gulf Coast shipbuilders, according to LEEVAC Shipyards of Jennings, La., a division of LEEVAC Corporation of Morgan City.
Shipyard sales manager Charles Burrell said, "we know the market in general is not great, but the level of conversion work we're involved with is consistently high." LEEVAC, well known for its design and engineering expertise, is no newcomer to the specialty construction and conversion market. Customers such as Geophysical Services Inc., who have seen the yard's capabilities in specialized seismic construction of new vessels, return to them for conversion of supply boats or other vessels in their boat operator's fleet.
Geophysical's vessel Patrick E.
Haggerty and the soon to be deliv- ered Kenda are examples of LEEVAC's new construction for the seismic industry. Rare though it may be today, this new construction is happening because of rapid technical advances in the seismic industry, according to Mr. Burrell.
LEEVAC's conversion projects that have gained recent attention include the transformation of a basic 190-foot supply boat, the Cal Diver I, into a saturation diving vessel for Cal Dive International.
Unique among vessels of its type operating in the Gulf of Mexico, this conversion involved the construction of a special moon pool located amidship through which the diving bell is lowered, and a new, totally enclosed operations system.
"Our research shows that the level of conversion will continue to increase because of new technology in the seismic and diving industries, and most importantly, the impending surge in the deep-water market," said Mr. Burrell.
Among projects currently under way at LEEVAC is the conversion of a 150-foot supply boat, the Seis Surveyor, to a seismic vessel for Survey Boats, Inc. of Paterson, La., a division of John E. Chance & Associates of Lafayette.
Circle 69 on Reader Service Card MAIN IRON WORKS Founded in 1948, Main Iron Works, Inc. (MIW) of Houma, La., now has facilities for construction of new vessels up to 250 feet in length.
Drydocking and a full range of repair services are also available, including sandblasting, painting, and a complete machine shop facility.
With more than 30 years of experience in designing vessels for towing, shipdocking, and oilfield services, MlW is ready for the new challenges of the future. With more than 375 vessels delivered to date, many of them innovative and well ahead of their time, the yard recently delivered the Mabel Colle, one of the most modern shipdocking and general towing tugs on the Gulf Coast, to Colle Towing Company of Pascagoula, Miss. This 85-foot twinscrew vessel is powered by GM Electro- Motive Division EMD-12-645 diesels with a total output of 4,000 bhp, driving Ulstein H900 "Z" Drives with 72-inch bronze propellers in nozzles.
Circle 70 on Reader Service Card MCDERMOTT McDermott Shipyards, a division of the offshore construction giant McDermott Incorporated, has facilities at three locations on the Gulf of Mexico—Morgan City and New Iberia, La., and Gulfport, Miss.
Each yard has under-roof construc- tion, automated drafting, NC burning, and modular construction as main components of its shipbuilding system. These yards are modern facilities capable of new construction, converting or upgrading existing vessels, and complete marine repairs.
Five drydocks are available, ranging in size from 1,500 to 5,000 tons capacity. The 5,000-ton dock, located at Morgan City along with a 3,300-ton unit, is 250 feet long with 110 feet between wingwalls. Two drydocks are located in New Iberia— a 3,300-ton facility 180 feet long and 80 feet between wingwalls, and a 1,500-ton dock measuring 160 by 65 feet.
McDermott's Gulfport yard was the latest to undergo expansion, from 10 to 84 acres, with more than five acres under-roof. Building ways are capable of launching vessels of up to 40,000 dwt. Output from this yard includes coastal and oceangoing petroleum, deck, and bulk cargo barges up to 600 feet long.
In addition to drydocking, all McDermott yards overhaul marine engines, repair and replace deck machinery, machine new tailshafts, build rudders, and crop and renew hull plating. McDermott is one of the few yards in the country aproved by the American Bureau of Shipping to repair shafts worn to under-minimum diameter.
McDermott recently delivered two unique, self-loading/unloading container barges to Matson Navigation Company of San Francisco.
Named the Haleakala and Mauna Loa, the barges were towed in tandem to Honolulu where the container- handling cranes were installed.
They are now operating in Matson's feeder service betwen Honolulu and other Hawaiian ports.
