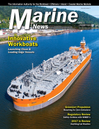
Insights: Emissions Control and Compliance
Marine News
Insights: Alternative Marine Technologies' Robert Kunkel and Chris Mandalakis weigh in on emissions control and compliance
Bob Kunkel needs no introduction to Marine News readers. Kunkel, President of Alternative Marine Technologies, previously served as the Federal Chairman of the Short Sea Shipping Cooperative Program under the Maritime Administration and Department of Transportation from 2003 until 2008. A past Vice President of the Connecticut Maritime Association, he is a contributing writer for Maritime Logistics Professional magazine and of course, Marine News. A graduate of the Massachusetts Maritime Academy, Kunkel sailed as a licensed engineer and eventually continued his career in ship construction at myriad venues.
Appearing for the first time in our pages, Chris Mandalakis is a recent graduate with bachelors and masters degrees in Naval Architecture and Ocean Engineering from Stevens Institute of Technology. Mandalakis has worked on a number of groundbreaking projects including a series of hybrid electric research vessels as an employee of Derecktor Shipyard and Alternative Marine Technologies. He has been involved in Amtech’s newbuilding construction oversight and design review for tankers at HMD in South Korea, and is currently working with Amtech as a naval architect and design integrator for the 2,200cbm LNG bunker barge currently under construction at Conrad Orange Shipyard.
This month, as our featured INSIGHTS subject matter experts, Kunkel and Mandalakis weigh in together on emissions control and compliance, as perhaps no one else in industry can.
This month, as our featured INSIGHTS subject matter experts, Kunkel and Mandalakis weigh in together on emissions control and compliance, as perhaps no one else in industry can.
With EPA Tier 4 here, is there anything else that marine operators can do in terms of emissions reduction, beyond mere compliance? Is the regulatory machine considering still stricter rules? In other words, is this the best we can do?
Many of these questions are still unanswered simply because the regulations on a domestic or international platform are confusing. Yes EPA Tier 4 is here for the larger horsepower engines used for propulsion and with that arrival comes a very limited group of engines that meet the emission requirement. Simply put, no operator likes to be ‘limited’ in selecting machinery in a new construction project. The game changed on January 1, 2016 for engines rated between 130 and 600 Kw and not solely used for emergency purposes. Herein is the problem of regulatory requirements leading industry technology. Based upon our conversation with the EPA and latest construction experience, there are no smaller block engines that meet EPA Tier 4 or IMO Tier III. Keep in mind the IMO Tier III compliance for this engine size is based upon operation in an ECA and many owners are having difficulty receiving an EIAPP certificate because of that issue. The EMA – Truck & Engine Manufacturer’s Association wrote to the EPA, USCG and Transport Canada on July 14, 2015 addressing this very issue.
Most if not all of the current problems the manufacturers are facing is the reduction of NOx and to receive an Engine International Air Pollution Prevention (EIAPP) Certificate the manufacturer must demonstrate the IMO Tier III NOx levels for the ‘family’ engine in service. Hence, the question is not what the Marine Operator can do achieve environmental compliance; it is what can the manufacturers do as many of the operators are not happy with the SCR solution to reduce NOx as it leads to additional operational costs and inefficiencies. The current Marpol Annex VI and EPA Tier 4 regulations are a huge step forward for environmental compliance. Monitoring and reporting stack emissions would be the next logical step and it will lead to new questions and problems. We are facing a generational change in the industry as the new owners and operators look to provide public benefits as part of their business model. All that said; if manufacturers cannot produce the product necessary to meet the regulations, the owner/operators are faced with a very serious problem and that problem is just starting to raise its ugly head.
The IMO and U.S. EPA both have their own version of emission regulations. When it comes to the U.S. coastal workboat sector – U.S. EPA is really the only standard that they have to worry about, yes?
Unfortunately the answer is NO. A domestic newbuild operator accepting an engine that meets the EPA Tier 3 regulations in accordance with the January 1, 2016 keel laying date and does not comply with IMO Tier III Marpol Annex VI is limiting his vessel’s trading or commercial operating routes. The IMO Tier III standards are a requirement in all of the current ECAs. The IMO NOx limits (depending on the engine speed), in Tier II range from 14.4 to 7.7 g/kWh while Tier III limits range from 3.4 to 1.96 g/kWh. In addition to the NOx limits, IMO adopted a HC emission standard of 2.0 g/kWh and a CO standard of 5.0 g/kWh from new Category 3 engines. No emission standard was adopted for PM, but manufacturers are required to measure and report PM emissions. Circling back to the first question, if your ‘workboat’ owner trades domestically he meets the EPA Tier 3 regulations. If however if he decides to work a job in let’s say Mexico, Canada or South America and leaves that U.S. domestic ECA, he cannot return and work U.S. or Caribbean ECA coasts without first installing an engine or SCR to meet the IMO Tier III requirements. Simply put he loses his EPA Tier 3 Domestic pass and is treated like a foreign vessel entering the North American ECA. He must comply with IMO Tier III.
