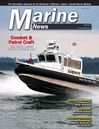
Advanced Greases Can Handle Today’s Deck Equipment Challenges
By Ben Bryant
Anchor winches, cranes, level winders and other equipment exposed to the elements on the deck of a vessel ay look good with a thick, consistent layer of grease, but appearances can be deceiving. In fact, several problems may be lurking below the surface of commonly used greases. For example:
1. Premature wear can occur if the grease is not up to the design loads and speed of the equipment.
- Today’s deck equipment is being pushed much harder over a wider range of operations, resulting in higher loads on gears and bearings that are rotating faster. Advanced, high-performance grease formulations are designed to handle today’s more demanding conditions.
2. Obsolete formulations can’t match the advantages of new lubricants. For example:
- Commonly used thick asphaltic grease will slide off the vertical face of the slewing gear on deck cranes. Alternatives can provide a thin layer which stays in place, improving component longevity and safety on deck.
3. Improper selection of lubricants can occur in an automatic lubrication system. Consider these factors:
- A softer grease used in an automatic lubrication system often performs better than older grease types. A lubricant must either separate contact points with a film or deliver additives that maintain anti-friction benefits even when squeezed out at the point of contact. Modern greases with high viscosity base oils and advanced additives can achieve both objectives.
- Temperature changes can affect grease performance; a grease which is good for the tropics may not flow through the auto-lube system in northern climates. Synthetic base oils in specialty lubricants have a greater operational temperature range.
4. Stocking different lubricants for different applications can get complex. While some high performance lubricants are designed for a narrow set of applications, others perform over a wide range of conditions. A lubrication engineer can sort through the requirements of each application and help rationalize the lubrication inventory while keeping an eye on your operational objectives.
5. Material incompatibility can occur. A recent investigation of seal failures on water tight doors led to a finding that the standard grease being applied softened the seals causing them to tear when the WTD was operated.
6. Eco-friendly characteristics are required when lubricants eventually wash out to sea. This necessitates formulations that are as good in performance in deck equipment as they are for the environment.
Modern lubricants have been formulated to maintain lubrication in today’s challenging marine applications. Key to selecting a specialty lubricant is an understanding of the operating conditions for the application such as load, speed, temperature, type of friction, materials and environmental conditions. In addition, identifying specific operational objectives to be achieved or business issues to be resolved will justify the investment in a specialty lubricant. A lubrication engineer can review lubricant types, formulations and performance parameters to recommend the best lubricant to meet the desired objective or outcome.
The Author
Ben Bryant, Marine Market Manager at Klüber Lubrication NA LP
(As published in the June 2017 edition of Marine News)
Read Advanced Greases Can Handle Today’s Deck Equipment Challenges in Pdf, Flash or Html5 edition of June 2017 Marine News
Other stories from June 2017 issue
Content
- Op/Ed: The Spill Response Industry's Greatest Challenges page: 18
- Anatomy of a Commercial Marine Lender page: 20
- A Legal Approach to Marine Casualty Response page: 22
- Regulatory Growth Drives Search for Durable Lubricants page: 26
- It All Flows Downstream page: 30
- North River Boats: Delivering Flexibility & Customized Output page: 34
- The Right Boat, Right Away page: 38
- Public-Private Project Promises to Revive America’s Marine Highway page: 44
- Autonomous Workboats: The Future is Now page: 46
- Advanced Greases Can Handle Today’s Deck Equipment Challenges page: 50
- Marine News Boat of the Month: June 2017 page: 51