Circle 71 on Reader Service Card MOSS POINT MARINE Moss Point Marine, Inc. is currently building one 181-foot supply vessel, two 92-foot tugs, one 800- passenger paddlewheel/excursion boat, converting a 383-foot T-2 tanker to a hopper barge, refurbishing a 68-foot shrimp boat, and constructing twenty-six 110-foot lighter barges for the U. S. Navy. The first two Navy barges were delivered recently to California approximately three months ahead of schedule.
Founded in 1980, Moss Point Marine has already delivered 61 vessels, which strengthens its "New American Leader" slogan.
Moss Point recently delivered the 219-foot freezer/stern trawler, Amfish, reported to be the largest U. S.—built vessel of her type to fish off the U. S. East Coast. The Amfish contains approximately 38,000 cubic feet of refrigerated storage space and is capable of processing and freezing up to 40 tons of fish products per day The shipyard had just acquired a 2,000-ton floating drydock which is 160 feet long and 60 feet between its 17-foot wingwalls. Constructed in 1980, the drydock has a built-in generation capacity capable of operating the dock in any location.
Moss Point Marine is located on the East Pascagoula River north of Pascagoula, Miss., which provides easy access to the Gulf of Mexico.
The shipyard occupies a 30-acre site and has 900 feet of sheet pile bulkhead on the river. One hundred and fifty additional acres are available if further expansions is needed. The yard has the usual complement of shipyard crafts and skills but an unusually low employee turnover rate. Many of Moss Point's shipbuilders joined when the shipyard was formed and have made a commitment to remain there for a career.
"That kind of dedication by highly skilled people is one of the principle reasons for our success," said John Dane III. president of the yard.
Moss Point Marine, Inc., is a complete shipyard with pipe, carpentry, and electrical shops, a large fabrication building, warehouse, three 150- ton crawler cranes, and various "cherry pickers" and other equipment.
Specialized equipment is readily available from nearby specialists such as propeller and machine shops that are located within 10 minutes of the shipyard.
In addition to John Dane III, president, other principal owners and officers are Burnice M. Havard, vice-president, and John Dane Jr., secretary-treasurer.
The yard's address is Box 1310, Escatawpa, Miss. 39552, and the telephone number is (601) 475- 6885.
Circle 72 on Reader Service Card NATIONAL MARINE SERVICE National Marine Service Incorporated, headquartered in St. Louis, currently services the inland waterway system and the Gulf Coast with three full-service shipyards— at Harvey (New Orleans), La., and at Hartford and Grafton, 111., on the Upper Mississippi River.
The Harvey yard, formerly Wall Shipyard, was acquired by NMS in 1980. Since then, improvements for the yard include: lengthening of the existing drydocks; construction of a new office building, engine shop, and wheel shop; purchase of a press brake; and increased inventory of diesel engine parts.
A new 160-foot drydock was installed soon after the Harvey yard was acquired, the sixth at the facility.
Other work undertaken by National Marine included dredging of the bayou channel, rehabilitation bulkheads, modification of two existing drydocks to handle larger barges and boats, and the improvement of gas-freezing facilities.
Circle 73 on Reader Service Card NEWPARK Newpark Shipbuilding & Repair, Inc., conveniently located on the Houston Ship Channel, combines experienced workmanship and knowledgeable management to provide quality work in the time frame required at a competitive price.
Inland and offshore vessels built at the Houston yard now travel the waterways from Alaska to the Amazon River, from the North sea to the Coast of Africa. New-construction capabilities include high-pressure cylindrical tank barges; customized vessels including shallow-water, self-propelled seismic craft; offshore, high-load deck barges; and inland, double-skin tank barges, to name a few.
Vessels can be lengthened, shortened, or have completely new prefabricated sections installed. Supply vessels have been converted to an- chor-handling and seismic service.
The company is founded on servicing the repair and maintenance needs of its customers, as well as overcoming specific design problems.
Its resident naval architect has more than 40 years of experience.
The Newpark yard covers about 25 acres, and includes the following facilities: 3,000-ton drydock, 220 feet long with 88 feet between wing walls; 1,500-ton drydock, 150 feet long and 76 feet wide; 1,250-ton drydock, 130 by 76 feet; two marine railways; a drydock/rail transfer system; 1,600 feet of water frontage; and 20,000 square feet of fabrication shops with automatic welding and burning equipment.