We have found EPA to be very cognizant of this problem and understanding of the fact that no engine in this power range exists to meet those emission requirements. For example, the regulations take into account new construction deliveries in the Great Lakes or repositioning repair voyages to, for example, Mexico, the Bahamas, Canada or South America. They have had extensive discussions in an effort to address the alignment of standards and enforcement for U.S. and Canadian vessels and provided several determinations addressing the issue. The provisions of 40 CFR 1043.10(a)(2) to exempt U.S. vessels from the NOx-related requirements of Annex VI do not apply for vessels that travel even once to ports or waters subject to Canada’s or Mexico’s jurisdiction or for that matter any other country. Annex VI does not apply as a mandatory treaty obligation for the Great Lakes, so this determination does not apply for vessels traveling on the Great Lakes. The USCG as a port state authority is obligated to enforce Annex VI requirements for U.S Flag vessels operating outside of U.S. waters just as they would for vessels flying any other flag. This means that such vessels need to have EIAPP documentation showing that all installed engines above 130 kW comply with the appropriate tier of emission standards under Regulation 13 of Annex VI based on the vessel’s keel-laying date.
Compliance with emissions regulations is one thing; reporting that compliance (and proving it) is yet another. When does it become mandatory, and what will operators have to do to comply? More importantly, what will it cost?
This is a very difficult question to answer. The submittal of Bunker samples and delivery confirmation is already a requirement. The IMO has a pending amendment 317 that addresses the data collection for fuel consumption. At this point, discussions take into account the current review and submittal of bunker deliveries, and looks at how that data can be placed into algorithms taking into the vessel’s EEDI. The project has been described as a very difficult “techno-economic” solution. We have seen demonstrations of stack gas analyzers and would expect the installation of this equipment would be the next step. The next set of dates everyone is struggling with is 2020 to 2025 and the requirements being instituted for that period are already under discussion to delay the next set of emission regulations and fuel requirements. We would expect the mandatory reporting to follow once the actual emissions requirements are set in stone. Placing an arbitrary cost on these regulations is very difficult if you are not looking at a specific vessel design, primary solution (engine type) or aftermarket secondary solution.
LNG is gathering steam as an alternative fuel. Is it the future, and if so, will operators still need after treatment of one form or another to reach Tier 4 compliance?
No doubt we are seeing more and more interest in LNG propulsion system in the larger ship category and LNG is a future fuel consideration – but not so much in the smaller size engines or vessels. IMO has approved the propulsion gas code and ship design considerations are moving past ‘LNG Ready.’ There are space considerations and issues that need to be addressed with safety zones in the applications. Pending keel laying dates and the type of engines installed including dual fuel applications will need aftermarket treatment to meet those later 2020-2025 emission requirements. The most difficult issue is the understanding of the cryogenics and the bunkering application. Simple operations that have been with us for a long time that are now much more complicated taking into account cryogenic temperatures, vapor issues and the understanding that LNG is actually a safe fuel.
Is the key drag on more operators switching to LNG the lack of infrastructure? Or, “if they build it, will the operators come?”
The lack of bunkering infrastructure is a key issue [here] on a worldwide issue. Where gas has been employed in the northern European ferry markets, infrastructure was quickly built and provided where a niche or targeted itinerary or market was identified. With a larger number of operators, particularly in the Jones Act Trade committing to burning gas, commercial availability will help to solve the infrastructure problem. Construction of the JAX LNG terminal is well underway in Florida to support the Tote Marlin Class vessels and we have seen other projects in the non-contiguous trades taking on new discussions of gas availability. Future economics and the cost of fuel will be the next driver. Above all, the key to the slow uptake of LNG is the current lack of a cost benefit. At $50-$60 a barrel, the capital costs associated with burning LNG make it a tough sell. We need to see an economic benefit reaching beyond the regulatory issues.
You’ve been involved in countless newbuild assignments and repower refits. What’s your favorite propulsion system today, why, and is it the panacea for all workboat operators?
Despite countless assignments, there are few of us that can claim unlimited experience dealing with the new EPA TIER 4 and IMO Tier III emission issues. Based on recent sea trials and FAT attendances we are very impressed with the GE L250 and V250 EGR environmental series. Look to this group to solve some of the other smaller engine issues. We have been working with Cummins on their new engine development and our hybrid projects and we see a lot of synergy with this manufacturer. By far, the growth potential in propulsion that we think will outpace all others will be hybrid applications.
Tier “beaters” – the practice of using multiple smaller engines to produce the desired power but staying under the HP of a higher tier engine has been described as good design. What are your thoughts on this practice?
In our opinion – taking into account specific design and project issues – it still is. Using the problems we are seeing in the 130 to 600 kW range – if we can install four 125 kW generators instead of three 145 kW units and circumvent compliance issues – why not? It is all based upon cost analysis and the Owners environmental commitment. We are going to repeat our opinion that shipping and transportation are both going through a generational change. How important will those environmental and social benefits become when compared to profits?
