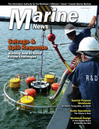
Ohmsett: Advancing Spill Response Every Day
By Jane-Ellen Delgado
The National Oil Spill Response Research and Renewable Energy Test Facility has been an integral part of the spill response community for more than three and a half decades.
Tucked away on the shores of the Sandy Hook Bay in central New Jersey resides Ohmsett – The National Oil Spill Response Research and Renewable Energy Test Facility. It has been an integral part of the spill response community for more than three and a half decades. Government agencies, private industry, and oil spill response organizations from around the world have visited the facility for testing, research and training.
From booms, skimmers and dispersants, to cold water testing and Remotely Operated Vehicle evaluations, Ohmsett has assisted researchers and manufacturers in evaluating cutting edge technologies that are helping remove spilled oil from the worlds’ oceans.
Managed by the U.S. Department of Interior’s Bureau of Safety and Environmental Enforcement (BSEE) and operated through a contract with MAR (MD) LLC, Ohmsett is part of the Bureau’s oil spill research program. Ohmsett directly supports BSEE’s mission to ensure the best and safest oil spill detection, containment and removal technologies are available to protect the U.S. coastal and ocean environments.
Realistic Testing in World Class Facilities
At the heart of the facility is one of the largest outdoor saltwater wave/tow tank facilities in North America. It is the only facility where full-scale oil spill response equipment testing, research, and training can be conducted in a marine environment with oil under controlled environmental conditions.
The tank measures 203 meters long by 20 meters wide by 2.4 meters deep and is filled with 10 million liters of crystal clear saltwater. The three movable bridges are capable of towing equipment up to six knots to simulate towing at sea. A crow’s nest mounted on the movable main bridge above the water provides a vantage point for mounting test equipment, such as sensors to remotely detect oil spills, as well as for video documentation of a test.
The facility is also equipped with a computerized wave generator capable of producing wave characteristics of 59 cm height (H1/3 at 7 meter wavelengths), 83 cm height (H1/3 irregular waves), and wavelengths up to 30 meters.
Ohmsett plays a critical role in providing full-scale evaluations of equipment and remediation techniques that enable rapid and efficient response to an actual spill. “We are the intermediate step between small-scale bench testing and open water testing,” says Paul Meyer, BSEE’s Ohmsett Manager. “With the ability to control the testing environment, we are able to provide repeatable test conditions. This way, any equipment modifications can be measured and compared with each test performed, giving our customers the opportunity to optimize equipment performance.”
With a wide range of testing and research capabilities, the oil spill response community relies on Ohmsett for independent and objective testing. “Our staff of engineers and technicians assists customers with test protocol development, product evaluations, and provides improvement recommendations,” says John Delia, MAR program manager for Ohmsett.
The Nuts & Bolts of Research & Testing
Over the years BSEE has funded multiple research projects at Ohmsett. Most recently, two highly successful projects conducted by BSEE were the Diminishing Slick Thickness test and the ICEHORSE Submersible Skimmer. Earlier this year, Ohmsett personnel conducted performance testing of two oleophilic skimming systems to better understand the relationship between Oil Recovery Rates and Recovery Efficiencies in varying oil slick thicknesses or diminishing slick thicknesses.
At Ohmsett, skimming systems are tested to the ASTM F2709, the standard for testing the performance of stationary skimmers in calm water conditions. However, the ASTM F2709 standard calls for testing in 3-2 inches of oil in order to create the ideal conditions necessary to measure a skimming system’s maximum performance. But, in an actual oil spill it is likely that a skimmer will operate in a thinner range of oil thicknesses. In this test series, a drum and disc skimmer were tested to ASTM F2709, as well as in various other oil slick thicknesses ranging from 2-inches to 1/8-inch using standard refined test oil.
“This series of experiments was the first of its kind and represents a continuation of basic research data associated with quantifying skimmer performance with varying test parameters,” stated Kristi McKinney, a BSEE project manager.
A significant oil spill response challenge is recovering oil in ice. While response equipment and techniques to contain and recover oil spills in the offshore Arctic regions already exist, there remains a testing and evaluation requirement to determine how well they perform, and to help improve them for use in cold water and ice environments. As such, BSEE has dedicated resources to advance the knowledge of oil spill response capabilities in cold water and ice-infested environments.