The yard offers all types of underwater repairs, from steel renewals to propeller reconditioning and ABSapproved tailshaft buildup. The electrical department has a staff of trained technicians specializing in marine electrical systems. Sandblasting and painting are specialties at Newpark; epoxy and inorganic coatings are routinely applied by experts. The yard's coatings work has been field-tested around the world.
Newpark's gas-freeing plant is one of the most modern facilities of its kind on the Gulf Coast, specializing in rapid turnaround. It has a smokeless flare for LPG gas-freeing for hot work, and nitro purging for certain types of external hot work repairs to vessels.
To insure timely performance, the shipyard works two shifts per day; services are available upon request 24 hours a day, seven days a week.
Circle 74 on Reader Service Card ORANGE SHIPBUILDING In the past few years, Orange Shipbuilding Company, Inc. (OSC) in Orange, Texas, has added a 36,000-square-foot construction building having two bays each 300 feet long and 60 feet wide. Each bay is served by one 10-ton overhead bridge crane and one 30-ton crane.
Productivity, efficiency, and quality control have increased substantially since the shop expansion.
In addition to the shop, OSC has added 10 marine transporters, each with a capacity of 400 tons, that are used to move completed vessels from the construction building to the water via the yard's marine transport system. This same system is used for drydocking vessels in need of repairs. As many as five vessels at a time can be docked using five side tracks. A vessel in need of major repairs can be moved inside the building, where work can proceed uninterrupted by weather.
OSC's marine railway is sized for 1,600 tons, and has a depth over the blocks of 16 feet. Future additions include a 7,500-ton-capacity drydock that is scheduled for installation in July this year, providing increased repair capacity.
Among recent deliveries was a 52 '/2-foot pushboat for the Tennessee Valley Authority. This vessel, powered by twin Cummins diesels with a total output of 940 bhp, will be used to transport coal barges on the Green River in Kentucky.
OSC is currently completely renovating the 70-foot pushboat Habibi for Harless Towing Company of Lake Charles, La.; the vessel sank in the Lake Charles ship channel in January this year. Work includes installation of rebuilt diesel engines and generators, replacing electric pump motors, stripping and replacing all interior woodwork, installing new electronics and appliances, and repairing damaged steel. This vessel was moved into the construction building so that work could be performed quickly and efficiently.
Most other work at the Orange yard involves drydocking of boats and barges. Repairs have mostly involved sandblasting and painting, renewing bent propellers, propeller shafts, rudders, welding, and replacing damaged steel.
Circle 84 on Reader Service Card PLATZER Platzer Shipyard, Inc. in Houston has built and repaired marine equipment for more than 35 years.
Located on Greens Bayou, its 20- acre yard offers marine repair, multiple- barge haulouts, boat drydocking, machining, gas-freeing, new construction, blasting and coating, and fleeting. In addition, a flare is being installed for flaring LPG pressure barges.
The yard's 130 employees have been kept busy recently on a variety of projects. The marine railway, with a 900-ton capacity, was rebuilt several years ago to allow for simultaneous docking of up to three barges through its transfer system.
This permits working on large projects such as the recent replating of two 265-foot barges concurrently, while still being able to provide quick repair drydockings to other barges. With its 150-ton crane service, large sections can be prefabricated indoors, and fewer days are required on dock, as was the case in the recent replacement of the midsection of a hopper barge.
Platzer recently resumed drydocking and repairs to towboats.
The yard has in-house capabilities for everything except propeller repairs.
These capabilities include crane service, electrical repairs, carpentry work, machining, steel repairs, piping, and coatings. All service can be performed on an aroundthe- clock basis to minimize time out of service.
The machine shop was moved recently into a new 7,200-square-foot facility, with 10-ton crane service.
Equipment is installed for any marine machining, including rebuilding of shafts to American Bureau of Shipping standards, up to 40 feet in length. Customers' shafts and rudders are stored under a bridge crane for ready access.
Platzer has long been active in the construction of tank barges and deck barges. Recently, the yard was awarded a contract for the construction of two specialized chemical barges. At this time, these may be the only tank barges under construction in the U.S. The facility is well-suited for construction of specialty vessels of any type. The shops are set up for modular construction in 35-ton units, with erection work kept to a minimum.
Efforts are being undertaken to make the yard ever more cost-effective through flexible manufacturing techniques aimed at the small quantities of varying types of vessels to be built over the coming years. With the yard's modern shops, machining capabilities, and in-house design expertise, any type of craft up to 900 displacement tons can be built.
