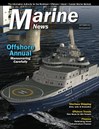
Shipyard Productivity Reaches New Heights
By Jamie Goddard
Lightweight Synthetic Lifting Slings Take Shipyard Productivity to New Heights; Material Handlers provide critical link in Hudson River PCB Remediation
A job completed on time or ahead of schedule is a display of the proficiency, productivity, and innovative thinking that can give you a competitive edge. And with the current oil market and the upcoming elections fogging the forecast for future orders (and indicating a likely dip), shipyards are vying to become better and faster, and capture every edge they can. To seize these opportunities as they arise, many are leveraging innovative systems, materials and tools that allow them to be agile, efficient, and nimble.
As a manufacturer of one such tool — the synthetic heavy lifting sling Fortis² — Yale Cordage has seen this movement through a unique vantage point – one where seemingly small details and tools are optimized for big results. Back in May, we shared how Fortis² transformed the safety and efficiency of heavy lifts at one large American shipyard. More recently, another shipyard followed suit – not only creating safer, more efficient lifting conditions, but, in coordination with other process improvements, performing a 700-ton lift and its corresponding construction phase a full three weeks ahead of time. And while we can’t speak to the other factors that contributed to the ahead-of-schedule delivery, we can speak to how lightweight cordage played a role – and how it can do so for your yard, too.
All the Properties of Steel Wire Slings at 1/8th the Weight
Fortis² is a multi-part sling made of Unitrex XS Maxwear synthetic cable that has a core of Honeywell Spectra HMPE fiber, is encased with a neoprene coating, and is overbraided with a tough high-tenacity polyester jacket – a construction just as abrasion-resistant as its wire counterparts. For routine heavy lifts, a 15-foot, 44-lb. synthetic multipart Fortis² sling exhibits the same stretch characteristics and stiffness of its 250-lb. wire equivalent, with an even better lifting capacity at 50 tons.
For massive lifts, yards can employ multiple 160-lb, 55-foot Fortis² slings, which are rated for 100 tons and can still be lifted and moved around without a crane or forklift – a protocol that contrasts sharply with that of its 1,000-lb. steel wire counterpart. Together, these strength, stiffness, and lightweight characteristics make it possible to use synthetics in ways you never have before – saving minutes and hours that add up to weeks over the course of a project or job.
Time Savers:
Until recently, the efficiencies of synthetics were limited to lifts that didn’t require the sling to be pushed underneath the load. Because of its stiffness, wire was the only option for those lifts – which also tend to be the heaviest. But today, even the heaviest of them all – like the 700-ton shipyard lift, which required three cranes – can be rigged in record time with lightweight lifting slings. Because the core fiber in Fortis² is parallel-braided to minimize twist and then sealed in place with the neoprene layer, the fiber retains its optimal strength and exhibits stiffness comparable to wire – a win-win all around, and a big time saver when it comes to rigging up a lift.
An elite modern shipyard workforce should not be defined by the brute strength of its workers. But without an equivalent or superior synthetic alternative, it’s hard to avoid either hauling enormous, heavy steel wire and chain slings around the assembly area manually, or waiting on the slow strength of cranes to do the job for you. One is a tax on your body; the other is a tax on your time. Fortis² slings can be moved around by hand without wasting time or risking injury. For routine lifts, instead of involving multiple workers and possibly multiple machines, most Fortis² sling sizes can be picked up by one person who can carry it over, slide it under the hook, and complete the job without ever needing help from a coworker or machine.
Several yards have adopted 55-foot Fortis² slings, which are rated for 100 tons and can be lifted and moved around without a crane or forklift. Compared with their 1,000-lb. wire counterparts, these slings weigh just 160 pounds. And because even the heaviest-lifting sling is still such a manageable weight, yards can use a set of 100-ton rated slings in various lengths to lift loads of all weights. It’s still necessary to have multiple lengths available to keep angles correct based on the width of the load, but there’s no need to have multiple load ratings for each length – the higher (100-ton) may always work. Not only does this save time, space and money, it also eliminates the risk of ever overloading by grabbing the wrong sling for the job. And in stark contrast with steel, the synthetic Fortis² slings don’t rust, freeze or corrode — eliminating a major maintenance concern and a lot of headaches.
While steel chain and wire slings are vulnerable to salty ocean air, rain, sleet, snow and other common shipyard weather conditions, Synthetic Fortis² slings are not. So while the effects of rust, ice and corrosion on steel wire and chain slings require extra-frequent inspections and precautions to be taken to prevent accidents or failure, rust-free, non-freezing, non-corrosive Fortis² can save a lot of time. It needs only to be inspected on its regular schedule and before every lift, and the easy to handle material allows inspections to be both thorough and fast.
Looking Ahead
Shipyards can see valuable gains from the implementation of lightweight slings – gains that put them in solid profit positions. Both outcomes amplify the importance given the uncertain economic and political environment, in which decreased future demand is still top of mind. But winning in tomorrow’s marketplace isn’t just about dominating a shrinking pond; it’s also about exploring new markets and seizing opportunities. Depending on largely unpredictable market conditions, shipbuilding demand could quickly shift from a primary need for Navy ships, to deep water exploration vessels, to the tugs, barges, and workboats expected to leverage the expanded Panama Canal.
In the construction of all of these vessels, plus buildings, bridges and more, Fortis² slings can maximize efficiency, safety, and a company’s competitive edge. And as conditions change, new easier-to-use, more flexible equipment will be at the heart of yards’ ability to turn their own large ships around (so to speak) on a dime.
The Author
Jamie Goddard, vice president of sales at Yale Cordage, leads sale strategy for the company and manages Yale’s industrial and electrical utility accounts throughout the United States. His responsibilities include building and maintaining client relationships while understanding and supporting the needs of more than 75 national and international accounts.
(As published in the September 2016 edition of Marine News)
Read Shipyard Productivity Reaches New Heights in Pdf, Flash or Html5 edition of September 2016 Marine News
Other stories from September 2016 issue
Content
- Interview: Aaron Smith Zeroes in on the Offshore Sector page: 12
- 'A Few Good Men' Thanks for the Leadership! page: 18
- Rethinking Inland Infrastructure Finance page: 20
- US Boatbuilding: Sink or Swim page: 24
- The Advent of Subchapter M page: 26
- Subchapter M: Post Publication Highlights page: 28
- Sustainable (R)Evolution: A Multipurpose Maritime Education Fleet page: 30
- Avalon Freight Services Redefines the Shortsea Shipping Formula page: 36
- CARB Powers Clean Air in California page: 40
- Why Should I Care About Thermal Insulation? page: 44
- Shipyard Productivity Reaches New Heights page: 48