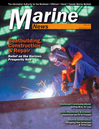
Pontoon Deck Preservation for Floating Dry Docks
By Bill Kraus
Always important, anything but simple, but often overlooked
Dry dock pontoon deck preservation is often taken for granted. In the flow of ever changing priorities for dry docks, it often gets pushed aside and/or delayed. If neglected long enough and often enough between preservation cycles, the thickness of the pontoon deck steel plates can be compromised. Salt water with chloride contamination causes accelerated corrosion while impact and abrasion damage from heavy equipment also take their toll.
For shipyards, the overall objective should be to provide a protective surface that will hold up over time, and that is easy to clean. Ease of cleaning can save a lot of cost each time after repeated dockings. All of that said; surface preparation is the key.
Coatings: Preparation is Everything
A clean sweep down of the intended surface areas should be done before the subcontractor arrives on site. Pressure washing at 3500 psi is the best way to remove chloride contamination, loose rust scale, and/or delaminated coatings. Weather can be an annoying problem, but if it interferes, it is better to call off work for the day than to have flash rust appear, or worse, coating delamination due to excess moisture.
Shot blasting is one of the most cost effective methods of removing the old surface down to a near white metal condition. A 3-4 mil anchor profile is preferred. Sand blasting is another method of surface preparation, but the containment required for sand blasting the entire pontoon deck in most locales makes this approach too expensive. Nevertheless, sand blasting is ideal for reaching areas – wing walls, and raised steel strips along the pontoon deck – that can be difficult to otherwise reach. In each case, a temporary shed can be constructed using PVC pipes and plastic sheeting which moves along with the sand blaster inside. Hand tooling should be kept to a minimum – it is labor intensive and expensive.
If an anchor profile already exists on the steel from past surface preparation efforts, then UHP (ultra-high pressure) water blasting at 35,000-40,000 psi is a modern alternative. Designed to suck up debris and water from blasting, it also leaves the surface clean and dry.
Chloride contamination needs to be removed to the level of 70 microsiemens of conductivity, even if it means more than one pressure washing. Otherwise, once the coating has been applied, galvanic corrosion cells will develop, causing delamination of the coating. Flash rust can be a problem for coating longevity, although a slight ‘bloom’ can be tolerated by some coatings. Before the work day ends and moisture appears, a primer coat should be applied to seal the freshly blasted steel.
Five Year Life Service
A high build coating system is best for longevity, and the proper equipment will involve the use of a plural component, heated airless spray machine capable of handling Part A/Part B ratios as high as 10:1. The coating system to be employed should include a primer coat in addition to the top coat. That’s because the typical 10-15 mil coating system employed in the past is simply not sufficient. A 40 mil system is optimal, and extra millage may be required if pitting is severe.
At least two days should be allowed for the coating system to cure; at least 24 hours for foot traffic, 48 hours for vehicle traffic and submergence, a five day cure. An anti-skid treatment on top of the final coat – a 16-20 grit aluminum oxide or equivalent – finishes the job.
Calculating Costs: apples to apples
The coating system itself is always the least expensive part of the pontoon deck preservation process. In fact, the coating applied will typically amount to only 20 percent of the overall job, with labor and equipment to prepare the surface and labor and equipment to apply the coating making up the rest.
Full containment of the dry dock, if required in a given region for sand blasting, is very expensive and thus sand blasting should be avoided.
Surface preparation is the most expensive part of the entire process due to the labor and equipment involved. However, if the shipyard can clear the pontoon deck completely before surface prep commencing, and avoid unscheduled dockings from interfering, costs can be kept to a minimum. The performance of the surface prep subcontractor is typically enhanced if he is also responsible for applying the coating system. That’s because, blame cannot be shifted to another party should something go wrong. The actual coating application, with proper equipment and coordination with the surface prep effort, can be the second lowest cost factor in the overall preservation process. Overcoat times between coats as specified by the manufacturer are critical for proper adhesion and curing.
The fewer the number of coats required to meet the specified mil thickness, the less the labor costs that will be accumulated. For example, if it takes five coats to achieve 40 mils in one coating system, but only 2 coats to achieve 40 mils in another, labor will be much higher in the former. Ceramic epoxy coatings can be more expensive per gallon, but if they can be applied in two versus five coats, the total material and labor costs will likely come out lower.
