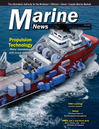
PROPULSION TECH: How to Get to Hybridization
Hybridization in the marine world is transitioning from the latest fad to a key part of vessel design and retrofits.
Driven in part by a demand for increased efficiency and new waves of global legislation, hybridizing or electrifying a vessel is quickly becoming necessary for organizations. In fact, the International Maritime Organization (IMO) rules and guidelines for the marine industry call for reduced emissions globally, and some ports around the world have established ambitious goals to reduce emissions to zero percent.
Early adopters of electrification and hybridization are already reaping the rewards and realizing positive returns on investment – including real savings and benefits to their fleets. Furthermore, they have also gained the knowledge and experience to continue to grow and develop even more hybrid solutions. Considering this, an increasing number of organizations are beginning to evaluate how they can move towards hybridization in their marine applications.
The hybridization challenge
Generally, hybridization can be defined as the coupling of two or more energy sources together to increase efficiency and maximize output. Often, these systems are coupled with energy storage via batteries or super capacitors to help smooth out peak power loads, or even provide peak energy for short-term loads. Further, many companies are replacing fuel-driven propulsion or thrusters with electric motors and using a series of generators to provide power based on demand. This, in turn, means that a vessel only consumes the necessary fuel, and alternate generators that are not required are turned off.
For some, hybridization can seem like an unavoidable risk. But, the first step to developing a successful plan for hybridization is to conduct the thorough research necessary to review your current situation. This will establish the vessel’s needs and provide solutions for the future. Investing in the resources to gather the correct data and establish a baseline of where you are currently is an essential. The plan and data should then be verified through multiple recommendations, as there are varying opinions on solutions and approaches. Knowing where you have been and where you are at will help to set the right trajectory for the future.
The hybridization process can start with a few shaft generators and increase all the way to a fully electrified vessel. Fully understanding and considering the purpose of your vessel will be critical to laying this groundwork. Items such as electric propulsion and thrusters, energy storage, shaft generators and multiple gensets are all puzzle pieces that vessel owners can move in and out of a vessel design. For some applications with short distances and duty cycles, fully electric ships have already been deployed and more are being designed and built for the future.
Benefits of hybridization
By considering the different aspects of the efficiencies that can be achieved, hybridization can enable vessels to reap many benefits. The primary return on investment in a hybrid vessel will be achieved through costs savings related to reduced fuel consumption. However, there are other tangible items to also consider. Hybridization can enable the use of smaller generators where peak loads are handled by battery systems, allowing generators to run less frequently – thus resulting in reduced weight, space, and maintenance.
For example, on a double propulsion system, shaft generators can be incorporated that can both motor or generate. In light duty, one of the two diesel generators could be shut off and powered by the other shaft generator instead. The engine that is running could power both the prop and a generator, while the engine that is off would be unclutched and have its generator switched to a motor. It would still function at a reduced load via the electric motor. This would translate to less operational hours on the two units, less maintenance, and more efficient fuel use.
Another advantage for hybrid vessel systems is performance. Whether using diesel or liquefied natural gas (LNG) engines, the response time to a power request is not immediate. Further, these engines do not adjust well to sudden changes in load. With power electronics coupled to energy storage, response times to a peak power need can shift from seconds to milliseconds. The engines also will not see this sudden change as it would be absorbed by the batteries or super capacitors, and there would be no need to have generators on standby to accommodate these peak loads. Thus, the equipment will experience less mechanical stress and load, which will extend its lifetime and decrease maintenance costs.
Utilizing smaller generators, shaft generators and power storage also allows for a higher level of redundancy on the vessel. Having multiple power sources and multiple electric motors can mean that vessels will still be able to operate at reduced loads in the event of a system failure. Take the two-propulsion shaft generator example above. If one propulsion motor has a fault, the shaft generator could be switched from a generator to a motor. Auxiliary generators, or the main propulsion generator, could then bring the vessel back to harbor for repairs via the electrical motor; all without a costly tug or tow.
Operating these multiple power sources will require the proper power management infrastructure. When these systems are designed correctly, they will be programmed to address the specific lifecycle of the equipment as well as help crews troubleshoot with ease. Many companies have invested a lot of resources into research and development to create control systems to help vessel operators run at peak performance and peak efficiency. However, it is still imperative that the integrators delivering the hybrid system have experience and tested power management software. The most cost-effective solution (up front) may not necessarily be the best or most cost-effective in the long run.
Weighing all the variables
There are a lot of benefits to hybridization; however, there are also some additional costs that need to be factored in. Batteries, super capacitors and power electronics require a different approach to maintenance. They also have different lifecycles and can require a specialized skill set to service. Getting crews trained will also need to be a vital part of the equation when considering the transition to hybridization. Troubleshooting a broken hydraulic line, for example, is a drastically different task than a broken wire. Also, there will need to be a different approach to stocking spare parts on the vessel as some will have special guidelines for maintenance. Therefore, when it comes to hybridization, having the right partners means more than just finding the right suppliers; it must also include partnering to have the right people on board.
In fact, these partnerships—and having a concrete goal and plan in mind—are key items for success in navigating the multiple approaches to hybridization. An in-depth approach must be taken and planned out carefully. Once establishing what your approach will be for a hybrid vessel, finding experienced partners who will walk alongside you in the journey is the next key step. Climbing the mountain is easier done when you have not only defined a strong vision, but also when you partner with others who have already experienced it.
Jon Mosterd is currently a member of the North American Center of Excellence at Danfoss Drives. Alongside his team, Jon helps to support Integrators, OEMs and end users with their marine and heavy industry applications.
This article first appeared in the July 2019 print edition of MarineNews magazine.
Read PROPULSION TECH: How to Get to Hybridization in Pdf, Flash or Html5 edition of July 2019 Marine News
Other stories from July 2019 issue
Content
- INSIGHTS: Edward C. Schwarz, ABB VP of Sales, New Builds page: 14
- Successful Sustainability Starts with … Lubricants page: 22
- OP/ED: A Measured Response page: 26
- PROPULSION TECH: How to Get to Hybridization page: 28
- PROPULSION: ‘Power’ to the People page: 31
- Maritime Simulation & Training: a partnership that pays off page: 40
- All Aboard with Fire Safety page: 44
- OP/ED: Stronger Together page: 46
- Lowering Shipbuilding Costs with Immersive Training page: 48