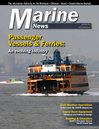
‘Securing’ the Inland Markets with Innovative Standardization
Patterson Manufacturing follows its substantial success in the barge winch markets with an equally impressive boat-to-barge coupling system.
In 2008, Pittsburgh-based Patterson Manufacturing Company developed the YoYo Barge Winch, a revolutionary design that reflected a total re-thinking of the way winches do their job. Fast forward to 2015 and the YoYo has penetrated North American inland markets in a big way, in just a few years. Even as the “YoYo” winch has arguably become the inland standard in barge winches – especially considering the 10,000th YoYo unit sale was recorded last year – Patterson has plans to engineer the same sort of revolution in the niche boat-to-barge coupling markets.
On the heels of the now ubiquitous and highly successful YoYo winch, Patterson Manufacturing has now introduced an equally innovative Self-Aligning Roller Chock (SARC) for the inland barge industry.
According to Patterson itself, their patent-pending Self-Aligning Roller Chocks (S.A.R.C.) are the next evolution in boat to barge coupling. Effectively utilized for both face wires and wing wires, the Patterson line of S.A.R.C’s include all of the features a quality inland operator expects: optimized sheave materials for both synthetic rope and steel cable, rounded edges to minimize wear points, corrosion resistant construction utilizing stainless steel and protective coatings for extended life, and extreme durability.
Addressing the never-ending need for innovation and increased safety within the inland marine industry, Patterson CEO David Grapes told MarineNews in December, “At Patterson we are constantly trying to help simplify our customers processes through increased efficiency and safety. In regards to the Self Aligning Roller Chocks, we were able to recognize, through working directly in the field with customers, that current solutions were not meeting their needs. With the transition to synthetic rope across the industry and potential issues created by this, we dove head first into the details of how the synthetic ropes are utilized on vessels, and were able to engineer innovative solutions to these issues that help solve both safety and functionality problems inherent with previous products and methods, while at the same time extend the life of the customers high cost consumables.”
Patterson’s Self Adjusting Roller Chocks & Roller Buttons
Until now, chocks could only align vertically. This helped extend the life of the rope, but allowed for dangerous side loading that could lead to permanent yielding of the product causing it to become non-functional, or worse, cause catastrophic failure. With the Patterson Horizontal Alignment Mounting System, the S.A.R.C. becomes the first truly self aligning design. The entire unit always orients itself to the center of the line pull, both vertically and horizontally, regardless of the angle. In short, these units are the ideal solution for fleeting boats that face many barges that have different heights, deck fitting configurations, and widths (one wide, two wide, four wide, etc.).
The S.A.R.C. is designed to functionally withstand the maximum strength rating of new ropes properly sized for the unit. What this means is that the rope is the weak point in the system. Its superior alignment capabilities allow for this, while minimizing the need for overdesign. This eliminates product failures common with previously available solutions. What it ensures is that you have the safest possible redirect point for your face rigging between your winches and barges, regardless of the line load, or the redirect angle.
The protection of rope is critical; not only in terms of ensuring safe operating conditions, but also to minimize the replacement cost of this expensive consumable. Addressing this reality, Patterson’s Spring Loaded Vertical Assist feature uses a high strength torsion spring mechanism, effectively eliminating the majority of the weight of the sheave housing, allowing your chock to begin aligning with little to no line tension, even when using ultra light synthetic rope. This eliminates abrasion by keeping the rope where it belongs: in the sheave, keeping your crews safer, and saving money. Best of all, perhaps, is the fact that S.A.R.C. units can be used in conjunction with other OEM buttons and/or deck fittings.
Similarly, Patterson Roller Buttons are proven to 50 tons and different from any other product on the market today. The robust base won’t yield under pressure, and the high-strength plastic construction has been extensively tested at high-cycle rates that mimic real life. Broken roller buttons lead to downtime, hotwork, decreased productivity — and lower profits.
Safety and Efficiencies: achieved through standardization
For decades, barge owners and operators had no reason to think twice about their rigging. There were only a few choices when it came to winches, and there were ratchets as well. In response, Patterson’s YoYo winch answered many if not all of those critical questions. Today, the newly designed S.A.R.C. and Patterson Roller Buttons are set to solve yet another quandary. For the inland waterways shipping industry, it means even more productivity and profitability, achieved through standardized fittings. Ultimately, efficiency increases are achieved through the need for minimal maintenance to the unit itself, eliminating cost in both parts and labor, and most importantly, through maximum protection to the synthetic face lines, which are extremely high cost consumables.
While S.A.R.C. and Patterson Roller Buttons are initially more expensive than the competitive product that they are replacing, Patterson’s David Grapes says that the return on investment will come from improved life length for the expensive synthetic face lines. Beyond this, the equipment also eliminates the labor intensive practice of positioning and moving chafing gear on the boats.
While targeted for the newbuild markets, the units are also practical for retrofit during any visit to the shipyard/repair facility as long as the shipyard is already planning to gas-free the vessel. According to Patterson, the removal of the old unit and subsequent welding of the Patterson pin into place should be a relatively short process. And, that’s the last time the customer will ever have the need for hotwork when it comes to Patterson’s S.A.R.C.
Today, Patterson reports that it is already in full production with its S.A.R.C. and Roller Button equipment and that units are in use by at least two major inland operators, on the Mississippi/Ohio river corridor and in the Pacific Northwest, in and around the Seattle area. Clearly, Patterson hopes that S.A.R.C. will fast become the new standard for vessel facing deck fittings, in the same manner that the YoYo gained widespread industry acceptance. The newest tool for all pushboat applications, including line-haul, short-haul, and fleeting vessels is now here.
David Grapes summed up the situation for MarineNews readers nicely, saying, “We are optimistic that this product will see wide scale adoption in the industry. Once a customer has had a chance to experience the benefits of this new design, we think it will be the obvious choice for all of their future new build and retrofit applications.” Given his success with the now universally accepted YoYo winch, there’s little reason to doubt him and every reason to hope he’s right.
(As published in the January 2015 edition of Marine News - http://magazines.marinelink.com/Magazines/MaritimeNews)
Read ‘Securing’ the Inland Markets with Innovative Standardization in Pdf, Flash or Html5 edition of January 2015 Marine News
Other stories from January 2015 issue
Content
- Marine News January 2015 - Editor's Note page: 6
- Insights: Johan Roos, Interferry's Executive Director of EU and IMO Affairs page: 12
- A Commercial Marine Lender and Lessor’s Lexicon page: 18
- OP/ED: Knowing the Rules of the Road page: 21
- Canada’s Ferry Industry Sets Course for Success page: 22
- Ferry Fixation: The Good, the Bad and the Ugly page: 24
- Ferry Safety in the Developing World page: 28
- US Ferries Are Safer, but Regulatory Burdens Grow page: 32
- Taming the Arctic, One Ferry at a Time page: 36
- Cold and Calculating: Dealing with Ice in Domestic Waterways page: 41
- SUNY Maritime: Bridging the Competency Gap page: 44
- ‘Securing’ the Inland Markets with Innovative Standardization page: 48
- Braemar’s FSP-LNG Containment System page: 57
- Ice-strengthened Ship Gets Ecospeed Protection page: 57
- YANMAR America’s EPA Compliant Engine page: 57