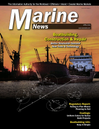
Coating Selection Delivers Fleet Uniformity – Even After Touchups
A 10-tug build project leads to federal standard color update for Great Lakes Towing Company.
Attention to detail enables uniformity. And when you’re refreshing a renowned tugboat fleet with a 117-year history, you want to ensure a uniform look across all vessels to portray a strong brand image. Doing so means achieving uniform coloring throughout the fleet. It also means having uniform colors on each vessel between dry dockings – such that maintenance coatings don’t stand out and make others question your quality.
That’s why Great Lakes Shipyard (GLS) focused on color uniformity when it started building 10 new Stan Tug 1907 ICE tugboats for The Great Lakes Towing Company (GLT). Both Cleveland, Ohio-based parties worked carefully with Sherwin-Williams Protective & Marine Coatings – another Cleveland company – to recalibrate GLT’s Federal Standard colors, which had drifted over time. The three companies also collaborated to color match alkyd maintenance coatings with the polyurethane coatings used to coat the new vessels, ensuring any touchups would blend right in.
Now GLT is realizing fleet uniformity as GLS constructs the 10 new tugboats, the first to be built in the United States to meet new U.S. Coast Guard Subchapter-M Regulations. GLS delivered the first vessel, the CLEVELAND, on June 30, 2017. The shipyard is building the remaining tugs over five years with each vessel conforming to GLT’s new color standards due to the judicious efforts of the shipyard, owner, and coatings supplier.
Recalibrating GLT’s Federal Standard Colors
Entering the tugboat build project, GLT’s primary Federal Standard colors were Red #11350 and Green #14066. However, when comparing color-matched samples from Sherwin-Williams to GLT’s existing fleet, the parties observed a disparity. This color drift had likely originated when GLT switched maintenance coating vendors years ago.
“We compared the coating samples prepared to our Federal Standard colors to our existing tugs and noticed a difference,” said Joe Starck, President of both GLS and GLT. “What we thought was our color standard had actually changed over time, so it was time to recalibrate.” Sherwin-Williams then fine tuned the mixing specifications to match GLT’s fleet, ultimately arriving at Red #11105 and Green #14062 for GLT’s new Federal Standard colors.
Ensuring Uniform Maintenance Colors
While standardizing fleet colors, the companies also addressed color matching between shipyard-applied coatings and maintenance coatings. Initially, GLT had specified SeaGuard 1000 Marine Enamel – a high-gloss, modified alkyd – for coating the new tugs and for performing touchups in service. The single-component coating would be easy to maintain with a pail of the exact same product onboard the vessel – and the colors would obviously match.
However, due to the high-profile nature of the Damen tugs, GLS wanted to achieve better color and gloss retention than what a standard alkyd offers. The shipyard selected Acrolon 218 HS Polyurethane, a multi-component acrylic polyurethane that provides excellent color and gloss retention, including in marine service. The maintenance coating would still be the SeaGuard 1000 alkyd.
Selecting different coatings for the shipyard application and maintenance touchups introduced the potential for disparities in color and sheen, as alkyds and polyurethanes have different formulation attributes. Through several iterations and consultations with GLS and GLT, Sherwin-Williams was able to get the alkyd and urethane coatings to match perfectly.
“We had to look ahead for future field maintenance operations to ensure our colors would be consistent. Otherwise, we would have ended up with more color drift, which we had just solved,” said Starck.
Covering Every Square Inch
A three-man applicator crew from GLS coated the CLEVELAND in various stages, as the shipyard fabricated the tug in two modular units – the hull and the pilot house. Following this construction method, compared to building the vessel as one complete unit, offers advantages for corrosion protection. Vessels built in one piece often have difficult-to-reach areas that applicators may miss or not coat sufficiently, which increase the potential for corrosion.
