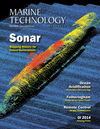
New MASK Unveiled
This facility makes waves … literally
Before sending a new ship to sea it helps to know how well it will perform, especially in rough seas. Testing and improving the seakeeping qualities of ship designs is an art that requires a combination of computerized modeling and simulation, scale model testing in a wave making tank, and actually taking a ship to sea.
The modernized Naval Surface Warfare Center’s Maneuvering and Sea Keeping (MASK) wavemaker was unveiled at a dedication ceremony on Dec. 19 at the NSWC Carderock Division’s West Bethesda, Maryland, facility. The MASK is named for long-time Carderock hydrodynamics pioneer, the late Harold E. Saunders.
The upgraded facility, which replaces an obsolete wavemaker, is housed in a dark, cavernous building with an arched rood like a giant Quonset hut. Every note of the national anthem, sung by Peter Eobbi of NSWC Carderock’s Ship Systems Engineering Station in Philadelphia seemed to hang in the air.
Although not as large as Carderock’s famous David W. Taylor Model Basin tow tank, the 12 million-gallon MASK basin will allow researchers to test how ship designs handle in every possible sea condition.
The basin is 360 feet long and 240 feet wide and can accommodate scale ship models up to 30 feet in length. The dark blue-green water is about 20 feet deep except for a trench where the water is 35 feet deep for testing submarine models.
The waves are generated by a system of 216 electro-mechanical panels called wave boards. The new system replaces the old pneumatic system installed when the facility was first opened in 1961.
An overhead carriage can “tow” the models, although most models today are self-propelled and operate with remote control.
The upgraded facility, completed at a cost of nearly $25 million, has not been used to test a ship model yet, but officials say that will happen starting in March.
Although a state-of-the-art facility when built in 1961, with the old mechanism, waves could only be generated in one direction. “Now we have the precision and ability to generate more precise and different wave patterns,” said Tim Arcano, PhD, Carderock’s technical director.
The waves are generated by the individual wave panels moving together along the side of the pool. They not only create wave patterns, but can be used to dampen waves and return the pool to a flat surface.
“We get so much more out of the tank with the new wave maker paddles, and much better and productive use of the testing time,” Arcano said. “It used to require a 15-20 minute wait before starting the next run. Now it takes about 45 seconds to return the basin to normal. This time frame that allows us to start the next test run 45 seconds later is totally new for us.”
“We develop realistic naval ship models up to 30 feet run them through different types of waves in order to run them through the stresses before they would actually encounter them at sea,” Arcano said.
The active panels impart and absorb wave energy to induce and reduce the waves; permitting the creation of different headings, wave-heights, periodicity and event “focused wave events” not found naturally in the ocean environment. As part of the demonstration, a crowd-pleasing, not-found-in-nature “donut wave” was generated.
“The control we have over these waves is amazing,” Arcano said. “For both in-service and future ships, we can test here in a small scale in our basin and identify safe operating envelopes for our ships and validate the environments that the ship might operate in.
Arcano said that Carderock has performed hydrodynamics testing on virtually every single ship platforms in the Navy fleet in the MASK facility. “The modeling and simulation, testing and design of almost every Navy ship all started here at Carderock. We have been able to validate the designs and dramatically reduce risk,” Arcano said. “We’re looking forward to testing the new ship designs here.”
According to Jon Etxegoien, head of naval architecture and engineering department, Carderock engineers and scientists will use the new MASK facility along with the 3,000 foot high speed and deep water towing basins and the Large Cavitation Channel in Memphis to study advanced hull forms and ship designs for seakeeping studies and survivability at sea. “There’s a small degree of overlap, but each facility has its own unique features.”
“We’ll do straight line testing for resistance and power in our long basins. We can test the hull for response amplitude with uniform waves, then start increasing the period or height and looking at how the ship reacts to that,” said Etxegoien. “But here we can conduct maneuvering and control to evaluate a hull’s seakeeping qualities. We can see how it reacts to different sea conditions.”
“We used to mount the models on the carriage and run them at different headings into a sea, obliquely to a sea, or with a following sea. Now, with new wave maker, we can actually control the angle of the waves. We can simulate a more natural sea state, such as wind-driven seas with a swell from one direction. If we expect a ship to be deployed to an area with a lot of big swells we can test and see how that design will handle that situation, and see how it responds to really adverse situations,” said Etxegoien.