Platzer's barge cleaning plant has capabilities for cleaning up to four barges at a time. The plant uses water, hot water, chemicals, and steam to perform cleaning operations at its two docks. Recently, back-up pump and vacuum equipment were added to provide better reliability.
Circle 75 on Reader Service Card PORT ALLEN MARINE The Midland/Port Allen Marine Service, Inc. (PAMS) main plant located on 750 acres with 7,500-foot frontage on the Gulf Intracoastal Waterway Canal, houses the main administration and engineering offices.
Also at this site is the new construction facility with the capability of producing more than 200 barges per year utilizing the most modern numerically controlled cutting and welding equipment.
At this Louisiana location also is the Main Yard Repair Department featuring four drydocks ranging in size from 500 to 2,500 tons lifting capacity. Over the past five years, the Repair Department has drydocked and repaired an average of 765 vessels (boats and barges) per year, replacing some 320,500 pounds of steel annually. Supported by a fully equipped machine shop, electrical shop, and sandblast/paint facility, the Repair Department is able to have many projects under way at the same time.
PAMS' River Plant, located on the Mississippi River three miles south of Baton Rouge, houses a topside repair facility with more than 600 feet of repair dock space, as well as capability to perform mid-stream repairs to deep-draft oceangoing vessels, and a drydock for quickturnaround bottom and side repairs.
At this location is PAMS' gasfreeing and cleaning facility, which is equipped to handle 100 barges per month, treating and disposing of all wastes, including halogenated organics and oil sludge, with strict adherence to all regulations established by the Louisiana Department of Natural Resources and the EPA.
PAMS recently completed the conversion of 80 open hopper barges to covered grain barges for The Ohio River Company, also a Midland Enterprises affiliate. This project involved the alteration of the coamings to receive covers and the building of 80 sets, or 880 corrugated metal lift-off covers with hinged loading doors in each cover. All covers were blasted and painted. The entire project was completed in about five months.
PAMS is currently converting a 160- by 38- by 10-foot deck barge into passenger dinner/cruise barge for Gateway Clipper Fleet Inc. of Pittsburgh. The finished vessel, which will be 166 feet 8 inches long, with a beam of 48 feet and depth to main deck of 10 feet, will feature three covered decks for the seating of up to 1,000 dining passengers in air conditioned comfort. The dining barge will be propelled by a dedicated pushboat that will also contain the gallery and mechanical equipment required to service the passenger areas.
Included in PAMS' future work is a major renovation of the 290-foot passenger riverboat President. The upgrading will include extensive replacement of interior and exterior decks and bulkheads, as well as a complete blast and paint job.
PAMS is presently negotiating with Shell Oil of Houston for the construction of two LPG barges.
Each will contain three tanks 172 feet 9 inches long with diameter of 14 feet 8 inches and a design pressure of 100 psig. Tentative construction schedule for this project is to start fabrication in mid-April, with delivery of the second barge by the end of October this year.
Circle 76 on Reader Service Card SERVICE MACHINE Service Machine and Shipbuilding Corporation was founded in 1956 when the offshore industry in the Gulf of Mexico was in its infancy.
Over the years, the Service Machine Group (SMG), as the company is known today, grew in a progressive and well-timed manner, paralleling the offshore industry itself.
SMG today is a multi-faceted organization providing services in shipbuilding, barge building, drilling rig construction, drydocking, topside repair and renovation, complete electrical services, tubular manufacturing, and fabrication of major offshore facilities.
Strategically located near Morgan City, La., at Amelia, the Marine Service Division of SMG has facilities and equipment that include an area of 30 acres, 3,000 feet of water frontage, 25,000 square feet of covered work area, crawler cranes of up to 150-ton capacity, 10,000 square feet of warehousing, floating drydocks with up to 2,500-ton capacity, and steel bulkhead for efficient topside work.
The Marine Services Division is fully equipped, staffed, and experienced to build vessels such as inland and offshore tugs, towboats, utility boats, ferries, supply boats, tug/supply vessels, deck cargo barges, jackup drilling rigs, and drilling/workover barges.
This Bayou Boeuf facility is linked directly to the Gulf of Mexico without restriction via the Gulf Intracoastal Waterway, the Atchafalaya River, Bayous Boeuf and Black, and the Chene Navigational Channel that is 400 feet wide and 25 feet deep.