After metalworkers fabricated the two modules, coating applicators prepared the steel to SSPC standards to remove any contamination, promoting a strong coating bond. Applicators next primed both modules with corrosion-resistant Macropoxy 646 Fast Cure Epoxy coating at 5.0-6.0 mils dry film thickness (DFT). Then, they brush-applied an additional accent-colored stripe coat of the coating on all welded seams for added corrosion protection.
The shipyard next welded the two modules together and stripe coated the disturbed areas. Finally, applicators coated the entire vessel as one unit for a continuous layer of corrosion protection. Applicators spray-applied a 3.0-6.0 mil DFT layer of Acrolon 218 HS over the entire vessel, using the approved Red #11105 for the pilot house and Green #14062 on the freeboard and bulwarks. GLS also used Acrolon 218 HS in other ancillary colors for deck areas and safety markings.
Due to some quick additional color matching, GLS was also able to spray-apply a continuous coating layer in the vessel’s engine room to enhance corrosion protection there. The shipyard decided on a whim to coat the room’s floor using the same deep blue color as the vessel’s MTU engines. On a Saturday morning, GLS called Sherwin-Williams with a request to match the engine color, which wasn’t part of the original specification. The coatings supplier was able to match the color and sheen and provide materials on the same day of the request, allowing GLS to stay on schedule. Doing so allowed the shipyard to coat the engine room before installing equipment, which meant applicators faced limited obstacles and were able to ensure complete coverage.
“Sherwin-Williams matched the engine color and sheen perfectly. The engine looks like it is part of the boat,” said Starck. “It was only a few gallons of paint, but the quick turnaround made all the difference in beautifying the engine room, while also ensuring every square inch is protected.”
Towing Ahead
GLS is currently the only U.S. shipyard authorized to build Damen’s Stan Tug 1907 ICE design. The CLEVELAND will serve as the basis of design for future Damen builds, including the additional nine nearly identical vessels for GLT. Based on its experience with Sherwin-Williams, GLS has a trusted local coatings supplier that will likely make the specification list for additional Damen tug builds, in different potential Federal Standard colors, of course.
“Partnering with Sherwin-Williams brought three strong Cleveland companies together to enhance ship building, repairing, and assist operations throughout the Great Lakes region,” said Starck. “They demonstrated the technical service capability to address our color drift and match new-build coatings to maintenance coatings, as well as the ability to be responsive to fast turnarounds.”
With the towing company’s new Federal Standard colors on file with Sherwin-Williams, GLT tug operators can now obtain color-matched maintenance coatings at any port where a company paint store is located, ensuring ease of maintenance.
The Author
Rick Gallenberger is Great Lakes Regional Marine Specialist for Sherwin-Williams Protective & Marine Coatings. He is NACE Level I Certified and has been with Sherwin-Williams for 29 years, including the last six years as a dedicated marine representative. He works with fleet and vessel owners to help protect their assets, along with servicing shipyards and contractors to promote efficiencies with their coating procedures.
(As published in the April 2018 edition of Marine News)
Read Coating Selection Delivers Fleet Uniformity – Even After Touchups in Pdf, Flash or Html5 edition of April 2018 Marine News
Other stories from April 2018 issue
Content
- By the Numbers: Barge Transportation Market page: 10
- Interview: Robert Kunkel, Alternative Marine Technologies page: 14
- sVGP Compliance Difficulties Continue for the Workboat Sector page: 20
- Op/Ed: California's Zero-emission Domino Theory page: 24
- Boatbuilding 101: Keep It Simple page: 26
- Ballast Water Regs: Difficult and More Difficult page: 32
- Victaulic & SSI: Designing a Marriage Made in Heaven page: 38
- 'Best of the Best' Welds Help Metal Shark Succeed, Expand page: 42
- Factoring Life Cycle Variables Enables Intelligent Motor-drive Purchases page: 45
- Tech File: Material Handler Boosts Paducah’s Productivity page: 47
- Coating Selection Delivers Fleet Uniformity – Even After Touchups page: 48