When Carderock engineers evaluate hull designs, they first build a computer model. Then they conduct testing with scale models, which informs the model. Then they test in real conditions, and reality informs both. “With new wavemaker, we can test and make sure our simulations are good,” said Etxegoien.
The new system will make testing simpler, Etxegoien said. “It used to be a difficult system to use over long tests, requiring very experienced operators. You couldn’t change angle of waves, so we would have to change the angle of the model. We couldn’t create the steepest waves. The new wavemaker will be much easier to use and allow for more complete testing.”
Etxegoien said the navy knows a lot about the kinds of seas its ships may have to sail upon. “We can create what we might expect to find because we have that data. We have 20 years of experience of on increasing and improving the data of the conditions in those areas where we expect to operate.”
There are other wavemaking facilities for performing hydrodynamic testing of ship models—such as in the Netherlands, Germany, China, Japan and Brazil—but Arcano said none can do what the Carderock team is able to accomplish today. “This is the most advanced of its class in the world.”
As a major component and field activity of the Naval Sea Systems Command, the Carderock Division is the Navy’s center of excellence for ships and ship systems, providing cradle-to-grave technical support for surface and undersea platforms. Carderock is the full-spectrum research and development, test and evaluation, engineering, and Fleet support organization for the Navy’s ships, submarine, military watercraft, and unmanned vehicles.
The Carderock Division consists of approximately 3,200 scientists, engineers and support personnel working in more than 40 disciplines ranging from fundamental science to applied/in-service engineering. The Hydromechanics Department researches hull forms, propulsion and ship dynamics to provide the foundation for new ship and submarine designs.
In delivering his keynote address as the “grand opening” ceremony for the upgraded facility, Dr. John Holdren, director of the White House Office of Science and Technology Policy Saluted Carderock for its spectrum of work from fundamental science to direct technical support of Navy acquisition programs and operational units, to include work to reduce acquisition and operating costs.
Holdren acknowledged that global competitors are focusing on science and engineering, making it vitally important for America to “maintain the intensity of our own investments [in science and technology] so we can keep our national security science and technology base healthy and ready to respond whenever needed.”
The MASK is named for the leading American hydrodynamicist of the 20th century, Harold E. Saunders, who was also a Navy captain and a member of two of Admiral Byrd’s expeditions to the Antarctic. Members of the Saunders family were present at the ceremony.
(As published in the March 2014 edition of Marine Technology Reporter - www.seadiscovery.com)
Read New MASK Unveiled in Pdf, Flash or Html5 edition of March 2014 Marine Technology
Other stories from March 2014 issue
Content
- Europe’s Seas Under Threat page: 12
- Human Powered Subs page: 14
- UK North Sea Activity Report page: 16
- Bibby Offshore Invests in Fleet page: 18
- CSS Olympia Delivered to GranEnergia page: 18
- Blyth Workcat Joins Osiris Projects Survey Fleet page: 20
- Sonar & the USCG page: 22
- Five Minutes with Hydroid President Duane Fotheringham page: 26
- Advances in Robotic Vehicle Technology page: 32
- There’s an App for That! page: 38
- Expect the Unexpected: Acidic Oceans page: 44
- X (Prize) Marks the Spot page: 52
- D-Day Mapping Mission page: 56
- 3D Imagining: Real-time with SAS page: 62
- I can see clearly now ... Via Resolution Optics page: 66
- New MASK Unveiled page: 72
- Interview: Global Diving & Salvage CEO Devon Grennan page: 76
- MacArtney's Record Growth in North America page: 83
- OI 2014 Technology Preview page: 84
- Sonar Image Stabilization A Powerful Tool page: 88
- Scanning Sonar for Search and Survey page: 88
- LiDAR Ordered for Wind Farm Development page: 88
- New Compact in situ pCO2 Sensor page: 89
- BIRNS Millennium Connectors page: 89
- New Survey Interface page: 89
- Engineered Syntactic Systems Expands Buoyancy Offering page: 90
- Sonardyne Ranger 2 Chosen for Russian Salvage Vessel page: 90
- New Broco Underwater Cutting Rod page: 90
- Shark Marine Launches D.A.S. Boat page: 91
- Kongsberg Camera Systems for OOI page: 91