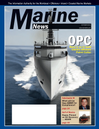
Page 33: of Marine News Magazine (October 2012)
Year in Review & Leadership
Read this page in Pdf, Flash or Html5 edition of October 2012 Marine News Magazine
weight savings, the engineers at BCGP took a slightly different approach, starting with the selection of their laminates. They abandoned the use of ?resin highways? to ow resin through a part, since they become brittle and serve a minimal structural purpose once the part has fully cured. Whereas most laminates are typically selected to easily ow resin, BCGP engineers selected laminates to be as light as possible, without sacri cing strength. After numerous test panels on both glass tables and tooling, enough data was gathered in order to move forward with full size production parts, and assemble a complete boat.An additional bene t to using resin infusion technology is consistency, which is in high demand in a production environment. By removing the variables of the ambient conditions and individual laminating styles during molding, the resin infusion process yields a repeatable and consistent part. Since the part is sealed under vacuum, the only condition variable is temperature. This can be adjusted with resin chemistry and various additives. The entire berglass part is laid up in dry form and essentially gives the user the freedom to determine when the part is actually infused, which takes less than an hour. Since there is no ?clock? running while the dry glass is being laid in the mold, it gives the laminator the ability to have an even higher level of quality control before resin is introduced into the part. This gives the builder the ability to work at a slower, more controlled pace. The cost trade-offs associated with resin infusion technology vary. In large boats, resin savings alone can be enough to justify the additional time and labor. This can be seen with the increasing popularity of infused hulls that are over 45 feet in length. For BCGP, it is all about weight. The resin savings help offset the cost, but the SCRIMP process requires additional materials to improve the quality of the part. The additional materials as well as the increased production time add cost, but the end result of weight savings and improved consistency make this option attractive for some customers. The rst infused boat from BCGP is a 27? rigid in atable boat, called an 850 IMPACT. The boat will be debuted in New Orleans in December. www.marinelink.com MN 33MNOct2012 Layout 32-49.indd 33MNOct2012 Layout 32-49.indd 3310/2/2012 9:54:49 AM10/2/2012 9:54:49 AM