Electrical service is provided by Sermac Electrical Systems, an affiliated company with offices in Morgan City. Sermac provides design and installation of total electrical systems, generator control panels, castle boat and two 58-foot aluminum oyster boats.
The 75-foot steel shrimp trawler continues to be the boat most in demand at the Steiner yard. This boat has proved to be very versatile, and so much in demand that there have been no significant changes in its hull design since 1980. The 75- footer was designed especially for fleet operations, with complete interchangeability of parts, simplicity, durability, and low maintenance being among its features. These features, so vital to fleet owners, has also made this design very desirable for the single-boat owner.
The two aluminum oyster boats are being built for the Louisiana oyster industry. These are constructed in a more or less separate production line.
As for steel hulls, the Steiner yard makes effective use of its two ESAB Heath shape-cutting machines.
Speed and uniformity of cut-out are afforded by this process, and there is much less chance of error. Not only has Steiner been able to supply its assembly lines with parts through the use of the Heath machines, but it is planned that the use of these machines will eventually be sold to other shipyards for the cutout of their vessels.
At the beginning of 1985, Steiner converted its inventory, cost control, and other bookkeeping process to an all-new computer system.
This IBM System 36 has the capacity for handling all the present demands of Steiner Shipyard as well as its inventory system. Additionally, the computer has capacity for anticipated growth for many years to come.
Circle 78 on Reader Service Card SWIFTSHIPS Swiftships, Inc. is a division of United Nuclear Corporation of Falls Church, Va. Swiftships, Inc. of Morgan City, La., was established in 1969; the current president, Jerry Hoffpauir, was one of the founders.
Swiftships is comprised of five divisions: the Morgan City yard specializes in aluminum construction of oilfield vessels, ferryboats, military craft, specialty vessels, and pleasure boats; Swiftships/Champion of Pass Christian, Miss., specializes in construction of larger steel vessels; Swiftships/Lafitte in Marrero, La., is a 24-hour repair facility and can accommodate vessels up to 125 feet; Swiftships/Freeport in Freeport, Texas, is a full-service repair yard specializing in supply vessels, large ocean-going barges, utility boats, tugs, and crewboats, and has two dry-docks of 2,500 tons and 3,500 tons; and Swiftships/Maroil in Singapore, which specializes in construction of military and oilfield support type vessels of steel and aluminum.
Circle 79 on Reader Service Card TAMPA SHIPYARDS A subsidiary of The American Ship Building Company, Tampa Shipyards Inc. is a full-service shipbuilding and repair facility. Located on the newly deepened, 43-foot Sparkman Channel, the Tampa yard has recently become the largest shipyard in the State of Florida.
With a production force of 1,500 employees, the yard is presently engaged in new construction as well as ship repair and conversion projects.
The newbuilding work is centered around the current $300-million, T-5 tanker program. Five 30,000- dwt product tankers are being constructed for Ocean Product Tankers, Inc. of Houston, for ultimate charter to the Military Sealift Command.
These tankers, 615 feet long with a beam of 90 feet and 34-foot draft, are designed to meet special requirements of the U.S. Navy.
In order to compete in today's highly technical shipbuilding industry, Tampa Shipyards embarked on an innovative and aggresive expansion program. During 1984, major new facility installations were completed and integrated into the current ship construction program.
Recent additions include two graving docks 750 feet long, 125 feet wide, and 28 feet deep, and a new 90,000-square-foot erection facility.
This assembly building is 600 feet long, 145 feet wide, and 115 feet high, and is serviced by two 250-ton overhead bridge cranes. Some 350 feet of this building straddles the new-construction drydock, allowing pre-assembled units weighing up to 500 tons to be erected in a totally enclosed environment.
In addition to these significant new erection facilities, Tampa Shipyards has acquired a long-term lease on the totally enclosed 430,000- square-foot Westinghouse heavy fabricating facility located near the main yard. In this facility, steel modules weighing between 200 and 500 tons are fabricated, prematched, completely pre-outfitted, and loaded on barges using the 700- ton overhead bridge crane that extends over the water for that purpose.
The large units are then transported to the main yard where they are assembled into the massive stern structure located inside the erection/assembly building.