SCR After Treatment: it’s been proven to work, produce tier IV results, and it fits into a tight space (think workboats). A GE engine reaches Tier 4 without it, using EGR. Is one solution better than another for workboats?
As with most choices, there are tradeoffs and please understand ‘proven’ is a gray definition at this point in the installation process. The GE engines are able to comply through the extensive use of EGR or exhaust gas recirculation, and clever manipulation of timing to reduce combustion temperatures and comply with NOx emissions criteria. It is a ‘Primary Solution.’ This, as expected, comes at a cost, in this case, fuel efficiency. SCR or selective catalytic reduction also impacts efficiency, the level of which depends on the system and application. SCR as a ‘Secondary solution’ requires additional equipment to be installed in the exhaust stack – though this equipment has decreased drastically in size as regulation and the lack of a ‘Primary solution’ has driven more to look at the aftermarket systems. Both options have their merits and problems and there is a best choice for every application.
What’s the most viable alternative fuel (beyond LNG)? Why and how likely is it to be adopted in the near term?
If we look at the transit and automotive sectors, there has been varying interest in fuel cells, probably caused by volatile and now historically low fuel prices. Hydrogen fuel cells, made more relevant by an increase in electric powertrain technology, are unique in that, when the hydrogen is generated using solar or other alternative energy source, they are truly emission free. Fuel cells have become smaller and more cost effective as they are produced in higher numbers for transit applications. The maritime industry historically adopted energy reduction and conservation as a means to reduce emissions and meet environmental compliance. We see energy storage as the path forward as it is essential to introducing alternative energy sources; whether fuel cell, wind power or solar. You can’t turn these energy sources on and off like a combustion engine. Bunkering and fuel handling are also issues – we will likely see a similar learning curve with hydrogen (compressed or liquid) as we are seeing with LNG as a fuel.
Methanol, or “liquid gas” is another option being discussed. As clean as natural gas, (though containing fewer BTU’s), methanol does not contain sulfur and can be created from renewable and non-renewable feed stocks. Why hasn’t it taken off faster?
Methanol is a widely traded chemical commodity, is liquid at room temperature, and is capable of meeting current and future Sulphur requirements. However, from an environmental standpoint, when we look at total emissions (fuel production to tailpipe if you will) there is no reduction in GHG production, as Methane must be processed to produce Methanol. Further, though methanol is essentially Sulphur free, NOx compliance is somewhat more difficult – current options include water emulsion in the fuel to decrease combustion temperature, or after treatment. Engine conversions for methanol are similar in complexity to gas burning dual fuel engines, so in many cases, the benefits might just simply not outweigh the costs of a methanol conversion.
Hybrid energy and batteries have come a long way for marine applications – in terms of weight, size (volumetric space taken upon by batteries and the power that they can generate). Do you foresee a time when this will become common on workboat platforms and if so, which ones?
We believe Hybrid and EV technology will be a very significant path forward. Battery technology will continue to drive progress in a number of industries including automotive, aerospace, and certainly marine. We are already seeing hybrid projects ranging from research vessel and coastal shipping newbuilds in the United States and to 1,100 passenger RoPax ferry conversions in Scandinavia. Over 2.5 megawatts of battery power has been installed in single vessel installations. We need to ask a simple question: is the combustion engine dead? The technology had a fantastic run and we see that slow death occurring in the automotive industry as sales of electric vehicles rise. Britain in fact has just announced that all new cars must be zero emission by 2050. GM believes their entire product line could be EV or Hybrid within 5 years. Hybrids have a number of distinct advantages particularly well suited to vessels with diverse operating profiles. Vessels such as PSVs, OSVs, research vessels and others which operate with distinct transit and station keeping or standby periods can utilize energy stored in batteries to avoid idling and underutilized electric and propulsion plants. Such operation is quiet and virtually emission free. Maintenance and fuel costs are further reduced. Look to energy storage companies like Corvus Energy and Spears to lead the way on the battery level. BAE Hybrid has been in this market for years in the mass transit market and has been our selected system manufacturer on several marine projects on the coastal front. Our Harbor Harvest Federal Marine Highway project will employ BAE Hybridrive as our propulsion’s system with Cummins and Corvus Energy.
(As published in the December 2017 edition of Marine News)
Read Insights: Emissions Control and Compliance in Pdf, Flash or Html5 edition of December 2017 Marine News
Other stories from December 2017 issue
Content
- Insights: Emissions Control and Compliance page: 14
- Op/Ed: Real World Infrastructure Needs page: 20
- What Hurricanes Teach Us About Energy Security page: 22
- AIS, AtoN, MTS – and you page: 24
- Hudson River Tales: PAWSA Pauses Parking Project page: 28
- WWII Museum’s PT-305 Sails Again page: 32
- Technology Qualification on the Route to Autonomy page: 36
- Marine News' Top 10 Stories of 2017 page: 40
- Best Workboats of 2017 page: 44
- Tech File: Bulk Barge Cargo Transfer Systems Solution page: 50