“During the winter months, we can replicate cold climate conditions at Ohmsett by using a chilling system to regulate the water temperature in the test basin,” stated Mr. Delia. “In addition, we place manufactured sea ice in the test tank to simulate an ice field in which response equipment will be operating.”
The sea ice is sourced from the U.S. Army’s Corps of Engineers Cold Regions Research and Engineering Laboratory (CRREL) where it is manufactured or “grown” to support multiple Army research programs for extreme climates. Recently, however, Ohmsett staff engineers designed and developed a system for producing the ice blocks on-site. Frames were constructed at the facility, and chiller boxes maintained at 0o F were used for freezing and storage.
Using this new on-site capability for testing in a simulated Arctic environment, the staff created ice for a BSEE funded project to develop a new approach to how oil skimmer technologies are deployed in ice-infested waters. It is anticipated that the technology could potentially improve the response industry’s ability to remove oil from otherwise inaccessible locations.
In 2014, Alion Science and Technologies of New London, Connecticut was tasked with developing a submersible skimming system that can be deployed from a vessel and maneuvered underwater to the location of the oil. In February 2016, the prototype system was tested in an oil and ice field at Ohmsett. The prototype, called the ICEHORSE, consists of a small smoothed drum skimmer and three ROVs mounted to an aluminum frame, with an ice cage to prevent ice from interfering with the oil recovery process.
The ICEHORSE was assessed on its ability to maneuver, travel speed, thrust, turning radius, and submerging and surfacing characteristics. After those initial tests, ice and diesel fuel oil (dyed red for visibility) were placed in a boomed test area to create a spill within broken ice. The skimmer system, initially located outside the test area, submerged, traveled underwater, and surfaced among the oil and ice to recover the oil.
“The submersible skimmer test successfully demonstrated the concept of operation. The prototype was able to successfully submerge, maneuver under the ice, surface within the field and recover diesel oil,” commented Ms. McKinney. “Next steps will be to review test results with an eye towards future development of this concept.”
BSEE Invests so that Industry can Succeed
For 35 years, Ohmsett has moved the ball forward in all aspects of spill response testing and research
With the new advances in technology for responding in ice conditions, BSEE has invested in the facility with newly developed equipment to measure oil slick thickness and ice coverage during testing. An acoustic tool adapted to operate from a ROV, detects oil in and under ice, tracks location, and measures thickness. The sensors provide real-time measurements of the slick thickness and include cameras for real-time viewing and recording.
To accurately and rapidly assess cold water and ice testing parameters such as total surface oil versus ice area coverage and oil layer thickness, a thermal imaging camera with processing software was developed specifically for use at Ohmsett. The Tactical Rapid Airborne Classification System (TRACS) creates images that separate ice, water and oil of several thicknesses based on differences in the thermal emittance.
The Author
Jane-Ellen Delgado is the Senior Marketing Communications Specialist of the Ohmsett Facility. She has been with Ohmsett since 2004 managing the branding of the facility. Ms. Delgado holds an MBA in Marketing from the City University of Seattle, WA and a B.S. in Journalism from the State University of New York at Brockport. On the WEB: www.ohmsett.com
(As published in the October 2016 edition of Marine News)
Read Ohmsett: Advancing Spill Response Every Day in Pdf, Flash or Html5 edition of October 2016 Marine News
Other stories from October 2016 issue
Content
- Towing Industry Safety: AWO & USCG Joint Analysis … By the Numbers page: 8
- Interview: Todd Schauer - President, American Salvage Association page: 12
- Op-Ed: Alaska's Golden Offshore Opportunity page: 18
- Ohmsett: Advancing Spill Response Every Day page: 20
- Fair Contracting in Casualty Response page: 24
- Sailing into the Arctic’s Future page: 26
- US Offshore Wind Comes to Life page: 28
- Foss Maritime: Hard at Work in the Arctic page: 32
- Incentivizing Spill Response Innovation page: 38
- Changing Spill Risk in a Changing Arctic Landscape page: 42
- Electric Motors for Marine Applications page: 44
- Overcoming the Propeller Supply Bottleneck page: 46
- Tech File: BoomVane - A Powerful Boom Deployment System page: 48
- Marine News Boat of the Month: October page: 49