New full-service outfitting berths adjacent to the assembly building are equipped with gantry and tower cranes to facilitate outfitting and testing. Tampa Shipyards is also making substantial investments in other related areas, including upgrading and modernization of the steel fabricating, sheet metal, carpentry, machining, electrical, and pipe departments, as well as blasting and painting facilities.
With its convenient location and year-round favorable working conditions, Tampa Shipyards provides one of the most unique and modern shipbuilding and repair facilities in the U.S.
Circle 80 on Reader Service Card TODD SHIPYARDS Todd Shipyards Corporation's presence has been positively felt in the U.S. Gulf of Mexico region since 1922, when operations were commenced in Mobile, Ala., with a subsidiary company, Todd Shipbuilding & Dry Dock Company. In 1923 Todd purchased land in Algiers, La., across the Mississippi from New Orleans, and Todd Engineering, Dry Dock & Repair Company was formed in 1925. This facility ultimately became the New Orleans Division.
Establishment of Todd Gal- veston Dry Dock Inc. in 1934 and the Houston Shipbuilding Company in 1941 added to Todd's prominence in the Gulf area.
The Mobile yard was leased and later sold, leaving Todd with four locations in the Gulf area, although the Houston Division has been idle since 1983.
Located on Pelican Island, the Galveston Division is a fully integrated repair/conversion complex.
The yard boasts two new steel floating drydocks. One is 853 feet long and 164 feet wide, with a lifting capacity of 40,000 long tons; the other measures 550 by 118 feet and can lift up to 18,000 long tons.
In December 1984, Todd Galveston was awarded a $30-million U.S.
Navy contract for the modification of the first of two C5-S-78A Seabridge Class RO/RO-containerships into Aviation Logistic Support Ships (T-AVB). These ships have an overall length of 602 feet and beam of 90 feet.
A quarter-mile away the Galveston Division operates the Southwest Plant, occupying 22.4 acres and featuring a 250-foot slip with a 200-foot covered marine bay with a width of 85 feet and depth of 15 feet. This facility is ideal for launching and final assembly of vessel midbodies, barges, and offshore structure components.
Two 200-ton-capacity bridge cranes and 118,855 square feet of covered manufacturing space within a 685-foot steel building make the Southwest Plant exceptionally suited for heavy structural steel fabrication.
Todd's New Orleans Division is capable of repairing a wide variety of ships, including tankers, ferries, cargo vessels, and barges of every size. The yard has three floating drydocks. Two of these each have a lifting capacity of 15,000 long tons, measuring 579 by 84 feet and 614 by 86 feet. The smallest drydock, measuring 306 by 63 feet with a lifting capacity of 3,500 long tons, was built recently to service inland waterway vessels. A large new crane, reconstruction of a 525-foot wharf section, and construction of a new 440- foot wharf extension were also part of a recent improvement program at the New Orleans facility.
In addition to its Gulf operations, Todd Shipyards Corporation, headquartered in New York City, also has shipyard facilities on the West Coast in Seattle, San Pedro, and San Francisco.