While dry dock availability is paramount, unscheduled dockings create a nightmare for cost effective accomplishment of the overall job. The goal should be 100 percent availability of the dry dock from start to finish of the job to experience maximum efficiencies in all areas of endeavor. Hence, coating should not be scheduled for this work unless there is a clear ‘open window’ to get the job done. This is the absolute key to minimizing costs. And, as a general rule of thumb, pontoon deck preservation represents less than 10 percent of the cost of steel replacement.
Finally, it is worth investing in a QC technician who can continuously monitor chloride contamination and anchor profile mil depth during surface prep, as well as monitor coating mil thickness during the application process. This technician can either be supplied by the shipyard or the subcontractor.
Examining Coating Systems
The typical two part epoxy system has been used for many years to preserve pontoon decks, and it is still in use today. However, the addition of ceramic particles, or ceramic particle loading, serves to enhance the mechanical properties of the coating far beyond a normal epoxy system.
Mechanical properties of the coating system are extremely important. CeRam-Kote 54 SST Primer with CeRam-Kote SPG (Sprayable Grout) Top Coat, for example, is one coating system recommended for pontoon deck preservation. John Vitzthum, Dockmaster for BAE Ship Repair-San Diego, has been instrumental in its development. When compared to a typical epoxy coating, this system features ceramic particle loading, which provides 5 times the adhesion, 4 times the impact resistance, 10 times the abrasion resistance, flexibility and dialectric strength sufficient to virtually eliminate galvanic corrosion. It also has excellent chemical resistance, and low permeability due to the 60 percent ceramic particle content. Finally, it is ceramics that provide the lubricity of Teflon, thus making the deck easy to clean, once coated. CeRam-Kote SPG is a 100 percent solids, high build coating which can be applied up to ¾” thick. In fact, it has been used to build up the thickness of steel plates to meet minimum thickness requirements. Bob Heger, President of Heger Dry Dock Engineering, referring to the CeRam-Kote product, said in January, “We recommend it to all of our customers.” Recently, the CeRam Kote system was applied on a Vigor-Alaska floating dry dock. Dockmaster Greg Howe told Marine News, “This coating system is holding up amazingly well.”
Warranty: as important as the coating itself
The typical one year warranty offered for many coating jobs is insufficient. Insist on a multi-year warranty. Mil thickness is again very important as it has an impact on the warranty. Obviously, a 10-15 mil coating thickness is not going to hold up as well as a 40 mil thickness, which can yield a five year warranty, excluding extraordinary impact damage from heavy and/or sharp objects. The shipyard should therefore make arrangements at the outset for “field repair” of this kind of damage during the course of pontoon deck usage. All parties – the shipyard dockmaster, coating manufacturer and surface preparation and coating contractor – should a part of and signatory to the agreed to warranty.
Whichever coating manufacturer is selected, their factory technical representative should be on site throughout the project to supervise as necessary to ensure surface prep and coating applications are done correctly. If any other subcontractors are involved, such as for deck blasting, debris removal, wash down, etc., they should be under the control and responsibility of the prep/coating subcontractor to ensure performance. Once again, a single subcontractor to do the entire job will ensure better results.
The Authour
Bill Kraus is a CeRam-Kote Tech Rep for Shipyards. Kraus holds degrees in both Electrical Engineering and Mechanical Engineering from the U.S. Naval Academy Contact him at [email protected]
(As published in the April 2016 edition of Marine News)
Read Pontoon Deck Preservation for Floating Dry Docks in Pdf, Flash or Html5 edition of April 2016 Marine News
Other stories from April 2016 issue
Content
- Interview: Frank Foti - President & CEO, Vigor Industrial page: 12
- The Master’s Authority: a Vital SMS Caveat page: 18
- How Politics Impacts OPA 90 Responder Immunity page: 20
- Support for Uniform National Discharge Legislation Builds page: 22
- Manage and Mitigate Risk on the Water page: 26
- North River Boats Thrives in a Challenging Build Market page: 28
- AIS Regulations: New Responsibilities and Opportunities page: 40
- Workboat Comms: Controlling Connectivity Costs page: 44
- Pontoon Deck Preservation for Floating Dry Docks page: 48