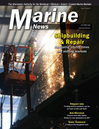
Page 43: of Marine News Magazine (October 2020)
Shipbuilding & Repair
Read this page in Pdf, Flash or Html5 edition of October 2020 Marine News Magazine
COATINGS AND CORROSION made to develop new chemistries for lower volatile organic which a particular organic compound gives off suf? cient compound (VOC) products that had no track record of vapor to ignite in air) below 95*F.
? eld performance. There are also requirements around ease of application,
By contrast, MPI standards de? ned what good looks including viscosity, pot life, dry time, condition in can, like, by de? ning the level of performance the product storage stability and ? neness of grind. should provide based on a regimen of tests tailored to each type of coating. MPI standards are classi? ed around basic
TESTING AND paint types such as alkyd versus latex, and clear versus pig-
PERFORMANCE PARAMETERS mented, with the requirements to pass these standards be-
Performance tests in the series include: ing virtually agnostic to the composition. This protocol of approving products based on performance gave speci? ers
Knife test: Adhesion is veri? ed by measuring the coating an invaluable compass with which to navigate the sea of system’s resistance to a cutting force. new low-VOC and water-based products.
Reverse impact test: The lining’s ability to maintain in- tegrity and adhesion is measured if the exterior of the tank 2. A strong lab testing/approval program gets dented. The uncoated side of the test panel gets ham-
Products approved by MPI were proprietary paints sup- mered, and the coated side checked for cracking or any plied by a wide range of industry suppliers with distribu- other loss of adhesion greater than 15 mm in diameter.
tion capabilities across the U.S. and Canada. This list of
Fuel and water resistance: Test panels are immersed for approved products offered the Navy ready access to source 21 days in glass jars containing a mix of JP-8 fuel and dis- the products they needed.
tilled water. The surface is then checked for blisters, dark-
Over the course of three days, Naval paint experts re- ening, or any indication of loss of adhesion (like softening).
viewed MPI standards and, ultimately, the decision was
Color: The difference in color between the primer and made for the Navy to adopt MPI standards and Approved the topcoat helps the inspector verify the coating’s cover-
Products Lists.
age, which is far more crucial with linings for immersion service than paints for atmospheric service.
APPLICATION OF THE MPI 500 SERIES
Immersion testing: Coated panels are submerged in vari-
With more than 70 bases worldwide that can span areas ous fuel/water mixtures at an elevated temperature for 180 up to 149,000 acres in size, the Navy owns a vast invento- days to simulate extreme usage condition ry of POL systems. These are considered among the most
Freeze-thaw stability: Coated panels are exposed to a 30- critical of land-based Navy assets in terms of a combina- day cycle of freeze/thaw that includes 16 hours at -30°C tion of risk from corrosion; the need for continuous direct followed by 4 hours at 50°C. support of base operations; and the life cycle cost effective-
Accelerated weathering: Coated panels are tested for ness of utilizing appropriate corrosion control systems.
50,00 hours according to ASTM D5894, varying between
Exterior corrosion such as pitting and surface erosion a UV/condensation chamber and a salt fog/dry chamber. on above-ground POL facilities can occur due to the fol-
Panels are evaluated for rusting and blistering every 1,000 lowing atmospheric effects: temperature, humidity/at- hours during the process. mospheric moisture, precipitation, salinity, topography, ultraviolet (UV) light, winds, chloride deposition, sulfur
CONCLUSIONS dioxide deposition and other pollutants.
With the adoption of new robust standards, the Navy has positioned itself to protect its fuel-related assets includ-
OTHER COATING REQUIREMENTS ing transportation and storage of fuels, fuel tank interior
In addition to rigorous performance testing, the 500 structures, steel sheet piling, and other steel waterfront
Series includes material-based requirements that im- structures for many years to come. Consideration was giv- pact personal and environmental safety as well. Products en to both performance in the ? eld and the safety of those submitted must be free of lead and chromate, benzene, applying the coatings. These standards are such that adop- chlorinated compounds, or ethylene-based glycol ether tion by other organizations would be simple and save the and their acetates; have a maximum VOC of 340 g/l (2.8 associated organization the time and effort spent specify- pounds/gallon); and have a ? ash point (the temperature at ing, testing, and evaluating coatings for their use. 43 www.marinelink.com MN