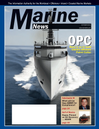
Page 32: of Marine News Magazine (October 2012)
Year in Review & Leadership
Read this page in Pdf, Flash or Html5 edition of October 2012 Marine News Magazine
BOATBUILDING Let?s talk about weight loss. No, not the kind that involves hours on a treadmill. Weight reduction in berglass workboats has a multitude of advantages: better performance on lower horsepower, the ability to carry heavier loads, and improved fuel economy. Brunswick Commercial and Government Products (BCGP), a manufacturer of berglass, RHIB, and aluminum workboats, recently incorporated resin infusion technology into their lamination process to add a ?lightweight? option to the IMPACT rigid in atable line. David Adams, a development engineer for BCGP, explained the rationale. ?Our government clients have been asking for lighter weight small patrol boats. The inherent challenge is to create lightweight parts that have structural integrity equal to or better than our normal construction,? says Adams. ?But if you give your customers what they ask for, then you better not have any issues with the end product. In our case, we had to ensure that the weight savings were signi cant enough to justify the added cost, and most importantly, the nished product had to be just as robust. Resin infusion is not a new technology. Large yacht manufacturers have used this process for years with great success, but it?s been cost-prohibitive for smaller recreational boats.? BCGP incorporates the SCRIMP (Seemann Composites Resin Infusion Molding Process) method, which was initially developed in order to reduce the emission of volatile organic compounds (VOC?s). The rst patent was awarded in 1990 to Bill Seemann, a former boat builder and founder of Seeman Composites, Inc. Purchased by Brunswick Corporation, the technology was put to use in the construction of luxury yachts. Because the method does not require the use of unique materials and fabrics, it is a viable alternative to more expensive carbon ber or Kevlar. When resin is introduced to dry glass under vacuum, the process yields a signi cantly higher glass to resin ratio over traditional open-molding techniques. Excess resin in the nal part is minimized, achieving weight savings of up to 35%. ?Traditionally, infusion technology has been used to reduce production cost, but our goals are slightly different: we were looking for signi cant weight reduction of the completed boat, and to improve consistency and laminate quality,? says Adams. Infusible stacked laminate material is selected to maximize the ow of resin through the part under vacuum, assuring that the user will saturate the part completely. The laminate and core usually consist of coarse materials that will serve as ?resin highways? to ow resin through the part when put under vacuum. This is seen rsthand with the increased demand of grooved cores and infusion- speci c berglass mats that resist full compression under vacuum, thus creating a void through which resin can travel. The rate of failure is reduced, giving boat builders the con dence to implement the resin infusion process. Knowing that the driving force for the implementation of infusion technology was customer demand for signi cant Resin Infusion in Workboats By Keith RanieriOctober 201232 MNMNOct2012 Layout 32-49.indd 32MNOct2012 Layout 32-49.indd 3210/2/2012 9:54:18 AM10/2/2012 9:54:18 AM