C i r c l e 8 1 o n R e a d e r S e r v i c e C a rd
Other stories from April 1985 issue
Content
- M A R I T I M E R E P O R T E R P u r c h a s es N e w a n d L a r g e r W o r ld H e a d q u a r t e r s O f f i c es page: 4
- Signet Awards Wartsila Design Contract For Two Cruise Vessels page: 5
- Propeller Polishing Guide Offered By Lips Propellers page: 6
- Kockums Delivers Big Vehicle Carrier To Wallenius Lines page: 7
- Red Fox Negotiating Licensing Agreement With John G. Kincaid page: 7
- Ocean Studies Conference Slated For June 16-19 At University Of Rhode Island page: 8
- Nor-Shipping '85 page: 10
- Pyramid Pump Division Offers N e w Catalog On Rotary Pump Lines page: 13
- Haggett Named Board Chairman For Shipbuilders Council Of America page: 13
- Valmet Specializing In Meeting Requirements Of The Offshore Industry page: 14
- New Diagnostic Kit From Aeroquip Corp. page: 14
- Marine Machinery Association Issues Invitation To Attend May 1, Meeting In D.C. page: 15
- Fincantieri To Build Huge Offshore Workship For Micoperi page: 18
- Stork-Powered Tug/Supply Vessel Launched By Quality Shipyards page: 20
- Robertson Introduces New Small Commercial Autopilot page: 20
- Halter Launches Rocket Booster Recovery Vessel 'Independence7 page: 22
- Radio Technical Commission For Maritime Services Annual Meeting page: 24
- Tug Fleet Owner And Operator Bart Turecamo Dies At Age Of 64 page: 25
- New Product Brochures Offered By Armco page: 25
- Fibergrate Introduces New Fibertred FRP Stair Tread Panels page: 26
- Promotions Announced By Woodward-Clyde page: 27
- Allied Introduces New Super-Strength Fiber page: 28
- ASNE DAY '85 page: 30
- Marinette Marine Offers Brochure On Shipbuilding Facilities And Capabilities page: 40
- MarAd Awards Contracts Totaling $2.7 Million For Repairs To RRF Ships page: 41
- Stanford Study Shows That Oceanrouting Reduces Casualties page: 42
- Marathon Introduces Semisubmersible For Gulf Of Mexico Environment page: 43
- T-AKX Prepositioning Ship Delivered By Bethlehem's Sparrows Point Yard page: 44
- "No-Leak" Seal From Falk Keeps Oil In And Dirt Out page: 45
- National Marine Study On PowerLube 750® Now Available page: 45
- Constant-Tension Winch Now Available From W.W. Patterson Company page: 46
- Capacity of Cockatoo Dockyard's Vickdock® Expanded To 1,000 Tons page: 46
- OTC-'85 SPECIAL PREVIEW page: 49
- Ship Financing Reforms Announced By Secretary Of Transportation Dole page: 76
- 'Silver Anniversary' For Atlas Freshwater Generator And Knutsen Vessel page: 76
- Gulf Coast Shipyards page: 78
- DAMPA Continuous Ceiling Approved By U.S. N a v y page: 97
- Norcontrol Revamps Its U.S. Operations — H o g a n Named President Of Authorized Agent page: 97
- Scanner Gives Peterson Builders Edge In Navy Shipbuilding Project page: 98
- Saab Introduces New Level-Gauging System page: 99
- Daewoo Names New Shipbuilding President page: 101
- Saab Purchases Salwico page: 101
- Perry Offshore Announces Expansion Through Tritech International Network page: 101
- Sonatech Announces New Expendable Doppler Soil Penetrometer page: 102
- TeleSystems Introduces Advanced Transportable Satellite Earth Station page: 102
- Membrane Air Separation System From Dow Produces Gaseous Nitrogen On-Site, Economically page: 103
- Work On Hopper Dredge 'Ouachita' For Gulf Coast Trailing Co. Is On Schedule At Twin City —Launching Set For End Of May page: 104
- New Worldwide Directory Available From Manville page: 104
- Larsson Appointed N e w Chief Executive of MacGregor-Navire page: 105
- BMV Maskin A.S. Introduces New Engine page: 106
- New Waterways Rope By Columbian Rope page: 109
- New Monitoring/Alarm System By Siemens AG page: 110
- Allison Gas Turbines Will Power World's Fastest Patrol Boat page: 111
- Contecco Appointed Exclusive Sales Agent For Swedish Firm page: 111
- Moss Point Marine Delivers Giant Freezer/Stern Trawler page: 112
- London Is Site For First International Cruise Shipping Conference June 19-20 page: 112
- McDermott Upgrades M / V Enterprise For Offshore Logistics page: 116
- New Marine Overcoat Sea-Slide™ Increases Speed, Saves Fuel page: 116
- Emulsion Fuels International Announces Supply Agreement With Exxon Chemical page: 118
- Cummins Announces New Increased Power Ratings For Their NT(A)855-M And KT(A)19-M Marine Engines page: 118
- Matson Will Convert Trailership To Combination Containership-RO/RO page: 119
- NcNab Now American Supplier Of Aquacatch® Speed Through Water Log page: 119
- ASCARGO Offers Free Brochure On Cargo Access Equipment page: 124
- Baldt 'Engineering Innovations Bulletin Highlights Moor-Free"" Rapid Release System page: 124
- Clemco Pipe Cleaning Tools Blast-Clean Pipe Interior Without Rotating The Pipe page: 125
- Shipboard Computer Distributed By Magnavox Displays Detailed Charts, Automates Navigation page: 125